Supporting sealants: Ensuring quality and consistency in insulated glazing unit seals
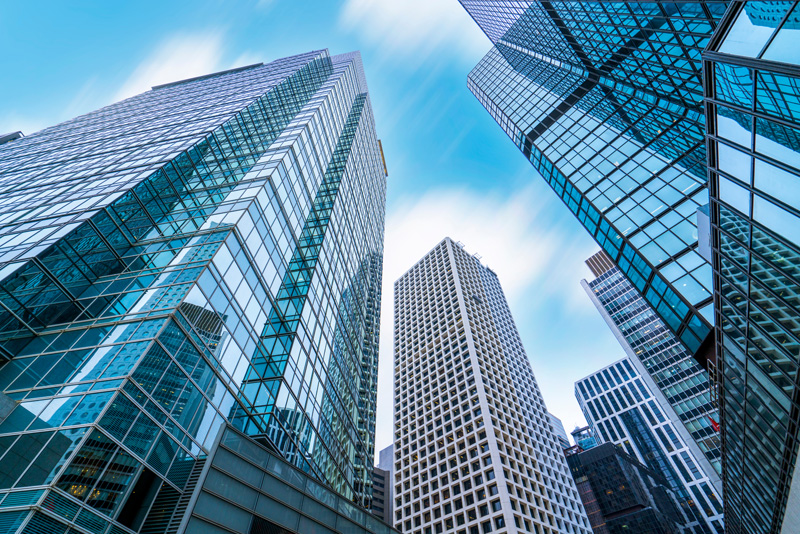
Sealants, the glue that keeps everything together, play a critical role in the performance and longevity of glazed fenestration systems.
The Fenestration and Glazing Industry Alliance (FGIA) is revamping IGMA TM-2400, Test Methods of Insulating Glass Sealants, to offer specifiers, manufacturers, and fabricators the most up-to-date information and best practices.
Together with several other FGIA documents, IGMA TM-2400 helps support quality assurance and product performance, mitigates risk, and ensures compatibility between sealants and glazing system components.
The role of sealants
A properly sealed insulating glass unit (IGU) ensures the vapour barrier and structural support are dialled in, allowing the IGU to deliver daylighting and thermal comfort in buildings.
On the other hand, seal failure can occur with poor or inadequate waterproofing, weeping, or vent holes in the glazing cavity. Failure can also happen because of faulty glazing techniques or selecting glazing materials that are incompatible with the insulating glass sealant system.
Considering the many different aspects of glazing systems—i.e. glass types, framing, gaskets, spacers, drainage, setting blocks, spacers, and shims—to design and install a high-performance facade, these components must be carefully specified, tested, and installed as a compatible and cohesive system. While each part of the system must be high-quality and suitable for installation, the sealant is key to a successful system.
Before discussing the details and testing methods of the new IGMA TM-2400 standard, the reader may wish to familiarize themselves with IGMA TM-3000, North American Glazing Guidelines for Sealed Insulating Glass Units
for Commercial & Residential Use, an informative resource on achieving the long-term performance of IGU systems.
In addition, IGMA TM-4000, Insulating Glass Manufacturing Quality Procedures, offers detailed guides and work instructions for the individual tasks necessary for assembling IGUs in a production setting.
The latter provides detailed guides and step-by-step instructions for IGU production in a factory setting. The former guide seeks to help standardize the manufacturing process to ensure quality and consistency.
The first section of IGMA TM-4000 is an overall checklist for unit fabrication, and the second offers detailed instructions for the different functions in the assembly process to support consistency.
By better understanding the inner mechanics of a glazing system and how everything works together, industry professionals will be better equipped to identify where failures can occur.
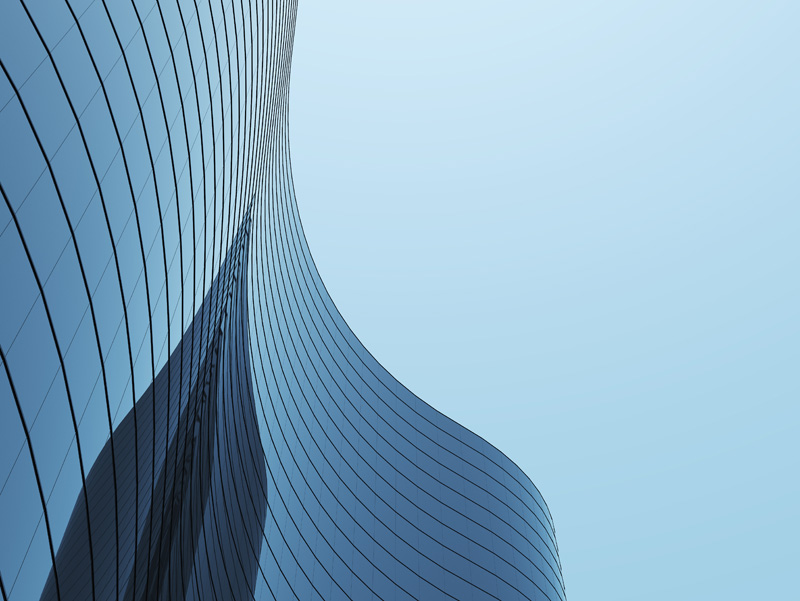
IGMA TM-3000
Unpacking some relevant information covered in IGMA TM-3000, the document contains advisory guidelines to assist in achieving the long-term performance of IGUs. It delves into different aspects of the glazing system and gives instructions for achieving adequate sealing and common pitfalls to avoid.
For example, to achieve a proper edge seal for dry-glazed systems, the minimum applied pressure is 0.70 N/mm (4 lb/in.) to create an adequate seal. At the same time, excessive or uneven pressure can increase mechanical stresses and contribute to glass breakage. Therefore, while edge-clamping pressure is usually sufficient to achieve an air
and watertight seal, pressure should not exceed 1.75 N/mm (10 lb/in.).
Another example is the importance of a framing system providing firm, four-sided perimeter support for an IGU. If this is improperly done, undue stresses are placed on the seals, which could lead to premature IGU seal failure.
IGMA TM-3000 also emphasizes the importance of ensuring proper drainage in the glazing channel because prolonged exposure to water or moisture vapour in the glazing channel is the number one cause of seal failure.
On the issue of compatibility, the document instructs that any materials that might come into contact with the components of the glazing system or IGU sealant(s) or be enclosed together under expected environmental conditions must be compatible with the sealant in all of those conditions.
Another issue to watch out for is sealants that contain linseed, mineral, vegetable oil, or certain excess plasticizers. When curing, these can release significant amounts of solvents or acids, thereby leading to IGU seal failure and surface contamination.
IGMA TM-3000 guidelines instruct that sealants used as heel beads or air and weather seals in contact with the IGU remain pliable under all expected temperatures, UV exposure, and environmental conditions to not interfere with the IGU’s movement capability. If this is impeded, it could lead to glass breakage or
seal failure.
Sealants must also be designed to withstand very hot temperatures, as IGUs with heat-absorbing or reflective glasses can heat up to as high as 60 C (140 F) when exposed to sunlight and still air and, in spandrel areas, as hot as
90 C (194 F). Also, the IGU assembly sealant must accommodate all structural frame and glass movements caused by wind, live and dead load deflection, and thermal expansion from those high temperatures.
Overall, it is highly recommended that one consult the glazing sealant manufacturer about their products’ performance, adhesion, movement capability, compatibility, and life expectancy.
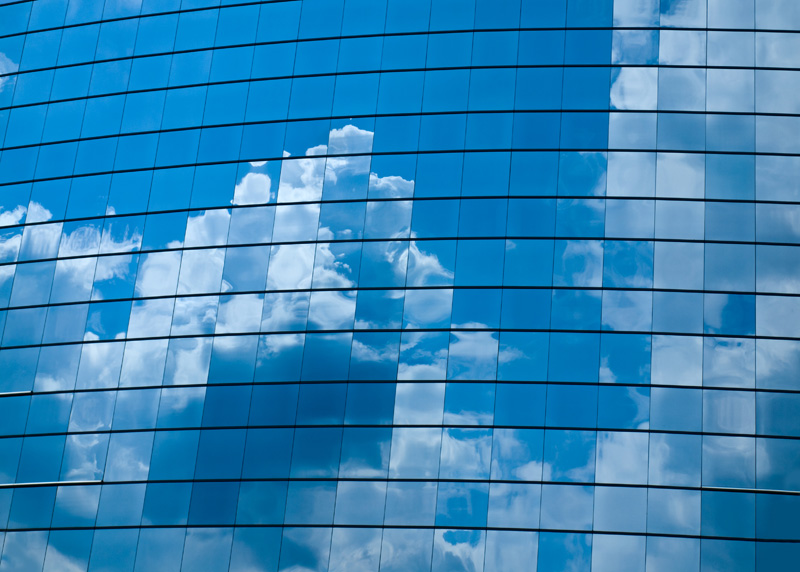
Latest version: IGMA TM-2400-24
This Test Methods for Insulating Glass Sealants was originally published back in 1976. It was reviewed in 1990, but no changes were made. While the vast majority of the information and test methods still apply, the document has been restructured and edited to incorporate the application of new technology.
The new version contains a revamped chart presenting the test methods with links in an easy-to-read manner. As a result, readers will be able to navigate the 69-page document more easily to find the most suitable test for analyzing the sealant in their application. This, in turn, lends greater quality assurance for the IGUs.
Delving into some more of the background in the newly revised IGMA TM-2400, FGIA points out the test methods were developed as advisory information and are meant to be guidelines. Consequently, they are intended to be voluntary, not requirements, as every application and installation differs.
FGIA test methods can be adapted into a plant’s quality control program, used to perform incoming materials checks, or employed to determine physical properties useful for engineering calculations supporting end-use. Essentially, the content is available as a tool for sealant manufacturers in their quality assurance programs and sealed insulating glass fabricators to assist in determining the quality of their incoming sealant. The information is also beneficial for specifiers and consultants to know what to look for when selecting products for their applications.
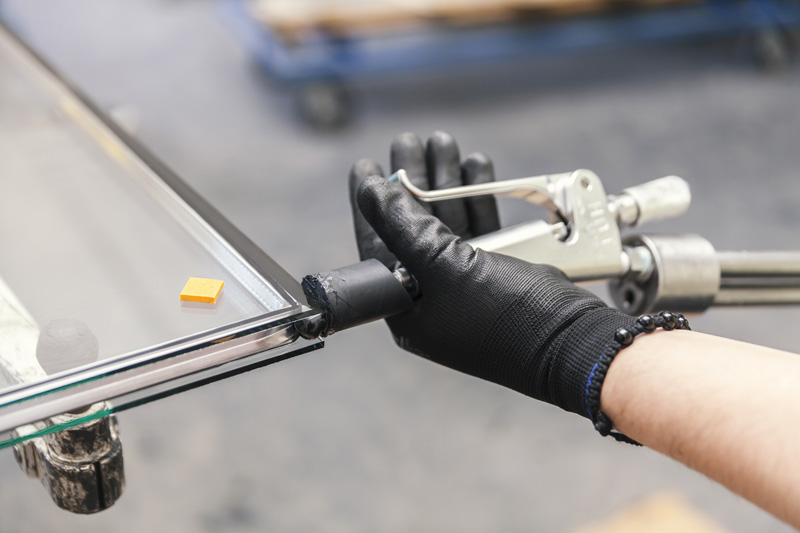
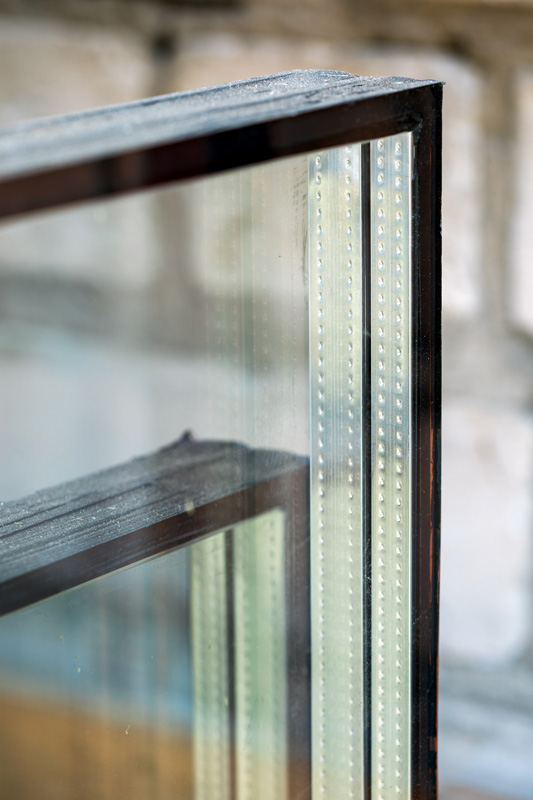
Key testing parameters
It is particularly important to call out a few key performance factors to test for, such as tack-free time, the sealant mix ratio and quality, moisture vapour transmission and permeability, shear testing, and sealant adhesion.
For the majority of these methods, the testing materials and apparatus must be equilibrated at 23 ± 1 C (73 ± 2 F) before starting the test.
Tack-free time is very important as the sealant must be fully bonded before the glass is moved.
Defined as the time interval after the sealant is mixed at standard conditions and without direct sunlight, it is determined to be fully cured when a polyethylene strip is pulled away from a sealant specimen and no sealant adheres to it.
The test method uses a 30 g (1.2 oz) brass weight, polyethylene strips, polytetrafluoroethylene (PTFE) moulds, a metal or PTFE straight edge, and a balance sensitive to 0.1 g (0.005 oz) to test tack-free time. The exact measurements are in the document.
To begin, 300 g (10.6 oz) of sealant base is thoroughly mixed with the appropriate curing agent for two or three minutes. Then, the mould is filled and struck off flat with a straight edge and cured for the specified tack-free time. Next, a polyethylene film with a brass weight is placed on the top surface for about 20 seconds. The film is peeled at right angles to the compound. If no sealant adheres to the strips, the unit passes the test.
IGMA TM-2400 delineates a couple of ways to check the sealant mix ratio, defined as the ratio part A holds to part B after mixing based on their proportionate weights.
The gravity cup method is a primary method performed with a specific gravity cup, a bottle used to determine the weight per litre (or gallon) and the specific gravity of paints or other liquids. The test weighs the Part A base material and the Part B accelerator material. Then, the actual mixed sample weight is compared to the theoretical mixed weight.
It should be noted the method requires a very high degree of accuracy when the two components have nearly the same specific gravity.
Another approach is the machine mix ratio check, a secondary test method that determines the base compound’s ratio to the curing agent created by a meter/mix machine.
To evaluate the uniformity of the mix, a small amount of mixed sealant is extruded onto a glass plate, and then a second glass plate is placed on top. The sealant on both sides is pressed down and examined under strong light. If striations or streaks appear, the test should be repeated with additional extruded material.
Three tests are provided for the moisture vapour transmission (MVT) and permeability of a sealant. The MVT is defined as the rate of MVT through a barrier in g/24h*m2. The water vapour permeability is the MVT multiplied by the thickness of the sample divided by the vapour pressure difference between the two sides in g*cm/24hr*m2°*mmHg.
The simplified cup primary test method involves slowly and thoroughly mixing 100 g
(3.5 oz) of sealant base with a curing agent for two to three minutes in a PTFE ring on a PTFE sheet. A second PTFE sheet is placed on the sealant, and pressure is placed on one of the lites of glass. Excess material is forced out, and the assembly is fastened with clamps.
After initial curing, the clamps, glass, and PTFE sheets are removed, and then the specimen is forced out of the PTFE ring and checked for the absence of bubbles.
Curing continues for another seven days. The specimen is then placed in a 50 mm (2 in.) diameter petri dish filled halfway with distilled water. The specimen is sealed on the dish and cured for another day.
Next, the assembly is placed in a desiccator where zero per cent relative humidity (RH) is maintained by a molecular sieve replaced every week. The petri dish with the sealant is weighed twice a week on an analytical balance, and the weight is plotted against elapsed time.
After three and four weeks, weight loss should become linear, indicating a steady state of MVT exists. Calculations are then applied to determine both MVT and permeability.
IGMA TM-2400 also provides instructions for an automated method and an alternate automated method for testing these values but notes that a third-party laboratory usually performs these tests.
Shear testing is performed in a number of different ways. The dead load method for shear testing is a primary and secondary test method, which is a laboratory procedure for determining the ability of a sealant to resist shear forces exerted by dead loading after the tack-free condition has been achieved. Dead load is defined as the condition which occurs when one or more panes of glass in a multiple pane IGU are in an unsupported condition relative to the other pane of panes of glass in the same unit, except for the support supplied by the strength of the sealant(s).
This is an important test because some sealants do not gain full adhesive properties until some time after the tack-free condition has been achieved. This method provides a basis for judging when it may be safe to handle, pack, store, or ship the IGUs without experiencing adverse stresses and loss of adhesion of the sealant to the glass and metal components.
For this test, a cured specimen is placed in a deal load tester. Immediately afterward, a 10 kg (22 lb) weight is placed on the platform and the plunger assembly and left for 10 minutes. Any movement of the unsupported light is noted in millimetres. In addition, the adhesion characteristics of the sealant to the spacer and the glass should be observed.
Another primary test method for creep determines the ability of a hot-applied sealant to resist shear forces exerted by dead loading.
An overlap shear test measures sealant adhesion to glass, aluminum, and galvanized steel spacers and the shear strength.
To perform the primary test method, 300 g (10.6 oz) of sealant base is mixed with the appropriate curing agent for two or three minutes. Two glass specimens are bonded with the sealant to produce a 25.4 mm (1 in.) overlap. Separately, the aluminum and galvanized steel spacers are bonded similarly. After curing, each specimen is mounted to a tensile tester and pulled in opposite directions at 50 mm (2 in.) per minute. The PSI is then calculated per IGMA TM-2400 instructions.
An alternate method to test overlap shear involves heating the second substrate in a forced draft oven prior to bonding it to the first substrate, which has had 25.4 x 25.4 x 3.2 mm (1 x 1 x 0.125 in.) of sealant applied to it.
Another very important value to test is the sealant adhesion, which is critical to ensure the units do not slide or shift.
The primary test method for tensile peel strength is used to evaluate adhesion. Like previous tests, 100 g (3.5 oz) of sealant base with the appropriate curing agent is mixed for two to three minutes. The sealant is then buttered over half the length of the glass strips. Additional sealant is then applied to the glass, and aluminum strips are placed over it. The bars are set on either side of the prepared panel.
The panels are placed in a 49 C (120 F) oven for two to three hours, then removed and left at ambient conditions for 24 hours. They are then put in the tensile testing machine and pulled at a rate of 50.8 mm (2 in.) per minute, and the level of adhesion loss is recorded. The method also offers a long-term exposure testing option.
A hand peel secondary method involves applying a patty of sealant to a glass panel and embedding a 50.8 mm (2 in.) section of the spacer stock in the patty with the balance of the spacer section protruding beyond the edge of the patty to serve as a handle. The same applies to the metal specimens.
After curing for 24 hours, adhesion to the metal is tested by lifting or twisting the spacer section to apply tension to the band area and noting any adhesion failure and the effort used to affect the movement of the spacer.
Using a razor knife, parallel cuts are made through the patty. The razor blade is run under the patty at one end of the section to produce a tab of sealant free from the panel. The tab is used as a grip, and tensile peel is applied to the sealant. Adhesion loss and effort used to affect movement are noted.
The document also gives instructions for a 180-degree peel adhesion test.
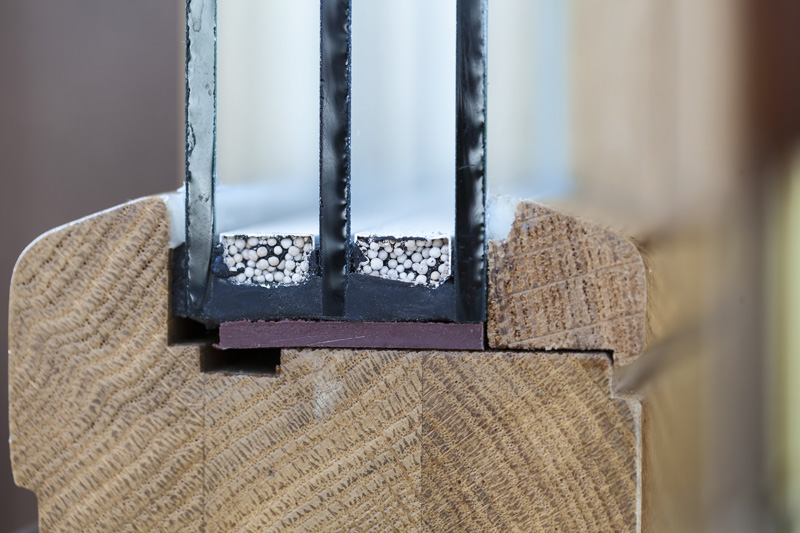
Sealing the deal
Since the sealant is such a critical aspect of IGU performance, the above-delineated tests and more have been developed to help ensure the consistency of fabrication and installation characteristics of high-performing IGUs.
By better understanding the important role of high-quality sealants in glazing assemblies, professionals will be better equipped to ensure their ultimate success.
Take our quiz and test your knowledge!
Author
Amy Roberts oversees the FGIA Canadian standards and regulatory building and energy codes, as well as the Insulating Glass Manufacturers Association of Canada (IGMAC) Certification Program for Insulating Glass Units (IGUs). She has more than 20 years of industry experience in glass and IG manufacturing, including residential and commercial window manufacturing. She can be reached at aroberts@fgiaonline.org.