Rejuvenating old masonry facades with overcladding
The approach offers the opportunity to incorporate new esthetic materials, additional insulation, and even air barriers and moisture control layers often required by authorities having jurisdiction (AHJs) or owner/client groups. In some cities such as Toronto and New York, new green codes are incentivizing the use of overcladding to improve building energy performance without penalizing the owners for exceeding limits on added floor area ratios (FARs).
Two effective and common approaches to overcladding are exterior insulation and finish system (EIFS) applications and the hanging of insulated metal panels (IMPs) on a new outer subframe or furring. EIFS, a relatively new system type introduced in the North American market in the early 1970s, provides an adaptable opportunity for overcladding, insulating, and waterproofing on older or poorly designed masonry facades—regardless of texture, joint design, and fenestration. Successful applications hinge largely on having a sound masonry wall beneath. Benefits of the EIFS overclad include the elimination of water penetration as well as improvements to wall R-value.
As for IMPs, there is a growing field of examples showing effective overcladding with metal panel products. The Metal Construction Association (MCA) has contended that varied overcladding approaches—from insulated rainscreens to backup walls to metal profiles and other panel assemblies—work well over varied substrates as well as steel or concrete structures. They also provide an effective barrier, delivering continuous insulation (ci) across overclad areas. Retrofit wall applications commonly use metal panels or IMPs hung on an existing exterior surface such as concrete masonry units (CMUs) or brick veneer.
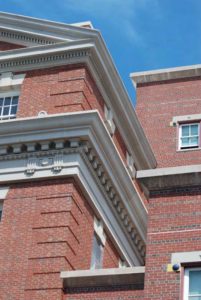
In this way, overcladding shares characteristics with rainscreen systems, and overclad enclosures can be considered as rainscreens in design and construction evaluation. It allows building exteriors to be updated even in load-bearing segments of concrete and masonry walls without having to undertake expensive structure reinforcement and additional columns, beams, or an underpinning foundation.
According to the National Research Council Canada (NRC), the original rainscreen principle consists of “a cladding, made of a lightweight, low water-permeance and low water-capacity material, installed on the exterior of a solid load-bearing brick wall, with a drained and vented air space between the cladding and the load-bearing wall.”1 This concept evolved to include the “open rainscreen wall” that addresses all forces which could lead to rainwater penetration.
The NRCC Division of Building Research also notes rainscreen overcladding often works effectively as part of building rehabilitation projects. In these solutions, the rainscreen walls are supported from framing members with a second inner barrier wall assembly that carries wind load and provides for requisite air permeability.
Early experience with overcladding in cities such as Toronto has proved to be highly effective. Kevin Day, a project principal with Sense Engineering, says this success led to “a movement to facilitate the renewal of high-rise residential buildings” in Canada and elsewhere. Whether the architect uses insulated composite exterior metal panels or another rainscreen-type overcladding, the solution “can improve not only the performance of the building, but also the comfort of the occupants.”