Rethinking Rebar: reinforcement goes green

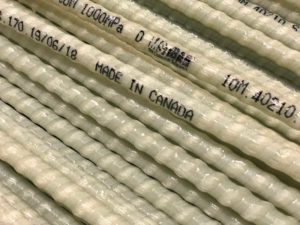
Research suggests the emissions from manufacturing BFRP rebar are 74 per cent less than typical steel and 22 per cent less than 100 per cent recycled content EAF steel. Not only are composites lighter, and in some ways stronger than steel, but they also make sense in scenarios where water exposure is a risk to the long-term health of the concrete system.
One example would be using composite reinforcement in a slab which will also have a hydronic heating system. Hydronic systems embed tubes into concrete, which will carry heated water to warm the slab. However, if there is a leak and the hydroponic tubing is tied to metal reinforcement, the risk of corrosion is certain. Basalt and fibreglass reinforcements do not corrode. While this does not prevent a leak from happening, it will reduce the possible damage the leak will have on the entire slab. Basalt and glass fibre rebar installation standards for composite reinforcement of concrete are described in ACI 440.6-08, Specification for Carbon and Glass Fiber-Reinforced Polymer Bar Materials for Concrete Reinforcement.6
As previously noted, steel and composite rebar do not have identical mechanical characteristics. While composite rebar may have greater tensile strength, it can also have a lower modulus of elasticity than steel rebar. This can limit its application in certain scenarios. It is therefore important to check with the project team’s engineers to ascertain best uses, as well as serviceability limit state (SLS) and any provincial design codes related to sustained loads.
European rebar, produced with large amounts of manganese, has tremendous flexibility and is easy to work with. However, this same workability also makes it unsuitable for bearing heavier loads, extreme thermal change, or the effects of seismic shock.7 However, it can be less expensive than traditional rebar and have a smaller carbon footprint, making it potentially useful on smaller projects in areas with only subtle temperature swings.
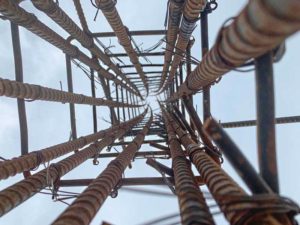
Green steel
Composite rebar is certainly leading the pack when it comes to lowering embodied carbon in reinforcement, but this does not mean the steel industry is not pursuing other changes in the face of climate change. As previously described, newer electric arc furnaces are operating with far fewer emissions than older basic oxygen furnaces.8 Along with modernization of many of the world’s electrical grids, the steel industry’s carbon footprint has been reduced by 36 per cent since 1990, according to the Steel Market Development Institute (SMDI).9
In the present market, specifying suppliers must have product-specific Type III Environmental Product Declarations (EPDs), or specifying rebar producers who are already disclosing their impacts through EPDs are some of the best ways to support data transparency and better data quality, and ultimately drive decarbonization in the steel industry. Sourcing rebar supplied from EAF mills is also advisable, as it will help support the transition to a greater share of EAF production over BOF-milled steel.
Several producers in the industry are also seeking to tackle the challenge of finding electric alternatives to the high-heat processes, which make it difficult to reduce the carbon footprint of steel production.