Repair and maintenance solutions for parking garages
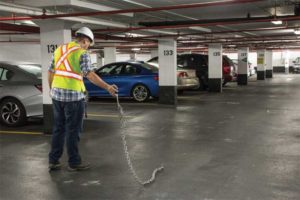
In addition to corrosion and carbonation, concrete can also deteriorate through freeze-thaw damage, alkali aggregate reaction (AAR), sulphate attack, fire damage, overloading, and, in the case of post-tensioned structures, post-tensioning strand failure.
Recognize and evaluate
A deep understanding of the type of concrete structure and also the deterioration mechanisms enables the engineer to undertake a comprehensive assessment of the structure to document the existing conditions and provide recommendations for repair. A comprehensive assessment of a concrete structure would include a detailed review of all available documents, past reports, and original drawings, in conjunction with a site visit. The site visit component would include both visual and acoustical surveys
(i.e. chain drag and hammer tap) to fully assess the extent of deteriorated concrete and/or moisture protection systems.
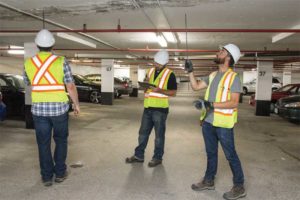
A chain drag survey is a technique used to locate hollow sounding areas on the suspended slab surface. However, it does not provide information with respect to the type of deterioration detected (Figure 2). The hollow sounding areas detected may be a result of concrete delaminations caused by the corrosion of the embedded reinforcing steel in the structural slab or due to the separation of the moisture protection system from the surface of the suspended slab. Similar to the chain drag technique acoustical sounding of the vertical concrete elements and suspend slab soffit is undertaken to identify the extent of concrete delamination (Figure 3). The principle behind the use of tapping rods/hammers to detect delaminations is similar to that of the chain drag for detecting slab surface delaminations. A tapping rod, when struck against the slab soffit, or a hammer struck against a wall or column, gives off a high-pitched ringing sound if the concrete is not delaminated whereas a hollow sound is heard when delaminated concrete is struck.
In addition to site assessment, material and destructive testing can be undertaken to determine the in-situ properties of the concrete (strength, density, air voids, Petrographic Number [PN], etc.), the chloride ion content, rapid chloride permeability (RCP), carbonation, half-cell potential, and as-built conditions. As the assessment is tailored to each structure, an engineer specializing in the repair and protection of concrete structures will be able to provide recommendations on what material testing, if any, is needed for a given project. For example, a strand assessment is necessary for post-tensioned structures to understand the condition of the embedded post-tensioning system. This may require test openings to expose the strands.
Design and implement
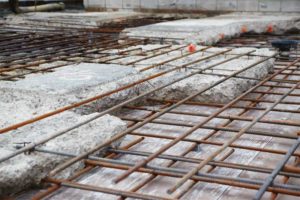
The results of a detailed assessment of the concrete structure will inform the type, extent, and scope of available repair strategies. Protecting the structure and maintaining the waterproofing systems in a state of good repair allow for the uninterrupted safe use of the facility, and ensures stability in the value of the asset and reduced long-term capital expenditure costs.
Strategies for repairs range from a do-nothing approach to complete replacement or demolition of the structure. The most common repair strategies have one thing in common: deteriorated material is removed and replaced with new, good quality concrete (Figure 4). As noted above, the full extent of any repair or rehabilitation program will be informed by a detailed condition survey assessment and the structural framing system for the structure in question. Included in the decision matrix on any repair program is the cost of the repairs and the anticipated service life of the structure and repairs themselves. An owner that intends to demolish a building within two years is not inclined to spend significant capital on long-term repairs, but may be more interested in installing temporary structural shoring to support the structure until the demolition is undertaken. Conversely, a wholesale rehabilitation approach, although more costly than localized repairs, may be more desired by an owner with an asset that is anticipated to be in use for the long term. In any restoration program, the corrosion process is typically reduced but not stopped, as the contamination within the concrete will remain in the unrepaired areas. Therefore, budgeting for periodic concrete repair and maintenance of the waterproofing system is required for the life of the asset.
To understand the required repairs, one needs to understand the structure type, extent of deterioration, available repair solutions, and the owner’s needs. Although most often used for civil projects, an asset depreciation curve is an exceptional model for concrete structures. Similar to roadways, investing capital in repairs and protection at the early signs of deterioration has a lower cost than repairing the structure when the asset is in poor condition. Investing $1 in localized repairs when the asset is in a fair condition eliminates the need to spend $4 to $15 on rehabilitation or reconstruction (Figure 5). Undertaking a $1 per square metre repair, protection, and maintenance program to a structure in the good to fair condition eliminates the need for a future $4 per square metre rehabilitation program when the structure is in poor condition, or when the structure is in very poor condition, a $15 or more per square metre structure replacement cost.