Repair and maintenance solutions for parking garages
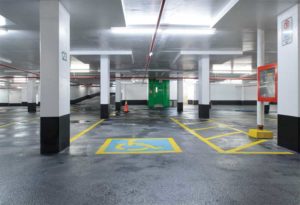
By Nigel Parker, P.Eng., LEED AP
Parking garages and other concrete structures are often exposed to severe corrosive environments leading to deterioration that necessitate the need for evaluations, repairs, and rehabilitation. Owners, engineers, architects, and contractors involved in the operation, maintenance, and restoration of parking garages play a key role in ensuring the structures are maintained in a state of good repair. Failure to do so lead to increased repair costs, potential loss of revenue due to closure of the facility, and, in the absolute worst case, structural failure resulting in a loss of life.
With many different concrete structural framing system types, repair methods, and maintenance solutions, knowing how to recognize a problem and evaluate it; design and implement a repair strategy, and finally how to maintain the structure becomes increasingly difficult.
Structural framing systems
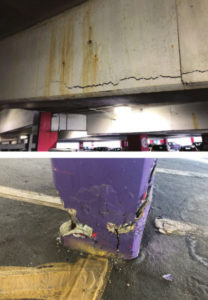
To understand how to repair and maintain concrete structures, an understanding of the types of concrete structures is required. In the Canadian market, there are three main types: cast-in-place, precast, and post-tensioned concrete.
Cast-in-place concrete structures consist of reinforcing steel and plastic concrete constructed onsite. Within the cast-in-place normally reinforced umbrella, several framing systems exist, including two-way, one-way, pan-joist, and waffle.
Precast concrete consists of concrete elements, either un-reinforced, normally reinforced, pre- or post-tensioned, constructed at a fabrication plant and then shipped to site. One of the most common precast structure types is the single- or double-tee parking structure.
Finally, post-tensioned concrete structures consist of concrete that is cast with an unbonded or bonded/grouted tensioning cable that is tensioned after the concrete cures to provide compressive forces to the member.
In addition to these three types, there are also structures utilizing structural steel framing to support the concrete slab or act compositely with concrete. The type of structural framing system will inform decisions on available repair solutions.
Concrete deterioration 101
Regardless of the type of concrete structure the potential for deterioration exists. Corrosion and carbonation are the two main types of concrete deterioration. Corrosion is an electrochemical reaction where electrons migrate from the anodic to the cathodic zone, releasing ferrous ions at the anode and hydroxide ions at the cathode. This process eventually leads to a potential difference between the anodic and cathodic areas at the surface of the steel reinforcement, resulting in the creation of rust as a by-product. Since rust occupies a larger volume than steel, it exerts internal pressure that causes the surrounding concrete to crack, delaminate (i.e. separate from the steel), or spall (Figure 1). As the concrete deteriorates, the reinforced-steel becomes exposed, thereby allowing more chlorides to penetrate the concrete and speed up the process of corrosion. The corrosion process is accelerated in structures, such as parking garages, where chloride ions (i.e. de-icing salts) are used. Concrete structures with a chloride ion by weight of cement of 0.20 per cent are generally considered to be above the threshold for corrosion to occur.
Unlike corrosion, which is an electrochemical reaction, carbonation is a chemical reaction between carbon dioxide (CO2) in the environment in the presence of moisture with hydrated cement minerals, specifically calcium hydroxide, to produce calcium carbonate (CaCO3). Carbonation of concrete is associated with the corrosion of steel reinforcement and shrinkage. However, it also increases the compressive and tensile strength of concrete, so not all of its effects on the material are bad.