Selecting clean doors for pharmaceutical and food operations
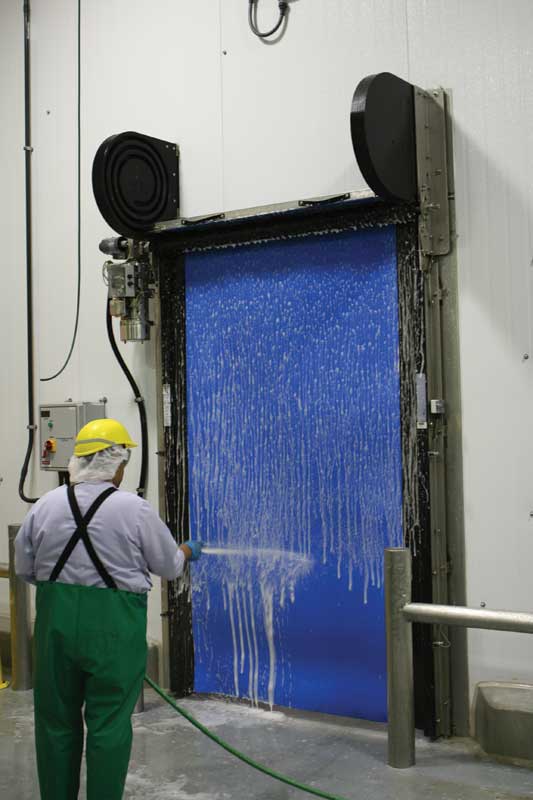
High-speed doors and fabric walls in the food industry
High-speed doors also play an important role in maintaining cleanliness in the food industry. New food industry-specific variations have been developed that meet USDA and FDA standards for cleanup. These types of doors are made of smooth polypropylene (PP), which provides higher resistance to acids and bases and a lower water absorption rate than vinyls and urethanes. This quality makes them highly resistant to mould and offers superior wash-down durability.
Other food-specific enhancements include:
- wash-down-rated sealed drive systems and controls;
- one-piece ultra-high-molecular-weight (UHMW) polyethylene plastic radial headers; and
- noncorrosive polycarbonates and UHMW side frames, which stand off from the wall to minimize surface-to-surface contact and reduce pockets where bacteria can grow.
Fabric walls or industrial curtain partitions also play key roles in maintaining sanitary conditions in the food industry, where they are increasingly being used for applications related to blending and mixing, or production operations involving powder or raw ingredients.
While USDA and FDA do not specify cleanroom regulations in the food industry, they do provide guidelines based on Hazard Analysis & Critical Control Points (HACCP) best practices. As such, designers should seek out products that specifically cite their compatibility with these protocols. One of the most common uses for industrial fabric walls in the food industry is for the isolation of production lines so they can be cleaned while other lines nearby continue to run at peak efficiency. Not only do these flexible fabric walls allow plant engineers to easily enclose areas and contain overspray from cleaning, but they can also help reduce potential for cross-contamination during production processes.
Some wash-down fabric walls are constructed of durable, cleanable, anti-microbial vinyl specifically designed for use in operations where compliance with federal food regulations is paramount. To eliminate the potential for harbourage concerns, fabric walls with manufactured panels with heat- or radio-frequency (RF)-welded seams and airtight/watertight panel-to-panel connections should be employed.
Wash-down fabric walls are typically suspended from existing ceiling structures or roof decks. Stainless steel components and hardware allow the walls to hold up to wet and harsh conditions that occur when production equipment is cleaned as part of HACCP best practices protocol. Should the ability to open and close the wall be needed, heavy-duty stainless steel track and trolley systems are available to ensure easy operation and durability in the wash-down environment.
Flexibility and potential cost savings are among the main benefits of fabric walls in any application. Since they are not rigid, they can easily be custom-designed to match a facility’s specific needs or workspace. Further, they can be moved or reconfigured if those needs change. When combined with anti-microbial wash-down features, this flexibility allows plant managers to achieve cleanliness protocols and production goals without the cost, permanence, or space requirements of rigid walls.
Conclusion
Pharmaceutical cleanrooms and food processing centres demand the most sanitary operations and equipment to ensure quality products. While the strictest FDA, USDA, and HACCP guidelines require the cleanest of processes, recent technology is up to the task.
From high-speed roll-up fabric doors to anti-microbial wash-down fabric walls, new products are changing the way these industries keep their facilities up to code and help provide the highest-quality products.
Jon Schumacher is the director of marketing for Rite-Hite Doors. He has been with the company for 20 years and is a former vice-chair of the Door and Access Systems Manufacturers Association (DASMA). Schumacher can be reached via e-mail by contacting jschumacher@ritehite.com.