Role of metal with stucco claddings in high-rise buildings
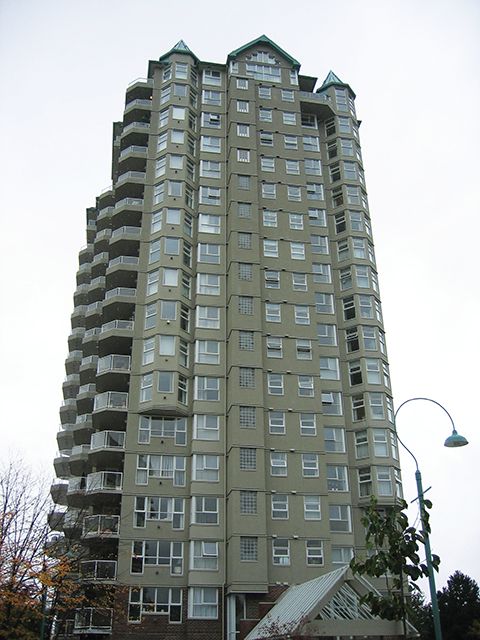
By William Spilchen, P.Eng.
The combination of steel and portland cement stucco has been successfully used in various climates and in applications across the country. Properly specified and installed with a drainage plane, this combo provides a fire-resistant and non-combustible cladding, making it suited for multi-family and other high-rise structures.
Stucco cladding has many attributes and benefits for architectural design, including the versatility to create various shapes and forms as well as curved walls, arches, and other ornamental configurations. Additional benefits of cost-effective stucco wall systems include:
- variety of colours, textures, and finishes;
- achievability of large, monolithic uniform surfaces;
- resistance against impacts, insects, and rot;
- low maintenance with a life expectancy of
50 years or more; - sound insulation; and
- airtightness.
However, these positive attributes cannot be achieved without attention to the proper design and application of the stucco system. Stucco plaster is a mixture of approximately 80 per cent sand, portland cement, hydrated lime, and the appropriate amount of water. Volumetric standards have been developed that regulate the amounts of each ingredient—specifically ASTM C926, Standard Specification for Application of Portland Cement-based Plaster, and National Building Code of Canada (NBC) Article 9.28.6, “Stucco.” Additionally, the quality and cleanliness of the sand is important.
For improved control of the ingredients, some companies provide pre-bagged stucco mixes, even with the sand (dried). Therefore, quality and ratio of materials is controlled by a manufacturer rather than by jobsite mixing and blending that could vary for numerous reasons. On larger projects, silo systems are now available to be set up onsite. Each of the ingredients is automatically fed into a mixer as prescribed. Other additives such as fibres, plasticizers, and other proprietary admixtures are available for improved performance, along with reduced shrinkage and the resulting, decreased cracking.
Much has been learned over the last decade regarding the importance of water-resistive barriers (WRBs) and flashing. Stucco is the primary barrier to the elements, but careful attention is required to prevent water from entering in behind the stucco itself. Water will not readily pass through the stucco, but finds paths around it—into junctions where the stucco stops and abuts another wall element such as windows, doors, or control joints.
Behind the stucco is a secondary, hidden barrier (i.e. a drainage plane); this includes the proper installation of air barriers, vapour retarders, and flashings around penetrations such as windows or doors. Generally, these flashings are the various peel-and-stick membranes available. Detailed instructions are accessible on proper application and shingling, especially at the bottom with the WRB, which would be applied later. Correct application and shingling of the WRB is critical. Appropriate metal flashings are required specifically at the tops of parapet walls. On multi-family buildings, through-wall flashings at each floor level are also recommended.
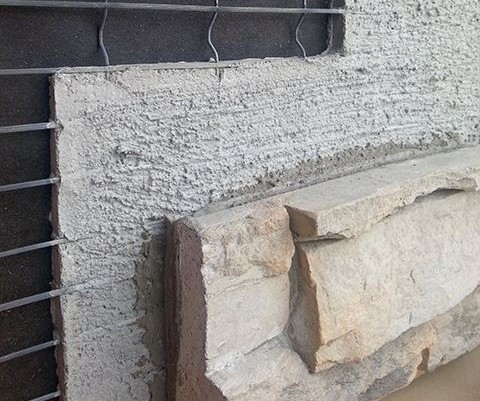
The appropriate metal flashings would consist of combinations of:
- plaster stops;
- through-wall flashing with 50-mm (2-in.) minimum back leg;
- sloping surface to the outside clearing the surface below by 7 mm (0.27 in.) and with 125-mm (5-in.) drip leg with safety edge; and
- window and door head flashings with end dams.
These dimensions are similar to through-wall flashings. The other critical metal components are parapet cap flashings and the correct installation of required control and expansion joints.
The WRB should be applied in two layers as double layers or half laps. These may be asphalt paper—preferably 30- or 60-minute rating—or building wraps. With the latter, the first layer should be a wrap, while the second layer can be an asphalt paper. The purpose of the two layers is to provide a bond-breaker with the layer in contact with the stucco. This allows unimpeded passage of incidental moisture to drain downward between the two layers.
Steel and lath
In Canada, a rainscreen cavity is required—a 10-mm (2/5-in.) interior drainage plan (at minimum) per NBC requirements to dispose of any water migrating behind the stucco. This physically creates an open drainage space to provide for air and vapour movement to achieve drying. The reason for rainscreens is the result of leaky condominiums in British Columbia. Due to high rainfall, much of which could be wind-driven, drainage and drying was inadequate during the annual cycle, which has led to building deterioration, saturated insulation, and subsequent mould problems. The only assured design was to incorporate the rainscreen to offer drainage and drying.
The metal lath is the next critical element of a sound stucco wall. Being a cementitious material, stucco is strong in compression, but weak in tension. Therefore, similar to concrete, steel reinforcement is required to provide the tensile strength.
Lath generally consists of galvanized welded wire in either 51 x 51-mm (2 x 2-in.) grids formed by 16-ga. wires (i.e. 1.5 mm [0.06 in.] in diameter), or 38 x 38-mm (1.5 x 1.5-in.) grids formed by 17-ga. wires (i.e. 1.3 mm [0.05 in.] in diameter). The lath must be a self-furring type and hold the body of the lath not less than 6 mm (0.2 in.) away from the substrate.