Revolutionizing sustainability with HFO-blown spray foam
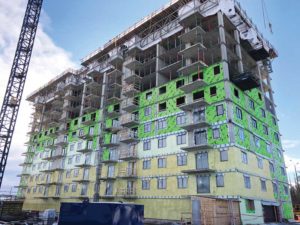
Modern manufacturing processes for HFOs are becoming increasingly efficient, reducing the total GHG emissions during the production phase. Innovations in the manufacturing sector are also driven by increasing scrutiny and regulations, forcing companies to adopt cleaner technologies.
Stringent regulations are pushing the industry toward low-GWP alternatives such as HFOs. The adoption of HFOs can result in tax benefits or incentives for businesses, indirectly contributing to a reduction in GHG emissions by making these materials more cost-effective and thereby encouraging their use.
The growing trend of consumer awareness about the environmental impact of products is driving demand for more sustainable options. The use of HFOs instead of HFCs can become a selling point for eco-conscious consumers, further driving down emissions by encouraging market-driven change.
Understanding insulation materials
Insulation is pivotal in any construction project, influencing the building’s energy consumption, comfort levels, and even its carbon footprint. Traditional insulation materials such as fibreglass and cellulose, have been mainstays in the industry for years.
Fibreglass insulation, which is made from finely spun glass fibres, is a common choice for many building projects. It comes in batts or rolls and is usually placed between studs, joists, and beams. It is favoured for its affordability and fire-resistant properties. However, fibreglass insulation has its considerations. It is not water-resistant and can lose its insulating ability when wet. In addition, fibreglass does not prevent air leakage, which can lead to higher energy bills. It also does not provide vapour control so additional materials are needed, as well as their installation. Installers must also exercise caution to avoid health risks from inhaling or encountering the tiny glass shards
Cellulose insulation, which is made from recycled paper products treated with fire retardants, is another prevalent insulation material. It is eco-friendly in its use of recycled materials and provides good sound insulation. Similar to fibreglass, it is usually installed in a loose-fill manner. However, it also shares some of the same considerations as fiberglass—it does not prevent air leaks or provide adequate vapour control, and is not water-resistant, potentially leading to moisture problems, including mould and decay.
In contrast, spray foam insulation is a modern solution that brings several benefits to the table. This material, applied as a liquid, expands upon contact with the air to form a solid, continuous layer of insulation. This means it can conform to irregular shapes and spaces, providing a tighter seal against air leaks than traditional insulation materials can offer. Not only does it provide high-quality insulation and air sealing, but it also functions as a moisture barrier. This multifunctionality eliminates the need for a separate vapour barrier.
The ecological impact of insulation materials
The ecological impact of insulation materials has become an imperative topic of discussion in the building industry. The evaluation of environmental footprints is not just confined to energy performance, but also includes other factors such as manufacturing processes, raw material sourcing, recyclability, and overall life cycle emissions. In light of these parameters, look and analyze traditional insulation materials and the contemporary HFO-blown spray foam insulation.
Fibreglass and cellulose, as traditional insulants, do have their merits in terms of initial energy savings. Fibreglass, being composed of glass, is made from abundant and natural materials. Cellulose, on the other hand, mainly comprises recycled paper, contributing to waste reduction. However, both materials possess greater environmental considerations when viewed from a broader ecological perspective.