Rethinking Rebar: reinforcement goes green

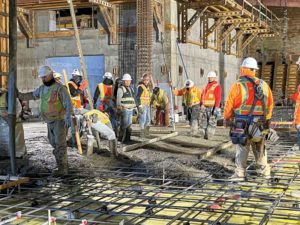
While steel provides excellent strength, its Achilles’ heel is its embodied carbon footprint. The process to produce a ton of steel, in total, creates about a ton of greenhouse gas (GHG) emissions, approximately equivalent to the amount of carbon dioxide (CO2) burned in 40 home barbecue propane tanks. Steel also has a higher embodied carbon footprint (by weight) compared to concrete. According to information from the World Steel Association, steel production equates to six to seven per cent of global GHG emissions.
The main driver of steel emissions is its production process. There are two primary types of steel factories: the basic oxygen furnace (BOF) and the electric arc furnace (EAF). Steel is an alloy of iron and carbon. Legacy BOF furnaces burn fossil fuels to heat iron ore, coke, and limestone to temperatures exceeding 2000 C (3632 F). This is then mixed with 25 to 40 per cent iron and steel scraps to make new steel. Modern EAF furnaces melt iron and steel scraps to create new steel, achieving much higher recycled content rates of 90 to 100 per cent. While EAFs have become the predominant method of steel production in North America, BOFs are still the most common furnaces used around the world.2
Given the high recycled content, steel from EAF production types tends to be about half as carbon intensive as BOF steel. However, reducing steel’s carbon footprint is not always as easy as specifying steel from an EAF factory, as production type is tied to steel shape. Hot rolled steel shapes, for example, are typically produced in EAF factories in North America. However, hollow structural section (HSS) shapes are more likely to come from BOF factories. Rebar can be produced using either BOF or EAF processes, thus sourcing rebar from EAF furnaces should be preferred.
The efficacy of specifying higher recycled content as a method to reduce the embodied carbon footprint of steel has also recently been challenged. Since the amount of scrap steel available is limited, some experts suggest specifying higher recycled content in metal products only arbitrarily changes the manufacturer’s allocation of accounting for scrap shifting the recycled percentage from one buyer to another, rather than creating any substantive change in supply chain practices. Until specifying higher recycled content starts to make steel deconstruction and recovery practices more desirable, and effectively adds more scrap to the system, it is challenging to create change through specifying higher recycled content.
Composite reinforcement
Composite rebar is not necessarily new, but it may not be as widely utilized as it should be. Unlike its steel cousin, composite rebar generally does not have any natural weakness to corrosion, which reduces the risk to the concrete around it. Composite reinforcement is also non-conductive, and in many instances, it has greater tensile strength compared to many types of steel rebar. Additionally, since composite reinforcement is lighter than steel, there are more benefits to the economic and carbon costs of its transportation.
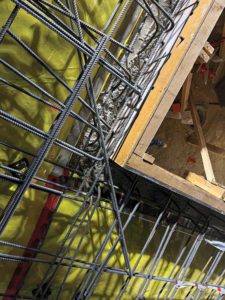
There are two common types of composite rebar: glass fibre reinforced polymer (GFRP) rebar and basalt fibre reinforced polymer (BFRP) rebar. Fibreglass rebar is produced from glass fibres in a polymeric matrix. The polymer makes load transfer to the glass fibres possible, while the fibres themselves carry the load.3 ASTM D7957, Standard Specification for Solid Round Glass Fiber Reinforced Polymer Bars for Concrete Reinforcement, provides guidance for GFRP in structural applications.4 CSA also provides specifics on building with composite rebar in CAN/CSA-S806-12 (R2017), Design and Construction of Building Components with Fibre-Reinforced Polymers.5 GFRP composite rebar is generally considered to be more carbon intensive than BFRP, 100 per cent EAF recycled rebar, but less carbon intensive than stainless steel rebar, galvanized rebar, or standard BOF rebar. Basalt fibre reinforced polymer, sometimes known as “basalt rock rebar,” has higher tensile strength compared to steel and, like fibreglass, is non-corrosive. Basalt rebar also shares concrete’s same thermal coefficient of expansion and can be up to 89 per cent lighter than steel, making its related carbon expenditures in transportation the lightest yet.