Flat Roof Ventilation: A Need for a Better Understanding
By Domenico D’Amato, Eng., Antonio Renzullo, Eng., and Domenic Chiovitti, Eng.
The introduction of thermal insulation for residential construction in late 1920s and early 1930s in North America created condensation issues, most notably within residential dwellings of wood frame construction. Typical signs of condensation were noted in the form of peeling wall paint and water-staining within upper-storey ceiling finishes. Although these issues were eventually controlled through the installation of vapour barriers within wall and roof construction, problems within some roof attic spaces persisted. Researchers in the mid to late 1930s indicated the installation of a vapour barrier was sometimes not sufficient to reduce the potential for condensation and the ventilation of attics and roof cavities was prescribed.1
However, the ventilation of the roof space remained ambiguous until Professor Frank Rowley conducted a series of “dog house” experiments in 1939. Rowley, a professor at the University of Minnesota and the president of ASHVE (currently known as ASHRAE), conducted roof ventilation research utilizing specimens in the form of small scale houses that closely resembled the size and shape of dog houses. The test specimens were constructed with sloped roofs and were similarly prepared and constructed without vapour barriers. The only difference between the specimens was the amount of ventilation allowed into the attic space. The first specimen had no roof ventilation while the other two specimens were constructed with vent ratios of 1/288 and 1/576, respectively. These test specimens were then subjected to interior and exterior conditions similar to residential dwellings under typical winter conditions.
These vent ratios represent the required area of openings providing exterior air into the roof cavity per horizontal roof area. At the conclusion of the test, only the house with a vent ratio of 1/288 revealed no traces of condensation or frost formation.
Rowley, Axel B. Algren, and Clarence E. Lund later completed full-scale tests yielding similar results to the doghouse experiments (Rowley, 1941). As part of the series of full-scale tests, a test specimen was also evaluated with a “flat” roof configuration (hereafter, flat roof). The test conditions were an exterior temperature of -23 C (-10 F), and interior air at 21 C (70 F) and 40 per cent relative humidity (RH). In general, various-sized ventilation openings and types were evaluated for the roof cavity under constant test conditions and building configuration. According to their findings, “light” frost accumulations were typically noted within the roof cavity spaces, regardless of whether roof ventilation was provided by side wall or roof openings.
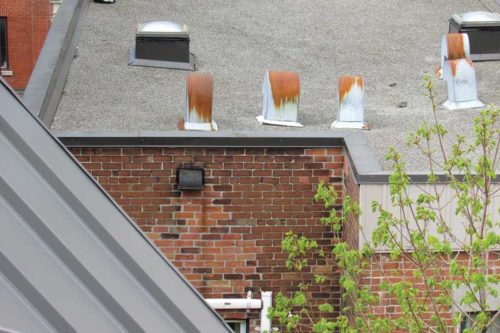
In 1942, the Federal Housing Authority (FHA), in the U.S., published the Property Standards and Minimum Construction Requirements for Dwellings, which stated ventilation be provided for all roof cavities and the minimum net ventilation area be “1/300 of horizontally projected roof area” for sloped roofs. Rowley’s findings were often assumed to be the source, or at least the basis, for the currently practiced 1/300 vent ratio. However, the FHA provided no references or citations in their publication.2
Five years later, the Housing and Home Financing Agency (HHFA), which oversaw the FHA, conducted research to verify the 1/300 requirement. Under the supervision of Ralph Britton (HHFA principal investigator), Penn State University conducted the tests, utilizing six insulated flat-roof structures. In general, a vent ratio of 1/300 was used for four of the specimens, with the other two having either no ventilation or a vent ratio of 1/100. It should be noted that the structure with a vent ratio of 1/100 in addition to a structure with a 1/300 vent ratio were studied without the installation of a vapour barrier. The results of the experiment indicated that structures with a vapour barrier installed, and a vent ratio of 1/300 revealed no visual or imminent condensation. In addition, structures with no installed vapour barriers, whether with a 1/300 or 1/100 vent ratio, and structures with no ventilation—all revealed imminent or some frost formations. Despite some overall encouraging initial findings, subsequent research was halted due to a lack of funding and the 1/300 requirement was adopted by ensuing building codes for sloped roofs.3
Evolving standards: The path of roof ventilation in the building code
Despite the limited experiments conducted by Rowley and the lack of proper referencing by the FHA in their 1942 publication of Property Standards and Minimum Construction Requirements for Dwellings, the 1/300 for sloped and 1/150 for flat ventilation requirements for attic spaces remains a somewhat arbitrary requirement in current North American building codes. Although this value was subsequently verified through some additional limited testing for flat-roof structures by the HHFA, it was adopted by North American building codes. These results, however, remain statistically insignificant to designers and builders.
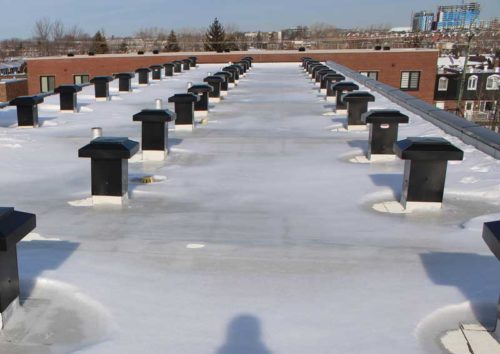
In Canada, the requirement for the 1/300 vent ratio first appeared in the 1953 National Building Code (NBC) and it did not make any distinction between structures with flat and sloped roofs. A 1959 revision of the code stated: “All unheated attic spaces shall be vented to the outside air. The total unobstructed area of vents shall be not less than 1/300 of the insulated ceiling area. Each vent shall be at least 60 square inches in net cross-sectional area and vents shall be spaced to provide the optimum circulation and change of air.“4 A distinction in required vent ratios between flat and sloped roof structures was later introduced in the 1977 NBC, stating in Article 9.19.1.3: “Where insulation is placed below the roof sheathing, and the roof slope is less than 2 in 12 or the roof incorporates no attic space, the unobstructed vent area shall be not less than 1/150 of the insulated ceiling area, uniformly distributed on all sides of the building”. Only minor changes to these articles in the code have occurred over time.5
Per the latest version, NBC 2020, the 1/150 vent ratio for flat roof structures persists. Article 9.19.1.2-2
states: “Where the roof slope is less than 1 in 6 or in roofs that are constructed with roof joists, the unobstructed vent area shall not be less than 1/150 of the insulated ceiling area.” NBC 2020 also adds the vent openings are not to be concentrated to only the top or to the bottom of the roof spaces (Article 9.19.1.2-3): “Required vent types may be roof type, eave type, gable-end type or any combination thereof, and shall be distributed a) uniformly on opposite sides of the building, b) with not less than 25% of the required openings located at the top of the space, and c) with not less than 25% of the required openings located at the bottom of the space.”6
Although it is placed as such that it may serve as a general statement regarding both sloped and flat roof structures, the last statement (c) is rarely seen practiced for flat roofs.
Flat roofs: A Montreal staple
The Industrial Revolution in the late 19th and early 20th centuries resulted in a significant increase in population for the island of Montreal; soaring from approximately 90,000 inhabitants in 1861 to roughly 724,000 over a span of 60 years. The growth of the city was prompted by the construction of the Lachine Canal and the expansion of the Port of Montreal. Not only did these projects necessitate a large workforce and the need for nearby housing, but inhabitants chose to form “villages” in these popular areas. Residential construction in the rapid developing riverside boroughs of Ville LaSalle, Lachine, Pointe St. Charles, and Griffintown, in addition to more inland boroughs such as Notre-Dame-de-Grace, St-Henri, and Plateau Mont-Royal produced residential dwellings constructed in close proximity to each other. With high demand for housing and narrowly-spaced lots, many new dwellings were often constructed attached to each other in these communities. With little to no space between individual properties, a flat roof design proved advantageous over a sloped roof.7 Flat roof designs also provided a more economical roof construction compared to sloped roofs. Consequently, dwellings with a flat roof design became a popular type of construction.8
As the city expanded, the construction of flat roof structures remained popular. Dwellings constructed with a flat roof continued to provide effective use of the available land. Aerial perspectives of the city today easily reveal the extent of residential low-rise buildings in Montreal constructed with flat roofs. These buildings were typically of wood frame construction and comprised a roof cavity between the roof deck and upper-storey ceiling finishes. The older structures were rarely subject to condensation issues, mainly because these structures were minimally insulated and were not airtight. Energy during this period of construction was relatively inexpensive and the need for insulation and airtightness was generally not required.9
However, with rising energy costs and added pressure from building codes and their requirements to design and build increasingly more energy efficient construction, the use of insulation (especially within roof attic spaces) and tighter construction evolved. New construction and existing structures subject to significant renovation were generally better insulated and were generally subject to less air leakage than older construction.
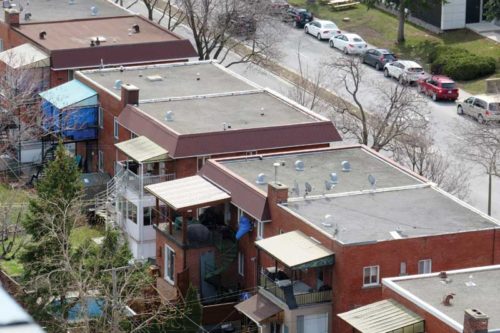
Ventilation strategies for flat roofs
Cavity ventilation is essential for insulated flat roof structures and can be achieved through passive or active means, or through a combination of both. In general, the roof structure of older residential buildings was constructed using roof joists, whereas modern roofs are constructed using parallel chord wood trusses. The installation of these trusses provides an economical construction and allows for deeper roof cavities and consequently deeper layers of insulation. The open webs of the trusses also provide a possibility for cross-ventilation of the roof cavity, given that sufficient distance remains between the top of the insulation and the bottom of the truss’ upper chord.10 It has been typically stated, including in the NBC, that a minimum 76.2-mm (3-in.) distance remain between the top of the insulation and the underside of the roof deck.
With the introduction of the 1/150 vent ratio, NBC 1977 also introduced the idea of installing 38- x 38-mm (2- x 2-in. nominal) purlins in the perpendicular direction of the roof joists to promote cross-ventilation and the dissipation of humid air to the exterior. Sufficient cross-ventilation within the roof cavity is important in order to minimize the risk of condensation regardless of the employed ventilation strategies.5
In general, the means for passive ventilation of flat roofs are limited to soffit vents and longitudinal vents. Soffit vents are typically located at the eaves and introduce fresh air into the roof cavity from its bottom extremity. Soffit vents are scarcely designed, and consequently their installation never introduced, into new low-rise construction projects. Architects are opting for designs without projections near roof level that expose the exterior cladding until the top of the parapet wall. Longitudinal vents are relatively recent and are continuous vents situated within the roof basin and raised from the roof deck to exhaust the air within the cavity. Despite the limited height of the roof assembly, longitudinal vents could maximize stack action when used in combination with soffit vents. However, it appears that longitudinal vents are never used since active ventilation provides a more cost-effective solution.
Active ventilation is often achieved through the installation of goosenecks and roof ventilators. In addition, roof ventilators are available in single- and multi-blade formats for which multi-blade units draw more air from the roof cavity.
Roof ventilators are almost exclusively used as the selected ventilation strategy of modern-day flat roofs for low-rise construction. These devices effectively draw air from the roof cavity, however with insufficient fresh air intake, humid air from the interior spaces can be aspirated into the roof cavity and may aggravate the formation of frost, condensation, and subsequently mould growth. Over-depressurization of the roof cavity, relative to the occupied space, may also create a significant pressure differential that the humid interior air finds a way into the roof cavity, leading to similar results.11
As seen in the photographs throughout this article, many buildings on the island of Montreal are attached on either one or two sides to another property. In addition, the adjacent properties often use different ventilation strategies. Given these differences, it is important that party walls are well constructed to isolate the individual roof cavities. Although the construction of party walls was original a city ordinance to limit the spread of fire in the 18th century, the isolation of roof cavities also becomes important so the ventilation of one roof does not impact the other.7 Such a case is presented in the first case study presented in the next section.
Case studies
Recently, condensation problems and issues of mould growth within roof cavity spaces have become more prominent in new or newly renovated buildings. Unfortunately, many designers and builders place great faith in the building code with regards to flat roof ventilation requirements without due consideration to basic ventilation fundamentals. In addition, given the limited research that current roof ventilation requirements are actually based on, it is no surprise that problematic situations arise. Outlined are some projects issues of condensation or mould within attic spaces that were addressed.
Laverdure
In April 2017, the authors’ company was requested to investigate a recent accumulation of moisture within the roof cavity of two-storey residential townhouses in the Ahuntsic borough of Montreal. The buildings comprised of a series of attached townhouses, which was subsequently the focus of additional investigations. The construction of the buildings was completed the year prior and damages to the second floor level finishes were reported in spring 2017. An initial investigation of the roof cavity via the removal of top-mounted roof ventilators revealed dampened roof insulation, and darkened wood surfaces on the underside of the roof deck and on the framing members.
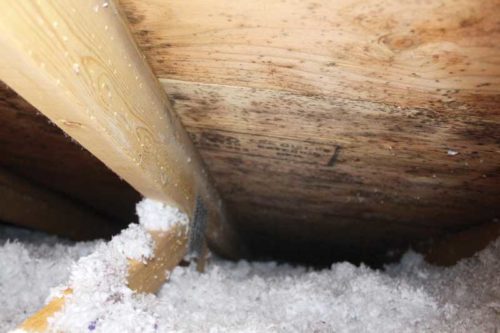
In general, a shared roof cavity for the six properties contained a total of 12 top-mounted roof ventilators (six-blade) located at quarter-points from the end walls of each property. In addition, no side inlet ports or other means of introducing fresh air into the roof cavity were noted. Exhaust ducts for mechanical ventilation systems (e.g. bathroom fans, hoods, etc.) were evacuated through the masonry walls.
In May 2017, smoke tracer investigations were undertaken at the second floor level of one of the townhouses with the goal of identifying potential moisture sources into the roof cavity. These investigations revealed minor deficiencies at the junctions of the fan casings with ducting and the vapour barriers within the master bathroom. However, the major sources of moisture migration into the roof cavity originated from a lack of sealed ducts for the return air handling.
The lack of sealed ducts for the return air handling allowed humid air to enter the wall cavities and bypass the vapour barrier at the head of wall partitions. In addition, the result of utilizing only top-mounted roof ventilators for the cavity ventilation creates negative pressurization within the roof cavity under normal conditions, which consequently draws humid air from the interior space.
Based on these observations and analysis, certain repairs were recommended. In addition to localized repairs at the master bathroom fan, the installation of sealed ducts for the return air handling was recommended to limit the humid air from bypassing the vapour barrier. Side inlet ports below parapet level were recommended to introduce fresh air into the roof cavity and resolve depressurization.
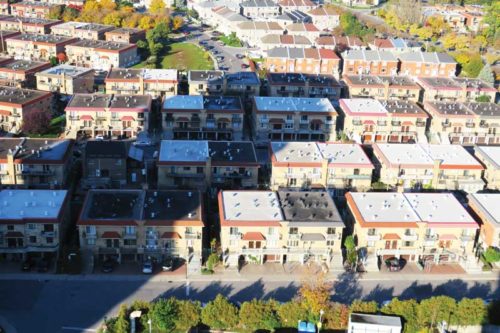
Prince-Arthur
In May 2017, the company investigated recent accumulation of moisture within the roof cavity of a three-storey condominium building near downtown Montreal. The building was originally constructed in the early 1900s but had been retrofitted in 2010. Similar to the Laverdure project, damages to the interior finishes were reported at the upper level (third floor) and an initial visit of the roof cavity also revealed a darkening of the underside of the roof deck and on the framing members.
During the initial visit, the capping of roof-mounted ducting enclosures was removed to gain access to the roof cavity and revealed an air space of only 76.2 mm (3 in.). In addition, the roof ventilation was limited to two single-blade roof-mounted ventilators.
During investigations, it was noted that a disconnected duct at one of the bathroom fan exhausts contributed largely to the moisture accumulation within the roof cavity. Once into the roof cavity, the moisture could not be evacuated effectively.
Therefore, the main, proposed solutions for this project were to conduct localized repairs at the deficient bathroom fan, introduce fresh air into the roof cavity via side inlet ports placed within the masonry, and to increase the cavity depth (raise the roof deck during replacement).
Belvedere
In August 2017, the recent moisture accumulation within the upper roof cavity of a newly remodelled residence in the Westmount borough of Montreal was investigated. During an initial site visit, high humidity levels were measured at the upper floor level (57 to 58 per cent RH), and darkened wood framing and deck underside were observed within the roof cavity. In addition, the ducts for bathroom fan exhausts were not equipped with backdraft dampers and were improperly terminated. During subsequent investigations, it also appeared the top-floor mechanical system was over-sized and cycled excessively, not allowing sufficient time for the dehumidification of the interior air during cooling.
The characteristics of the roof were such that the thickness of the air space varied between 178 mm
(7 in.) and 254 mm (10 in.), and the roof ventilation was limited to four, well-distributed, single-blade roof ventilators. As part of the recommendations, side inlet ports were incorporated within the masonry wall to introduce fresh air into the roof cavity and avoid depressurization during normal operating conditions.
In addition, many modifications were recommended regarding the mechanical systems and included the modification of the HVAC system (reduce cycling and minimize internal pressurization) and repairs to the bathroom exhaust fan ducts. In addition, repairs to the discontinuous vapour barrier installations were made.
The company was not involved in any further follow-up investigations, however recent repairs were undertaken at two of the case study sites.
The need for further research
With the goal of developing clear guidelines for effective roof ventilation, the authors’ company is gathering other construction and engineering professionals, and university researchers to further investigate ventilation requirements for flat roofs. The intent is to undertake full scale tests to determine adequate ventilation strategies for flat roof wood construction.
An exterior test structure will be built in Montreal and has been to emulate the existing housing stock in the city, with the goal of studying the impacts of various ventilation strategies and conditions. The 9.7 x 7.3 m (32 x 24 ft) structure is designed to limit the waste of construction materials and to facilitate the evaluation of various roof ventilation schemes. In addition, the impact of various roof cavity (i.e. depth and placement of insulation) and parapet configurations will also be evaluated.
An initial phase of monitoring and data collection within the roof cavity is anticipated for winter 2025. An understanding of the various ventilation factors and their effects on the roof cavity behaviour will be obtained during this phase. If winter conditions permit, basic ventilation configurations will also be analyzed. Additional configurations will be analyzed in depth during the following winters.
The company has identified that problems exist with the ventilation of flat roofs and that research is required to establish effective ventilation strategies. The goal of this research is to provide practical information that can be implemented within the housing industry.
Notes
1 Refer to Rose, William B. “Early History of Attic Ventilation.” Building Research Council-School of Architecture. University of Illinois at Urbana-Champaign, 2002, pages 3-5.
2 See note 1, pages 7-9.
3 See note 1, pages 10-11.
4 Learn more about the National Building Code of Canada 1953. NRC No. 3474. Ottawa, Canada: National Research Council, 1953, page 72.
5 See the National Building Code of Canada 1977. NRCC No. 15555. Ottawa, Canada: National Research Council of Canada, 1977, page 270.
6 National Building Code of Canada 2020 Volume 2. First Printing. Ottawa, Canada: National Research Council of Canada, 2020, pages 109-110.
7 See the research by Maryse Leduc and Denys Marchand. Les Maisons de Montréal. Montreal: Gouvernement du Québec – Ministère des affaires culturelles, 1992, pages 12-17.
8 Read the document by Michèle Benoit & Roger Gratton. Pignon sur rue – Les quartiers de Montréal. Montreal: Guérin Éditeur, 1991, pages 21.
9 Refer to the study by Forgues, Y.E. “The Ventilation of Insulated Roofs.” National Research Council Canada. Ottawa, Canada. 1985, page 2.
10 See note 9, pages 6-7.
11 See note 9, pages 7-11.
Test your knowledge! Take our quiz on this article.
Domenico D’Amato, Eng., is a project engineer with nearly nine years of experience in building envelope consulting. D’Amato has performed and assisted in multiple facade safety inspections, condition surveys, and investigations of building envelope failures.
Antonio Renzullo, Eng., has 22 years of experience in building envelope consulting. His specialization includes building envelope inspection, technical investigations, and analyses of building envelope deficiencies, and assembly failures. Additional experience includes data acquisition, instrumentation, research and development, and equipment procurement and development.
Domenic Chiovitti, Eng., is president of Chiovitti Consultants and specializes in building envelope consulting. Chiovitti has more than 35 years of hands-on experience and has been recognized by the court as an expert in numerous cases and investigations with regards to envelope performance failures.