Roof repair vs. replacement: When is it time?
by Allen Lyte, B.Tech., C.E.T., RRO
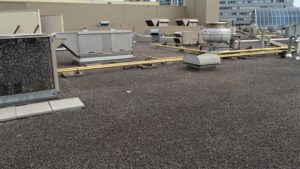
Determining the timing of an appropriate roof management approach is one of the most critical decisions a property manager can make. The cost to fully replace a roof can strain budgets. Deferring the decision to properly repair or replace a roof when required can result in collateral costs associated with interior damages and concealed deterioration of building components. Regular roof maintenance is mandatory, but as a roof approaches the end of its serviceable life, additional repairs should be completed to address specific defects to achieve long-term performance. Implementing repairs to manage roofing assets can help defer full roof replacement and allow options to renew the existing roof. This article focuses on low-sloped roofs and deals with telltale signs when roof work is required and available options.
Know the material
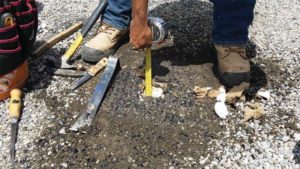
Numerous types of roofing materials are employed to construct the roof assembly. These materials shed water and provide thermal resistance and air/vapour control. The order in which the roof membrane, insulation, and vapour retarder are installed determines the type of roof assembly. Conventional roof assemblies have an exposed roof membrane and are applied over the insulation and vapour retarder, supported by the structure. Protected assemblies, also known as inverted roof membrane assembly (IRMA) or protected membrane roof (PMR), have their roof membrane directly above the structure, concealed and protected by insulation and ballast to hold the insulation in place.
Roof insulation in low-sloped roofs falls into one of the following two groups:
- rigid board in the form of foam, wood, or mineral-based board stock; and
- semi-rigid fibrous boards commonly using fibreglass or mineral wool.
In PMRs, only moisture-resistant insulations can be used since they will be exposed to moisture, and the most commonly used product is extruded polystyrene (XPS).
Vapour retarders can range from polyethylene (PE) sheets, asphalt-laminated kraft paper, modified bitumen (mod-bit) sheet, or simple layers of felt and asphalt. The type of structure and how the insulation is adhered or mechanically secured dictates the most appropriate vapour retarder. It is important to note vapour retarders with waterproofing properties can act as a secondary drainage plane and can defer and/or redirect water from where it breaches the roof membrane to where it leaks to the interior. The roof membrane in a PMR also performs the job of the vapour retarder.
Common roof membranes fall into the following four categories:
- single-ply;
- built-up (including mod-bit);
- liquid-applied; and
- hybrids (a combination of any of the other to utilize the best attribute of a given roof membrane component).
Single-ply
The most common single-ply roof assemblies are either thermoplastic based (e.g. polyvinyl chloride [PVC] or thermoplastic olefin [TPO]) or thermoset (e.g. ethylene propylene diene monomer [EPDM]). The light weight, flexibility, and large sheet size of single-ply membranes make them economical choices for large roofs. Single-ply membranes are installed by fully adhering, mechanically securing, or loose laying them and holding them in place with ballast (Note, ballasted single-ply membranes over insulation are not PRMs). While single-plies can come in a range of thickness, often the thinnest available is utilized making the roof less durable due to risk of damage to the only layer of roof membrane defense.