Reducing Canada’s carbon footprint with sustainable insulation
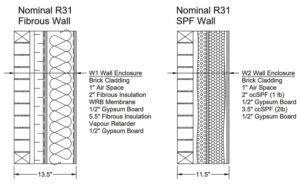
Transportation’s impact on energy consumption
Energy demand for the manufacturing of thermal insulation is listed in the industrial sector and has the largest total energy demand needs in Canada. At 52 per cent total energy demand, this sector represents the largest opportunity for a reduction in energy use. In relation to the manufacturing of thermal insulation, traditional insulation types such as fibreglass and mineral wool, require fuels such as natural gas and coke to melt the raw materials and spin them into fibres. High performance insulation types such as spray foam, extruded polystyrene (XPS) and expanded polystyrene (EPS) use more electricity to blend or mould their products into shape.
The influence of insulation thickness
In Canada, the benefit of using energy in the form of electricity is that more than 60 per cent of electricity is generated from hydro/tidal sources. Traditional and high-performance insulation types all typically have some percentage of recycled materials in their manufacturing process. The recycling process can include recycling onsite waste and waste directed from landfill created by another source. Mineral wool traditionally receives byproduct from other industrial (pre-consumer) processes, whereas fibreglass and foam insulations traditionally receive their byproduct from the consumer (post-consumer). Some manufacturers of spray foam divert plastic away from the landfill by using hundreds of millions of plastic bottles each year in their manufacturing process.
Canada is a large country. Driving from St. John’s, Newfoundland, to Vancouver, British Columbia, will take one approximately 75 hours with a travel distance of more than 6,700 km (4,164 miles). The increasing number of cars and trucks on the road has increased the vehicle running time due to traffic volume and has had a significant impact on the energy consumed by the transportation sector.
Proper disposal of thermal insulation
With transportation representing 23 per cent of the total energy demand for Canada, the construction industry should not only consider where construction materials are being manufactured, but also the material’s transportation efficiency. Insulation manufacturing facilities are expensive to build and maintain. With limited facilities spread throughout Canada, shipping from the manufacturing location and its shipping efficiency should be considered by the design industry.
Consider the following example, two insulation facilities are manufacturing products in Toronto and an 1,858 m2 (20,000 sf) university project is 2,030 km (1,261 miles) away in Winnipeg which needs to be insulated with R-20 exterior vapour permeable insulation. Shipping efficiency should be considered to minimize the number of trucks needed to provide the required amount of insulation to the construction site. Two suitable options are exterior-grade board stock insulation and site-applied open-cell exterior spray foam insulation. The site-applied spray foam insulation would only require one 16-m (53-ft) tractor trailer to completely insulate this project, whereas the offsite manufactured board stock insulation would require eight tractor trailers (depending on type).
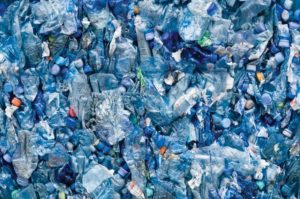
Expanding the perspective on thermal insulation
Thickness of the building enclosure has a direct impact on the total carbon footprint of the building, so ensuring an effective insulation solution will minimize the need for thicker footings, structural members, clips, flashings, jambs, sills, and other structures. Traditional insulation such as fibreglass and mineral wool uses trapped air between the fibres to achieve their R-values. Fibrous insulation typically has an average R-value of R-4 (RSI 0.7) per 25 mm (1 in.). High performing insulations use blowing agents (e.g. hydrofluoroolefin [HFO]) with a higher thermal performance than air to achieve their R-values.
Since 2021, Canada has mandated all blowing agents in thermal insulations must have a global warming potential (GWP) of one. The HFOs in XPS typically have an average R-value of R-5 (0.88) per 25 mm (1 in.), and the HFO’s in closed-cell spray polyurethane foam (SPF) have an average R-value of R-6 (RSI 1.05) per 25 mm (1 in.). It should be noted open-cell SPF does not use any blowing agents to achieve R-3.8 (RSI 0.67) value. EPS uses pentane trapped in closed cells; however, there is still trapped air between the closed cells and the material can still achieve an R-value of 4.7 when using graphite. All these insulations provide valuable resistance to heat transfer; however, they must be used effectively to achieve the best results in the field. Many types of SPF exist, including vapour permeable products used on the exterior.