Radon Active: Future-proofing buildings against silent hazards
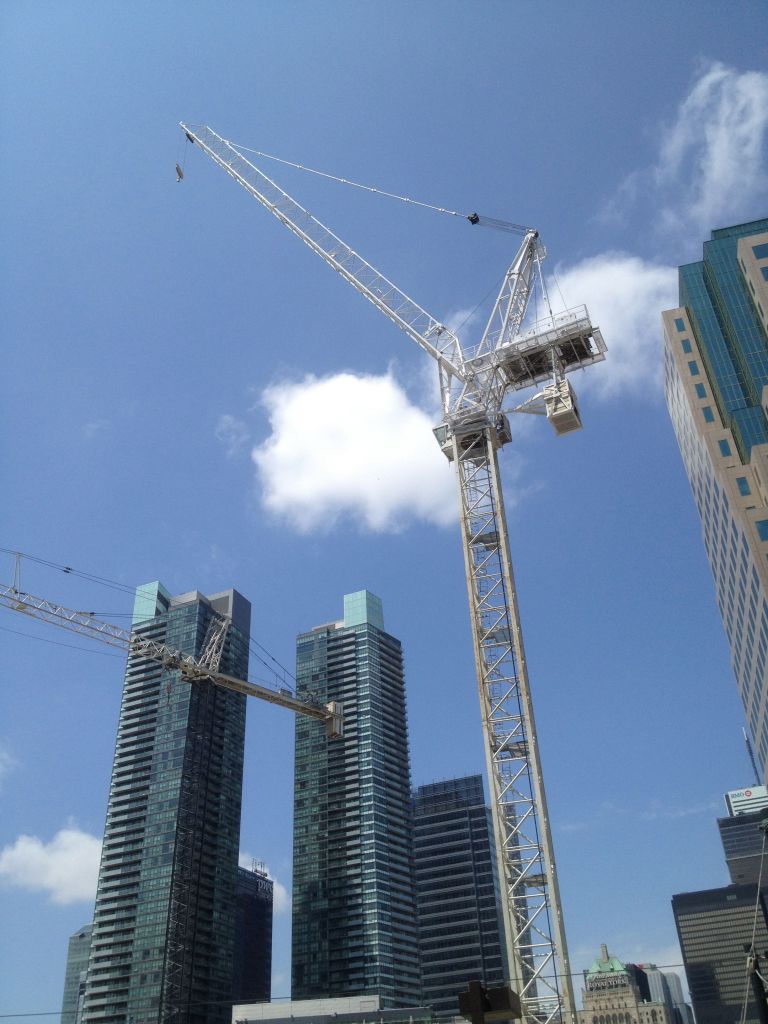
By Jason McGonigle, B.Tech., Dipl (Env. Tech), and Eric Hood, PhD, P.Eng.
Designing new buildings to meet both current and potential future hazards makes good business sense. This is particularly the case when pre-emptive protection measures have much lower costs in comparison to retrofits.
One example involves proactively dealing with infiltration of radon and other soil gases (e.g. methane) into indoor air. Radon is a radioactive gas emitted by the decay of naturally occurring uranium in soil. Driven by very small differences in air and pressure between a building and the surrounding subsurface, radon enters interior spaces through construction joints, service penetrations, and other small pathways through the floor and foundation.
Contrary to what was previously known, recent Health Canada data demonstrates that radon can be found in any soil type and that no region of Canada is ‘radon-free.’) Previously, radon risk was assumed to be tied to certain specific geological conditions, such as the presence of significant uranium in soil. Most experts erroneously believed radon to be a non-issue in Canada.
In recent years, there has been improved understanding of the health risks of radon. U.S. sources (including the Environmental Protection Agency [EPA] and the Surgeon General) have found it is the second-highest cause of lung cancer, after smoking. Health Canada has identified radon exposure as the leading cause of lung cancer among non-smoking Canadians.1 Accordingly, many industrialized nations, including Canada, have recently reduced the levels of radon allowed in indoor air. In 2007, the federal government adopted a guideline of 200 Bequerels per m3 (a measure of radioactivity), recommending remedial action to reduce the concentration to the extent practicable when exceeded in a building’s normal occupancy area.
Due to this increased understanding of the health hazards, the country’s federal and provincial governments are increasing emphasis on protecting building occupants from radon infiltration. Health Canada is assuming a lead role in taking steps to build public awareness of the risks of radon, and has released technical guidance documents, including Guide for Radon Measurements in Public Buildings (Schools, Hospitals, Care Facilities, Detention Centres) and Radon: A Guide for Canadian Homeowners.
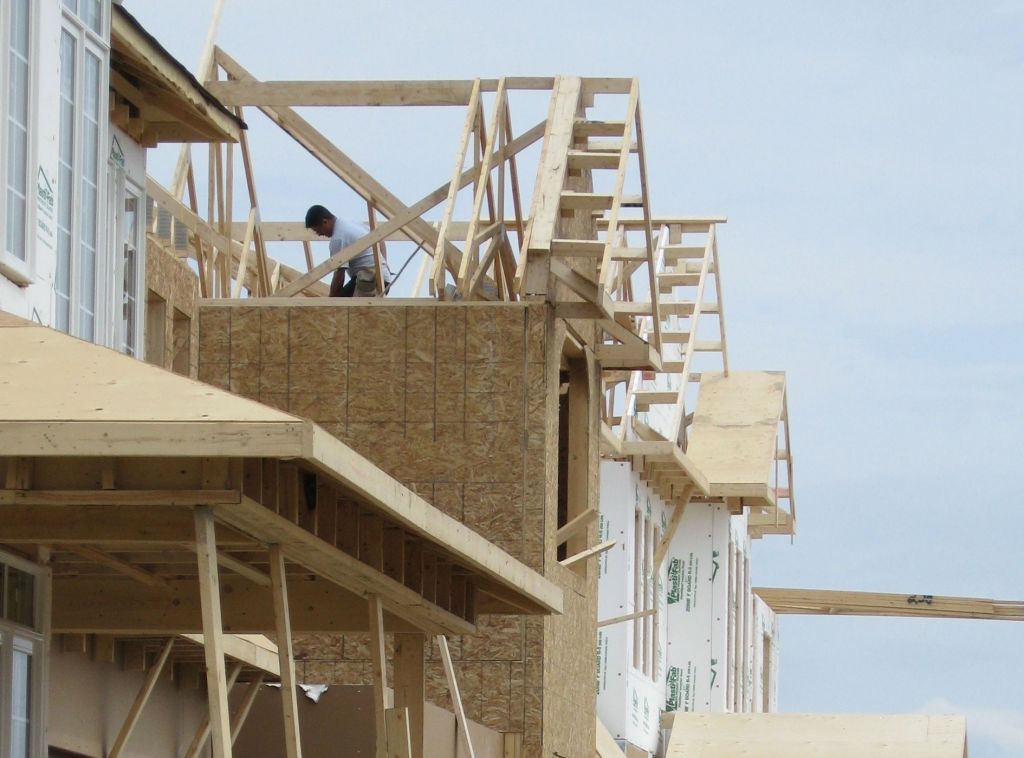
The provinces have been implementing Health Canada’s initiatives through a range of measures. For example, there was Ontario’s Bill 96 to make radon workplace testing mandatory (Radon Awareness and Prevention Act, 2013), which did not pass before the provincial election was called in the spring of 2014. However Bill 96 was a replacement for a similar, earlier bill that likewise got caught in an election before it could be passed; when this article was being written (late May 2014), the issue seemed to have the legislative staying power to come up again. Other provinces—including Québec, Nova Scotia, and Prince Edward Island—are conducting radon testing in schools. Following changes to the National Building Code of Canada (NBC) that require soil gas protection measures in residential dwellings, the provincial codes are adopting similar provisions.
Studies have found radon concentrations tend to be highest in enclosed rooms that are in contact with the ground, such as basements or the ground floor of buildings without a basement. However, HVAC systems and elevators can circulate radon-impacted air throughout the building, even to its highest floors.
It is now believed there are many variables contributing to radon levels, including ventilation, human activity (e.g. smoking), location in building, and foundation construction. There is good evidence that remediation is effective in significantly reducing radon levels. Proactive measures, such as those described in this article, could help improve the health of building occupants.
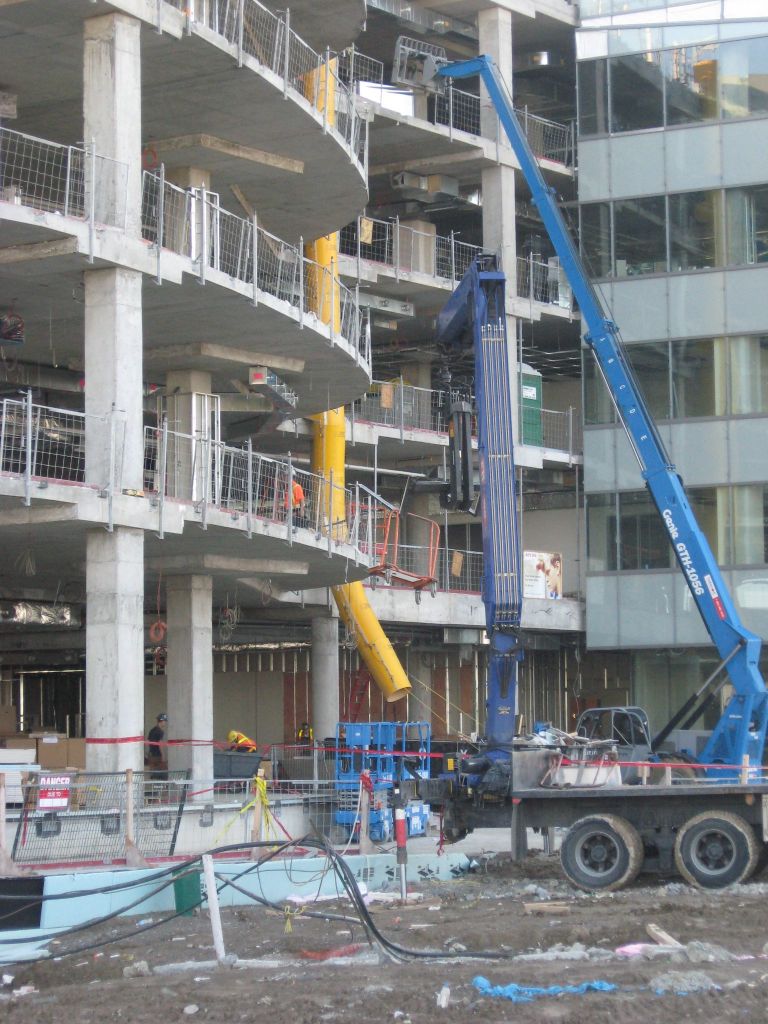
Testing for radon
Radon testing is simple and straightforward. A qualified measurement technician can install passive sampling detectors, about the size of a two-dollar coin, at strategic locations within the building. The sampling process takes time—Health Canada recommends periods of three to 12 months to provide reliable results.
Testing is typically done during the winter heating season, which can represent a ‘worst-case’ condition for radon. At the end of the testing period, the detectors are shipped to a laboratory for analysis. The findings of long-term studies are typically considered sufficiently reliable for the purpose of determining whether mitigation is necessary.
However, such long-term studies are often poorly suited to the realities of modern building management requirements. An alternative screening level study can be completed in as short as one day to provide real-time results and determine whether such a longer-term study is necessary to confirm the findings. Such studies typically involve the collection of radon samples from below the floor of the building and the measurement of radon concentrations using a field detector.
Mitigation without disruption
If the findings of a long-term radon testing program show problematic levels in a building, mitigation measures must be taken. There is a limited range of approaches.
Each approach has its own advantages and disadvantages, depending on the building design. Measures taken to deal with radon are similar to those that might be installed to mitigate other soil-borne hazards such as methane and volatile organic compounds (VOCs) associated with soil or groundwater contamination stemming from a property’s previous industrial use.
The most common means of mitigation is sub-slab depressurization, which usually involves connecting one or more suction points to the underlying soil through the concrete floor slab (depending on the size of the building and other factors) to exhaust radon into the atmosphere before it enters the building.
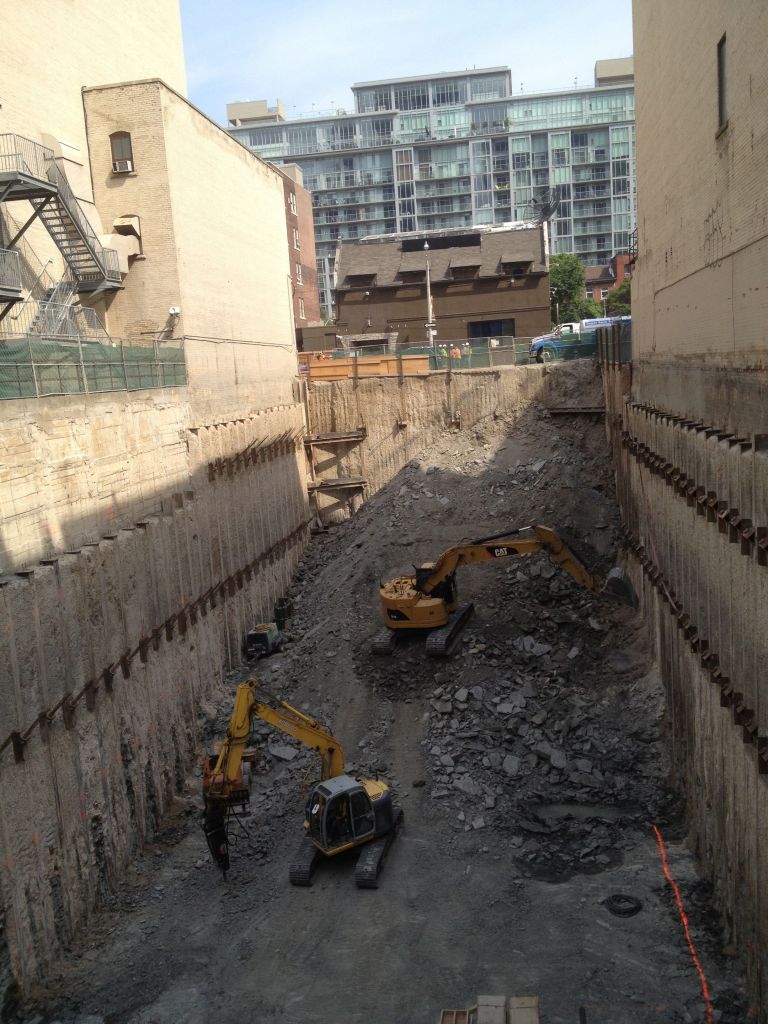
Additional piping is installed to carry soil gas containing radon from the suction pit to an exhaust point on the building’s roof. One or more electric fans, or in some cases wind-driven turbines, are installed to pull the soil gas from the underlying soil and vent it to atmosphere. The exhaust point must be set at a location where the exhaust gas will be harmlessly diluted in the atmosphere and will not re-enter the building through windows, doors, or other entry points.
For new buildings, a vapour barrier can be installed below the flow slab to prevent the flow of soil gas containing radon into the building. The vapour barrier must completely separate the building from contact with soil and be carefully constructed so it is free of any small punctures that can act as a pathway for radon migration, diminishing the system’s performance. For buildings being retrofitted with a mitigation system, installation of a vapour barrier is impractical; however, sealing construction joints and floor slab penetrations with flexible caulking is a simple and effective means for reducing radon entry and improving the performance of sub-slab depressurization systems.
Another common mitigation approach involves adjusting the building’s HVAC system to create a positive pressure in the building that prevents radon infiltration. Sufficient makeup air must be brought into the building to pressurize it over the range of building operation conditions, considering the effects on comfort heating and energy consumption. This strategy can vary in terms of reliability.
Radon-resistant building construction
The increase in public and regulatory concern about the hazards of radon, plus the understanding any soil type can potentially be a source of the radioactive gas, means it can make sense for new-building designs to proactively incorporate radon-resistant features as a matter of course. As with many building features, it is not only easier, but also less costly and disruptive, to build soil gas mitigation measures during construction than it is to retrofit these measures into an existing building. (The steps to be taken for construction-stage mitigation are virtually the same as those used in retrofitting an existing building—absent much of the cost and hassle associated with retrofits.)
New buildings can include a purpose-built venting layer below the floor slab, which allows radon to be easily removed. Typical venting layers consist of clear stone or other highly permeable materials. A recent innovation is the use of aerated floor-forming systems as a replacement for aggregate venting layers that allow the protection of very large buildings at minimal cost.
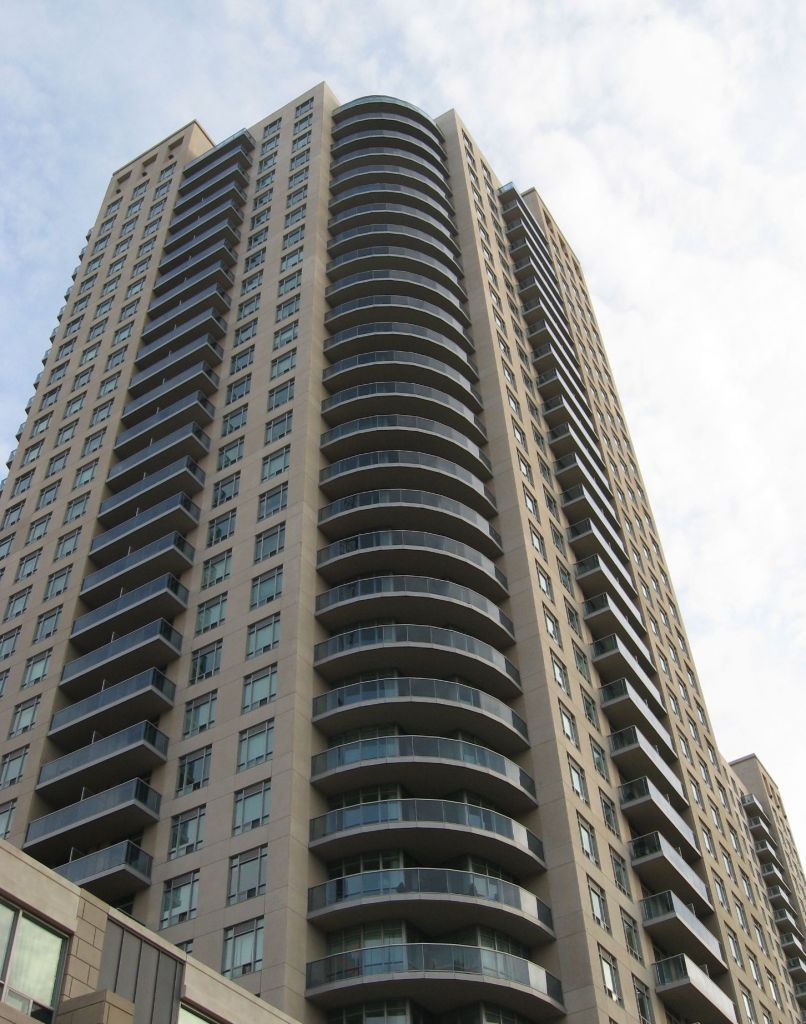
When the building is constructed with an effective mitigation system (with performance confirmed by a post-construction performance testing report), it becomes a selling feature for the building, potentially contributing to Indoor Environmental Quality (EQ) credits under the Canada Green Building Council (CaGBC) Leadership in Energy and Environmental Design (LEED) program. Future owners are reassured to know when radon is detected in the building after it is completed, it will be easy and low-cost to operate an effective mitigation system.
Conclusion
Dealing with radon requires having the correct professional expertise available. This may involve several skillsets, including an understanding of soil and groundwater contamination so as to provide information on the nature of the threat’s source, as well as knowledge over the factors impacting IAQ.
It is important to work with professionals who have not just the knowledge of their field, but the ability to understand the economics of building operation and the skill to communicate their findings to stakeholders. It is also critical to collaborate with professionals with experience working with the building design team, including the architect, structural engineer, and HVAC system designer. This enables integration of the mitigation system into building design, while also offering the experience necessary to ensure the mitigation system is properly constructed.
Notes
1 Some of these issues are identified in the Public Health Ontario document, “Lung Cancer Risks from Radon in Ontario: Burden of Illness, Estimates, and their Policy Implications.” Visit www.oahpp.ca. (back to top)
Jason McGonigle, B.Tech., Dipl (Env. Tech), is a principal in the Whitby, Ont., office of Golder Associates, where he is senior practice and business leader in the Environmental Health and Safety Group. He has 10 years of experience with Golder. McGonigle can be reached at jason_mcgonigle@golder.com.
Eric Hood, PhD, P.Eng., is a senior engineer and associate in Golder’s Whitby office. He holds a bachelor’s degree and a PhD in civil engineering, both from the University of Waterloo. Hood has five years of experience as a senior engineer with Golder; before that, he was a senior scientist with Geosyntec Consultants. He can be contacted via e-mail at ehood@golder.com.