Roof repair vs. replacement: When is it time?
When repairing is no longer viable
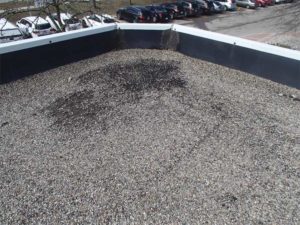
At some point, when the leakage occurrences surpass tolerance levels, continued repairs will need to be evaluated. This varies for every roof depending on the sensitivity of the space and occupants below the roof. When the failures move from a localized incidence to widespread leaks the costs to repair begin to exceed maintenance budgets and are no longer economically viable. Fortunately, once repairs are realized to be no longer feasible there may be options to renew the roof instead of full replacement.
Renew or replace?
Benefits of renewing a roof include reduced costs, condensed construction schedule, less impact onsite, and deferral of roof disposal to landfill sites. However, a roof renewal is only an option if the existing roof has not totally failed and contaminated the entire assembly with water. This comes down to the extent of leakage, type of insulation, and ability to dry. Waterproof vapour retarders or solid concrete structures, for example, prevent moisture escaping the roof assembly.
The service life for the renewal project depends on the building’s long-term ownership plans and available budget.
Renewal strategies
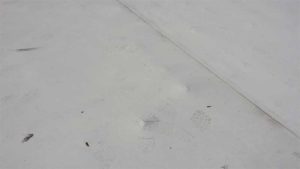
Depending on the condition of the roof, service life/performance, and available budget, there are a range of renewal options based on the type of roof membrane. Asphaltic BURs begin to lose performance with the aging/oxidation process of the asphalt waterproofing component. When the field of the roof begins to show signs of inflexibility and the upturn/penetration flashings are still in good condition, a BUR can be re-saturated. The re-saturation process can help revive the asphalt in the top pour of asphalt forming the flood coat, the primary waterproofing component in a BUR.
Given the upturn/penetration flashings, including upturns at roof edges, are the most common failure points it makes sense to replace these at the time of restoring the flood coat. The change in direction of the roof membrane at these locations increases stresses that can cause localized failure (e.g. splitting membrane seams and de-bonded membrane terminations). When doing a full roof restoration, the re-saturate material is often upgraded to a more robust material to augment the existing flood coat waterproofing. Typically, this involves removing the existing gravel surfacing and fixing defects in the BUR, such as blisters or ridges, prior to roof membrane renewal.
The advancement of liquid-applied products provides the opportunity to fully coat existing smooth-surfaced roofs. Single-ply, mod-bit, and existing liquid-applied are best suited for this renewal option. BUR would need the gravel surfacing removed. The fully bonded nature of the liquid-applied overlay helps prevent inter-ply moisture transfer regardless of the moisture being trapped in the existing insulation.
Roof overlays generally refer to the application of a new roof membrane over the existing roof. Depending on the roof assembly and membrane being used as the overlay, it may be applied directly over the existing roof membrane. However, if the existing membrane is too deteriorated and the added weight is a concern, the existing roof membrane can be peeled to expose the underlying insulation. This allows any wet insulation to be more easily identified and replaced.