Roof repair vs. replacement: When is it time?
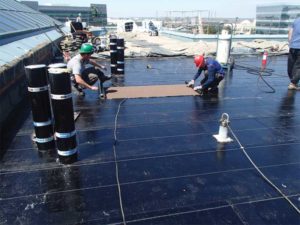
Typical rigid insulations used under conventional roof membranes include foamed plastics, wood, or mineral fibre, and semi-rigid fibre. Polyisocyanurate (polyiso) insulation has the largest market share of the base insulation foams due to its cost versus thermal resistance. However, some feel it does not provide the best substrate for a roof membrane given its low density and dimensional instability. Semi-rigid mineral wool or fibreglass insulation have fair thermal resistance, and while not dense, they are dimensionally stable and have the ability to dry if exposed to moisture. Wood fibreboard, commonly used as cap insulation over the base, is used for its density and dimensional stability instead of its thermal resistance. Wood fibreboard insulation is the most moisture absorbing of these materials and moisture will lower the fibreboard’s already low thermal resistance rating. The greatest cost impact of wet insulation is not the reduction in energy performance, but the effect on the roof membrane’s performance. The roof membrane can develop blisters from the entrapped moisture, creating increased stresses on the roof membrane. Moisture can affect the adhesion of the roof membrane and reduce the wind uplift resistance. Long-term entrapped moisture will reduce the service life of the roof and limit the effectiveness of roof repairs as well as limit options to renew the roof.
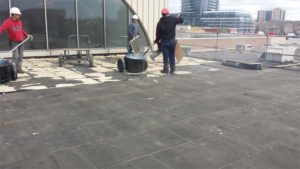
In new construction, the amount of insulation required depends on the type of building occupancy and the geographical location as dictated by building codes. Designing to meet or exceed the minimum current code requirements is the best practice; however, code requirements do not need to be followed when renovating an existing roof. The existing insulation values should be met as a minimum during a roof renovation. Upgrading the base insulation for increased thermal resistance should be attempted where existing upturn clearances under doors, mechanical equipment, etc., permit. Tapered insulation should be included to improve drainage to prevent standing water. Lastly, a durable, dense, dimensionally stable cap insulation should be applied overtop.
Conclusion
Deciding to renew a roof instead of performing full replacement may appear to be a simple choice, but, in fact, involves numerous considerations critical to the success of the building. For best results, building owners should obtain the advice of experienced professionals when determining the best solution. A structural engineer must be engaged if the roof load is going to be increased (such as installation of a new roof top mechanical unit) or the building structural system is being modified.
Finally, replacing a roof can present a great opportunity to protect and enhance an investment. This is the time for owners to evaluate their expectations of their building’s service life. While some building owners simply choose to replace like-for-like, many take this opportunity to change aspects of the roofing system to improve durability and longevity, increase energy performance, and control costs. Long-term investors will benefit from new robust roof assemblies with increased service lives and which require minimal maintenance to achieve the best life-cycle cost. However, if ownership goals are limited to the short-term, renewing the roof in lieu of full replacement reduces capital costs. Increasing the insulation in either scenario will reduce energy costs and should be completed when it meets the owner’s financial model. Again, an experienced professional can help navigate the structural, serviceability, and durability concerns to ensure the most appropriate system is specified for the building and budget.
Allen Lyte, B.Tech, C.E.T., RRO, is a principal partner in the consulting firm W. Allen Partners Inc. specializing in roofing materials, their application, and building science. Lyte is an active director on the executive board, and past president of the Ontario chapter of the Roof Consultants Institute (RCI). He can be contacted at alyte@wallenpartners.com.