Reducing energy consumption with exterior sheathing
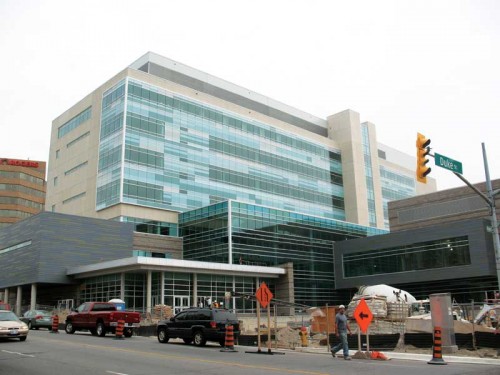
By Rockford Boyer, B. Arch. Sc.
With the ever-increasing demand for efficiency in new buildings, as well as the retrofitting of existing facilities, exterior sheathing plays an integral role in reducing energy consumption and the associated carbon dioxide (CO2) emissions. (This article deals with insulating, not structural, sheathing). Exterior insulation, continuous across all structural members without thermal bridges (other than fasteners and service openings), is the most thermally effective way to insulate a building. The sheathing’s thickness depends on the climate zone.
When selecting exterior insulation, there are four criteria to consider:
- sufficient and stable R-value at all temperature ranges;
- breathability;
- dimensional stability; and
- product durability and longevity.
As this article illustrates, finding a product meeting all this criteria can help the wall assembly reduce energy consumption. Key products to consider include stone or mineral wool, extruded polystyrene (XPS), and polyisocyanurate (polyiso).
Stable R-value
Insulation materials in North America are required to state their specific R-value when tested at 24 C (75 F), which is approximately room temperature. Traditionally, this value has been used for practical purposes, but it is important to look at how the insulating material performs at other temperatures.
For comparison between stone wool, XPS, and polyiso, room temperature is used as a baseline. Although there have been several studies conducted on sheathing performance and temperature, there is not much information published on insulation products and ‘climate-driven’ R-values.
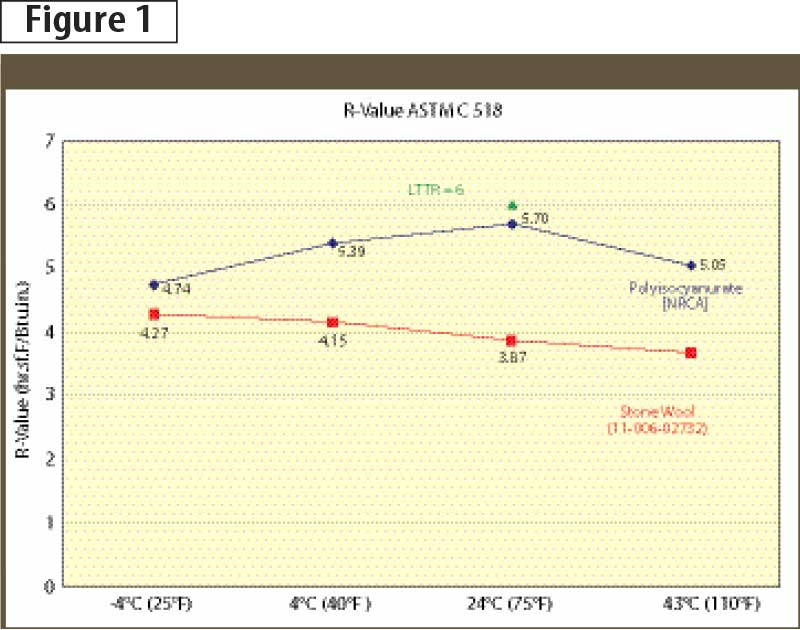
When comparing these three insulation types, only two of the products’ R-values increase when the temperature falls below 24 C. The principles of radiation and conduction at lower temperatures ensure stone wool and XPS R-values increase when the temperature dips. (Convection is the transfer of heat through various mediums [i.e. gases and liquids), whereas radiation is via electromagnetic waves. (A third method of heat transfer, conduction, occurs through materials molecules.]) These two materials’ rise depends on difference in temperature (i.e. Delta T) between the outside and inside. Stone wool or XPS sheathing would have a greater R-value in a typical Winnipeg winter climate in comparison to a typical Toronto winter.
On the other hand, the R-value of several polyiso insulations are reduced (in some cases, drastic ally) when the temperature decreases. This is because the blowing agents used in production of the foam insulation condense at lower temperatures. In the United States, the National Roofing Contractors Association (NRCA) conducted a study to better understand the performance of polyiso insulation at dynamic temperatures. Results for the third-party research are listed in Figure 1. The red line indicates stone wool’s R-value increases at the same reference temperatures. Manufacturer’s thermal warranties should specify the percentage of R-value loss over a specified period.
The chart illustrates the reduction in R-value due to increased or decreased temperatures for polyiso. The XPS R-values at dynamic temperatures were not immediately available, although the R-value will rise with lower temperatures.
Breathability
A wall’s ‘breathability’ is key to ensuring the assembly performs as intended. Using highly permeable materials in a wall will not impede its vapour drive potential. This is essential as it allows moisture to escape. A non-permeable material (e.g. several foam plastics and vapour retarders) can lead to durability issues, mould growth, and reduced R-values when moisture is trapped inside.
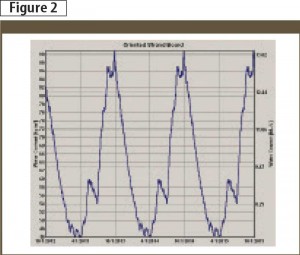
Letting the wall system ‘breathe’ either inward or out without restriction enables any moisture to filtrate outward, avoiding what could be called ‘compost in a bag.’ This concept is demonstrated through the various hydrothermal modelling charts that are depicted throughout this article. These charts used the following wall assembly:
- a 100-mm (4-in.) brick cladding;
- 25-mm (1-in.) air space;
- 50-mm (2-in.) thermal insulation;
- spun-bonded polyolefin membrane;
- 12.5-mm (0.5-in.) oriented strandboard (OSB) sheathing;
- 89-mm (3.5-in.) batt insulation;
- a vapour retarder; and
- 12.5-mm interior gypsum board.
The model’s location was an east-facing wall in Toronto that had a moisture sink of one per cent of water-driven rain allowed to bypass the insulated sheathing. It was run to simulate average temperatures for a three-year period.
Mineral wool thermally insulated sheathing placed over OSB sheathing
Figure 2 shows how moisture content (MC) in the OSB increases in the fall and winter, and can completely dry out during the spring and summer. There were no obvious issues with this wall assembly’s drying potential.