Rethinking Rebar: reinforcement goes green

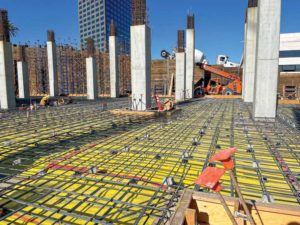
By Chris Bennett, iSCS, CDT, and Aurora Jensen
Reinforcing bar, commonly known as “rebar,” comes in the form of mesh, wires, or bars, and is designed to strengthen concrete under tension. Describing it in a more humanistic manner, one could consider rebar as a part of the muscular skeletal system of a building. Together, rebar and concrete work to resist tensile forces and increase the utility of a structure.1 Without rebar, people would not be able to build high into the sky or safely cross large expanses of water.
However, the embodied carbon generated while creating and transporting traditional rebar is substantial. Luckily, new alternatives to traditional reinforcement are becoming more present in the market and the steel industry is making strides to build more sustainably.
Steel rebar
Historically, reinforcement has come in the form of steel. Common on all manner of job sites, the basic “black” bar is carbon steel rebar. It has high tensile strength, but corrodes easily, making it a poor choice in matrices with high likelihood of moisture exposure. The CSA Group (CSA) G30.18-09, Carbon Steel Bars for Concrete Reinforcement and CSA A23.1:19, Concrete Materials and Methods of Concrete Construction, covers parameters for lengths and coils of various reinforcement. ASTM A615M-09, Standard Specification for Deformed and Plain-Carbon Steel Bars for Concrete Reinforcement, provides additional guidance when needed.
Epoxy-coated rebar is basically standard steel rebar with a thin coat of epoxy. It offers improved resistance to corrosion; however, the coating itself is delicate and chips easily during transport and installation. This leaves affected areas susceptible to corrosion. Guidelines for rebar with protective epoxy coatings are covered in ASTM A775/A775M-19, Standard Specification for Epoxy-Coated Steel Reinforcing Bars.
Galvanized rebar fills a similar role to epoxy-coated rebar, by way of the galvanizing process. Compared to epoxy-coated rebar, some galvanized varieties are not as resistant to corrosion, but they are more difficult to chip and damage. The coating material for galvanized rebar is zinc, which is applied in various thicknesses through a process called “dipping” or “hot dipping.” Bolts, ties, dowel bars, and anchors can all be galvanized. CSA A23.1 refers to ASTM A153/A153M, Standard Specification for Zinc Coating (Hot-Dip) on Iron and Steel Hardware for galvanized steel reinforcement.
Stainless steel rebar has significant resistance to corrosion and does not require mitigating chipped areas like epoxy-coated rebar. This makes it an optimal choice for ease of installation and durability of the reinforced concrete. However, stainless steel reinforcement is traditionally very expensive and typically only found in projects which require long-term defense against corrosion, such as bridges or in geographies with higher seismic activity. It is also more embodied-carbon-intensive than standard rebar, by a margin of more than 10 per cent. In North America, the main standard for stainless steel rebar is ASTM A955/A955M, Standard Specification for Deformed and Plain Stainless-Steel Bars for Concrete Reinforcement. It includes dimensional bar profiles and other information to assist project teams.