Restoration of a heritage brick clock tower
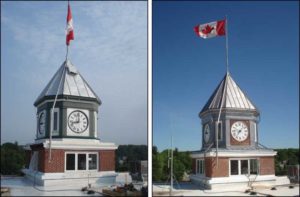
Revisions to brick repair work
The anomalies uncovered on November 7, 2013, and the advanced state of deterioration on the north side of the building prompted a change to the repair approach. The scope of brick repair work was modified to include the full removal and replacement of the multi-wythe brick masonry on all four sides of the tower. Drawings were revised and reissued for construction. Since cold weather had set in, the team had to follow cold-weather masonry construction practices. The scaffolding around the tower was enclosed and heated to ensure the mortar curing temperature stayed above 0 C (32 F). The complete removal and replacement of brick masonry tower walls proceeded one corner at a time to ensure stability of structure during construction. The replacement multi-wythe brick masonry walls were constructed in a similar fashion to the original.
On November 18, 2013, the author was requested to attend the site to review additional sources of active water infiltration. It was raining on that day. Significant water infiltration from the tower roof was noted. A review of the flashing and roof drainage system during the rain event highlighted the flaws of the existing systems including:
- the gutter at the eave of the tower roof was inadequately sized;
- downspout was not connected;
- flashing between the wood panels of the eight-sided tower walls and the flat podium roof was ineffective; and
- the roof hatch was poorly sealed (Figure 4).
The project team discussed the importance of addressing the cause of the observed structural damage and about how the active water infiltration from the upper tower structure had largely contributed to the damage to the wood-floor framing and the brick masonry.
A comprehensive waterproofing system was recommended for the clock tower structure. Since town authorities wanted all modifications to replicate the detail of the existing tower, the following were proposed:
- remove existing rotted material and replace/consolidate
as required; - install new waterproofing membrane over the exterior surface;
- repair exterior wood sheathing of clock tower;
- reclad the structure with copper and lead-coated copper to match existing profiles;
- replace standing-seam steel roofing with lead-coated copper standing seam; and
- add a code-compliant lightning protection system.
The wood cladding required seasonal sanding and painting to mitigate the infiltration of water. The proposed metal cladding system would eliminate the need for seasonal maintenance.
The Town of Huntsville decided they wanted to proceed with the comprehensive waterproofing of the tower structure. A high-temperature resistant, self-adhesive roof underlayment was added between the new lead-coated copper cladding and plywood substrate.
The municipal heritage committee agreed the use of copper and lead-coated copper would be a more durable exterior finish than the existing wood sheathing and would be better for the overall sustainability of the building. The copper and lead-coated copper were to be handcrafted to match the exact profile of the existing clock faces and wood cladding. New eave gutters and downspouts were added as part of the waterproofing work.
The replacement of the cladding and roofing membrane addressed the cause of the observed masonry deterioration. The service life of the newly reconstructed masonry walls is greatly improved with the source of the original damage resolved.
Conclusion
The tower was unveiled in May 2014 after a year of construction and at a final cost of approximately $230,000. A successful heritage restoration project requires collaboration between all parties. The flexibility and ability to focus on long-term sustainability by the Town of Huntsville, the municipal heritage committee, Heritage Restoration, and Ultimate Construction were all critical to the project’s success. The result was a beautifully restored clock tower that matched the detail and profile of the original tower structure.*
*A version of this article was published previously in the proceedings from the 13th Canadian Masonry Symposium in Halifax in June 2017.
Kevin Hughes, M.A.Sc., P.Eng., CAHP, is a structural consulting engineer at Tacoma Engineers Inc. in Barrie, Ont. His areas of expertise and interest include structural and masonry design, building condition assessments, structural repair, and restoration. He can be reached at khughes@tacomaengineers.com.
The specified slider id does not exist.