Salvaged copper adds drama to library
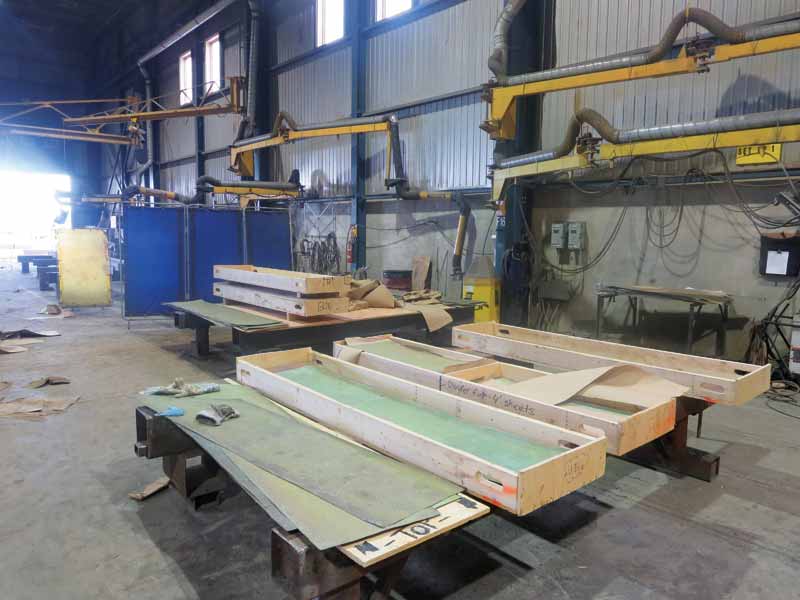
Photos courtesy NORR Ltd.
Recovery
It became apparent to the project team they needed to spend as much time on the design of the recovery, sortation, and preparation of the reused material as on the design of the actual solution. The first goal was to maximize the amount of copper removed by saw cutting as close as possible to the standing seam of each panel. The sheets were then stacked in crates, stored, and numbered. The material’s use was based on a survey of maximum size of panels recovered and, of course, lengths. At this point, the design team was unaware 30 per cent of the panels were 1.2-m (4-ft) lengths instead of the preferred 2.4 m (8 ft). The other concern was the quality of the green patina and whether it was consistent across all the panels. Therefore, all the pieces were assessed and sorted (usable or not) to calculate the total number of panels available for the intended design.
Initially, the team felt it had 80 per cent more than what would be needed. However, in the recovery process, and because of labour issues, storage mistakes, sortation of less-desirable pieces, as well as surprises related to useable lengths and sizes, the design team ended up with only five per cent excess. The author recommends designers plan to recover 100 per cent more material than what is required for the final design in future recovery programs.
The final part of the recovery was to take the oil-canned site material—stored in long, flat crates—for rolling and flattening prior to fabrication into the new design. At this point, the energy inputs included labour and power for sawing the panels, moving material to the fabrication shop, and flattening the sheets in a roller machine. These inputs are minimal when compared to buying new material.
Panel design
The base perforated copper wall panels start 2.4 m (7.10 ft) above the library floor. The room measures 21 x 12 m (68.10 x 39.4 ft) for a total area of 705 m2 (7588.5 sf).
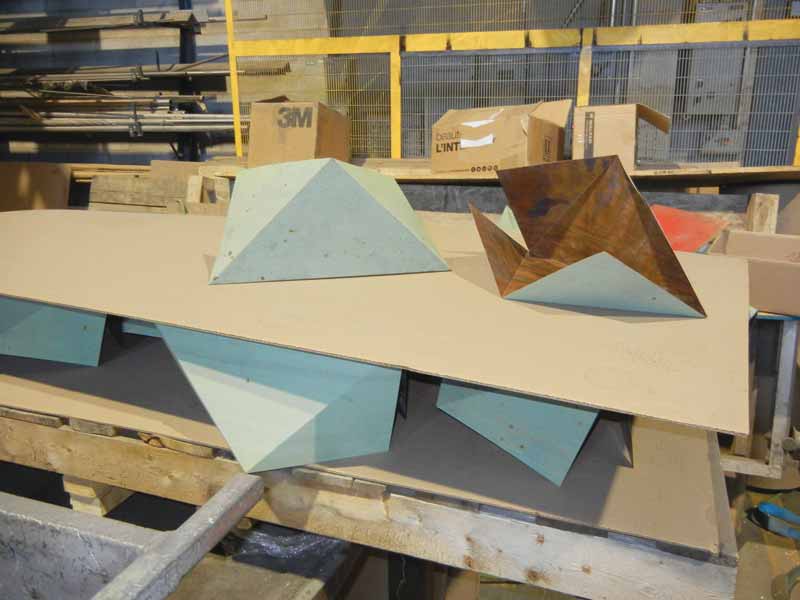
The starting point for the design was the available amount of recycled copper sheets. After removal and inventory measurement of all panels, it was established the maximum design module could be no more than 2.4 m x 406 mm (8 ft x 16 in.) per copper sheet. This established the modulation. All of the wall copper panels were initially roller flattened and perforated to enhance acoustic properties. To prevent oil canning in a 406-mm wide sheet and to assist in sound attenuation, the design team also decided to break press the panel in the middle and return it at each edge to fix it to a back panel. The continuous break at ± 203 mm (8 in.) at each end stiffens the copper panel, making it extremely rigid over the long 2.4-m lengths. The sheet became a “C” panel approximately 406 mm wide x 2.4 m long.
Following the break pressing of the perforated sheet copper, the back side was lined with acoustic insulation fabric. This is essential for sound absorption; sound gets captured as soon as it reaches the perforated holes. The insulation also seals the hole from dust or air moving in the cavity. The floating shells also act as sound baffles, reflecting and trapping noise in the back, perforated wall panel.
The individual 406-mm x 2.4-m long copper sheets were shop-assembled vertically on aluminum panels approximately 3 m (9.8 ft) wide and ± 1.7 m (5.5 ft) high. The aluminum structures were constructed of 50 x 50-mm (2 x 2-in.) aluminum with an additional 3-mm (1/8-in) aluminum back panel. These perforated panels are designed to be picked up and erected to very tight tolerances onto a structural steel framing system. A gap of ± 152.4 mm
(6 in.) between the vertical panels allows some tolerance, but in essence, near perfection is required to set the panels in place.