Reducing Canada’s carbon footprint with sustainable insulation
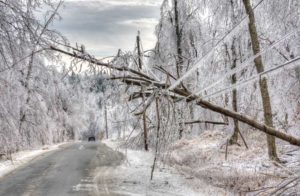
By Rockford Boyer, B. Arch. Sc., MBSc, BSS
At nearly 10,000,000 km2 (386,1022 mi2) and a maximum temperature ranging from +45 C (113 F) in Yellow Grass, Saskatchewan, to -63 C (-81.4 F) in Snag, Yukon, Canada is one of the largest and coldest countries in the world. However, even with the vast size of the country and the large delta in hot and cold temperatures, the global carbon impact is less than two per cent. In fact, in 2021, the Union of Concerned Scientists listed Canada as having only 1.8 per cent of the total global emissions.
As a point of reference, the U.S. and China account for almost 40 per cent of the total global emissions. It is still very important as Canadians to do their part to further lower the country’s total global emissions. Therefore, it is important to identify key sectors of energy use in Canada and discuss how the construction industry can potentially assist in reducing the impact of carbon generation and air quality through more sustainable building materials and practices.
The total energy demand for Canada was 12,204 PJ (2.92 kcal) with 52 per cent from the industrial sector, 23 per cent from the transportation sector, and 25 per cent from the building sector. The energy demand can be further broken down to 13 per cent residential and 12 per cent commercial. As a point of reference or scale of the yearly Canadian energy use, a petajoule is equivalent to 31.6 million m3 (1 billion cf) of natural gas or 278 million KWh.1 By breaking the petajoule unit down to a more common unit, it is obvious there is a massive amount of energy being consumed in Canada and throughout the world. For the design community, it is important to not only look at the energy/carbon that can be saved in buildings, but also how to reduce the building footprint through manufacturing, transferring, and disposing of building materials.
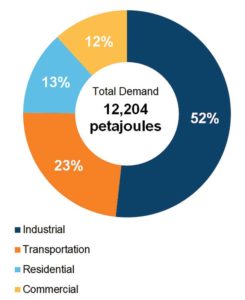
Considering the environmental impact of insulation materials
All building insulation types save energy throughout the use phase of buildings by minimizing the heat transfer (cold/hot) through the building enclosure. The insulation installed within the building enclosure must be used effectively to have the largest impact on energy reduction. The R-values listed on the data sheet, drum, bag, or from the salesperson are the nominal R-values and do not reflect the actual in-situ effective condition.
Sustainability impact analysis
Typically, calculations are conducted to determine the effective R values of these walls to ensure they meet the local building codes or intended energy use intensity. If all types of insulation produce the same effect R-value when calculated in an assembly, other metrics must be measured to determine the most suitable solution for the building’s carbon footprint. As previously stated, the combined energy demand in Canada for residential and commercial buildings is approximately 25 per cent; therefore, other metrics to assist in determining the most sustainable solution for reducing the overall carbon footprint should be determined by manufacturing and transportation of these insulation types.
Energy demand for manufacturing
Environmental product declarations (EPDs) and life cycle analysis (LCAs) are good tools to help understand the extraction, manufacturing, transportation, and disposal of building materials; however, they do not provide the full story. Building insulation is only a component in the building enclosure and different types of insulation all have different functions and characteristics. For example, fibrous insulation traditionally only functions as a thermal control layer and other components must be used in conjunction with the fibrous insulation to control the air, moisture, and possibly vapour. Spray foam insulation has performance characteristics that can achieve a thermal and air control layer, and possibly a vapour control layer without the need for a secondary material. Therefore, to better understand the total carbon footprint of the building enclosure, a full analysis of all components must be completed to fully grasp the overall sustainability impact.