Roof repair vs. replacement: When is it time?
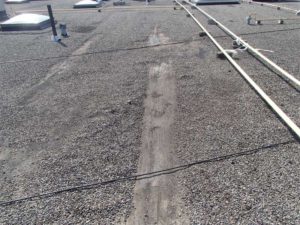
The majority of roof leaks do not occur through the actual roof membrane, but via other rooftop components such as mechanical equipment sitting on or penetrating through the roof. Often replacing inexpensive sealant around exhaust stacks/vents will prevent a leak. This condition can be easily evaluated by building maintenance staff when the sealant is visibly split or debonded. More complex rooftop mechanical equipment often become the source of leakage when condensation trays become clogged and backup, or when failed duct waterproofing allows water to seep in.
Since stress on the roof membrane is greatest at transitions at the roof’s edge it is critical to have durable roof membrane flashings and then protect them with sheet metal flashings. While the sheet metal flashings should be designed as largely esthetic, in addition to protecting the membrane flashings from abuse the drip edges do provide a certain amount of water shedding away from the building. If allowed to deteriorate too far the sheet metal can create a safety concern if it becomes loose and blows off.
PMRs require the least maintenance due to the roof membrane being protected by the overlaying insulation. Clear drainage is critical for this type of roof assembly to avoid displacement of the insulation which could then float on ponding water. Trapped stone ballast between displaced insulation and the roof membrane can cause abrasion damage over time.
Failure modes
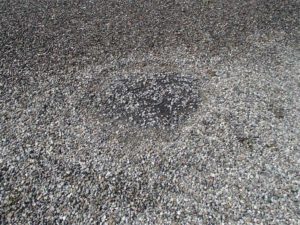
A visible roof membrane can be prone to various modes of failure in an exposed conventional assembly. Bituminous-based roof membranes can develop blisters from entrapped air/moisture and ridges lead to split roofs over time from differential movement. As the protective surface of the bituminous roof wears due to foot traffic, wind scouring, and asphalt degradation, the primary waterproofing layer can be damaged and expose the roof membranes’ reinforcement.
All bonded roof membranes have the risk of de-bonding from their substrate or at their own seams that could lead to eventual failure of the system. Lighter single-ply membranes are prone to punctures, tears, and tenting at areas where the membrane pulls away from upturns (e.g. parapets), thus causing stress on the roof system. When the insulation or the single-ply membrane is mechanically secured the fastener can puncture the membrane from below. Fasteners can “back out” over time as a result of dynamic wind loads. Crushed insulation around fasteners leaves the membrane unsupported and the head of the fastener can then penetrate the membrane.
Liquid-applied membranes can suffer from similar wearing concerns. Since liquid-applied membranes tend to be smooth and lighter in colour, they run the risk of discolouration due to dirt pickup similar to single-ply membranes. Improper installation or excessive wear becomes an issue when the reinforcement of a liquid-applied membrane becomes visible or exposed. Water can wick through this reinforcement layer just like any reinforced roof membrane. Depending on the vapour permeance of the liquid-applied membrane, water blisters can form or the membrane can simply de-bond if substrate preparation is not done correctly.