Restoration of aging masonry buildings
by Jonathan Dickson, P.Eng., BSS
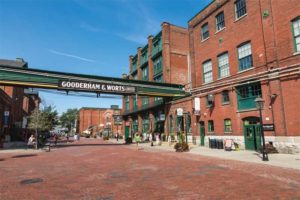
Brick masonry has, and will continue to be, a prevalent building material as it has several desirable attributes. However, it is these same material attributes that can also potentially make brick masonry undesirable for use in the exterior walls of buildings. For example, durability and esthetics can be considered as both positive and negative attributes of masonry depending on the quality of design and installation. The long-term performance of brick masonry enclosures requires technically sound design and quality construction practices supported by diligent maintenance procedures throughout the life of the structure.
Brick masonry assemblies are a combination of brick units and mortar. The brick can be arranged to either form the entirety of the enclosure (mass wall) or as a separate cladding over supplemental control layers of the exterior wall assembly (veneer). Within historical structures, the masonry assembly usually completed most of the required functions of the exterior wall enclosure. Multiple layers of masonry, also called wythes, were employed in these buildings and tied together to create an assembly capable of supporting the structure while providing the required control functions (air and moisture) of the uninsulated exterior wall assembly (Figure 1).

Images courtesy Pretium Engineering
As buildings became insulated (thermal control), a vapour control function was a good practice in cold climates. Buildings also became taller and were required to be more economical to construct. This resulted in the use of other materials for the structure of the exterior walls (e.g. wood, steel, and concrete). Thus, brick masonry went from a structural component used in a mass wall configuration to a cladding material hung off the primary structure in a veneer configuration retained for its durability and esthetics. Regardless of the type of brick masonry configuration, the performance of the assembly requires both the brick masonry unit and the mortar to function as intended.
Mortar
While the mortar joints may occupy less than 20 per cent of the total wall area, the impact to the wall’s long-term performance is disproportionally significant. Modern mortar is a combination of lime, Portland cement, and sand proportioned to achieve desired compressive strengths (Figure 2). Historic mortars are composed of pure lime or are lime-centric and have lower compressive strengths than the modern Portland cement-based varieties.
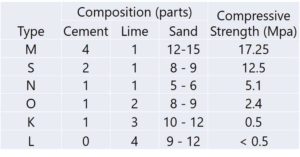
The mortar in the masonry assembly is designed to fail in the sense that should differential movement occur the mortar fails before the brick units in the building. When rehabilitating older brick masonry structures, it is important to maintain this relationship between the bricks and mortar. It is pertinent to note that there could be undesirable consequences when replacing historic, soft mortars with modern, hard ones (Figure 3). If a historic brick masonry wall assembly repointed with strong, modern mortars undergoes differential movement, the path of least resistance will become the brick units instead of the mortar. The subsequent widespread cracking through the units will be difficult to control and repair. Such an occurrence would be significant for a historic building where masonry is often of key esthetic importance.
Best practice #1: Before specifying mortar for restoration of an older masonry building, determine the composition of the existing mortar to decide on the appropriate mortar for the application.