Putting Pen To Paper: A brief course in spec writing
With the prescriptive method, basic materials (e.g. concrete, stainless steel, or wood) can be specified by a generic description or by reference to the corresponding standards. When specifying materials like a certain brick or ceramic tile using the proprietary method, one should use a manufacturer’s model number, or several models of different manufacturers (when all are acceptable alternatives). For more complex systems like mechanical equipment, elevators, or even a curtain wall, one should consider using the performance method to provide criteria related to the end results.
That said, employing a combination of the three methods can be more practical and can help maintain a project’s integrity. It is also recommended specifiers avoid very long texts, while ensuring a product truly satisfies the requirements of the cited standards or responds to the performance criteria. This method also allows the submission of alternate solutions other than the trade names mentioned.
Regardless of the method selected, one should consider creating a system within the project manual to ensure the drawings refer back to specified products. This could take the form of including a short description on the drawing itself. An alternative is to use an abbreviation and the spec section number in which the product is specified (e.g. MEMB.2, section 07 10 00, or CLKG.5, section 07 90 00, for a given vapour barrier membrane or a caulking, respectively).
Levels of specification
Specifications can be prepared at three different phases: the concept design, preliminary design, and final design.
- The concept design phase refers to a short description of the design’s intentions in textual form that includes products and systems and is part of the concept design report. The main tool employed is UniFormat (or UNIFORMAT II), level ‘2’ or level ‘3,’ and the new PPDFormat, which puts this very initial specification of the project into context.
- The preliminary design phase is a more detailed specification of the products and systems required using more technical language. Part of the preliminary design report, this phase also uses UniFormat (or UNIFORMAT II), although at levels ‘3’ or even ‘4’ or ‘5.’ Here, a summary of general conditions and requirements may be incorporated. PPDFormat is also a good guide to follow at this phase.
- The final design phase corresponds to the project manual, which contains not only a detailed description of all products and systems, but also installation procedures and environmental and other conditions under which they must be executed. MasterFormat (with its 50 divisions) and SectionFormat/PageFormat are the tools to be used; standard specifications, such as National Master Specification (NMS) or office master or typical specs, help facilitate the production of this essential document.
The project manual contains three principal parts of groups, as categorized by MasterFormat:
- procurement and contracting requirements (Division 00);
- general requirements (Division 01); and
- technical requirements (Divisions 02 to 49, some of which are not assigned and are for future use).
The first two components may vary in some significant ways according to the type of contract (e.g. stipulated price contract, construction management, or design-construction).
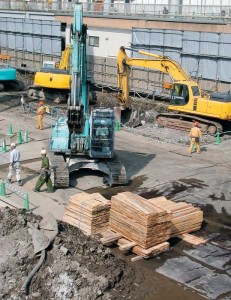
Photo © BigStockPhoto/Radu Razvan
Whether comprehensive, short form, or very short form, it is recommended the project manual maintain the main structure of the standard specs (i.e. sections based on types of work as established by MasterFormat, and each section in three parts [i.e. General, Products, and Execution] as prescribed by SectionFormat). Once again, the specifier should consider writing the project manual on standard letter-sized paper—per PageFormat instructions—as opposed to using drawing sheets, even if it is only a few pages. Other factors to take into consideration and manage are the project manual’s various publications and modifications required during the bid period and construction.
During the course of a project, the manual can be issued:
- ‘for comments’—to obtain comments from the client or other professionals (at different stages of its completion);
- ‘for tender’—to start the bidding process (at 100 per cent of its completion);
- ‘for construction’—incorporating changes made during the bid period, to sign the contract, and to begin construction; and
- ‘as-built’—to include changes made during construction.
The project manual can be issued in consecutive packages (i.e. for multiple contracts with construction management), in repetitive packages (i.e. when constructing in phases), and, for practical reasons, in several volumes.
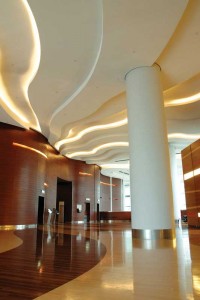
Photo © BigStockPhoto/Norman Chan
Changes during the bid period may result from additional client requirements, clarification requests from bidders, or late information. These modifications are issued in addenda, which will have the same legal value as the project manual itself. For similar and other reasons, changes during construction are issued by change directives and change orders, and also acquire contractual force.
Putting together the project manual
It is always wise to create a checklist for the work procedures when preparing a project manual. Apart from determining the type of spec and contract, these procedures include:
- selecting products section by section in conjunction with the project designer and project manager, and verifying the choice is still available on the market;
- co-ordinating specs and drawings, ensuring they complete each other and are easily interrelated;
- verifying administrative requirements with the project manager (who in turn must obtain the client’s requirements), including compliance with prescriptions of, for example, FM Global, and of the Leadership in Energy and Environmental Design (LEED) program, as well as specific extended warranties;
- determining what specialties will be dealt with by external consultants, such as finish hardware, asbestos removal, and elevators;
- establishing items to be co-ordinated with the engineers and other consultants, like masonry reinforcement and load-bearing stud walls; and
- checking the requirement for tests and inspections to be paid by the client (e.g. air/vapour barrier membranes, roofing, and curtain walls).
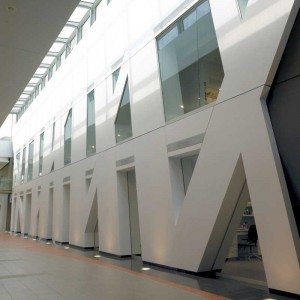
Photos © Jacques Frenette
More than a specification
Although ‘project manual’ and ‘specification’ are two terms frequently used to mean the same thing, they are not, in fact, synonymous. The former has a larger meaning than the latter. The project manual ties everything together to ensure all those participating in a project understand the intricate relationships involved in the creation of a building. It completes the design process, and reflects all the care and experience the design firm can offer its clients. (See this author’s earlier article, “Putting Together the Project Manual” in the March 2009 issue of Construction Canada. Visit www.constructioncanada.net and select “Archives.”) Indeed, as this author has written in an earlier issue of Construction Canada, “it is the depository of the knowledge, experience, and history of a professional firm.”2 As such, it should be taken seriously and prepared with care and high proficiency. That is the challenge of the spec writer’s profession.
Vrej-Armen Artinian, CSC, CSI, is a graduate of Cairo University (B.Arch, 1964) and McGill University (M.Arch, 1969). He started his career specializing in the design of school buildings, and then moved on to industrial buildings, laboratories, and research centres. Artinian has been a specification writer at Montréal-based NFOE et associés architectes since 1992. He is a member of Construction Specifications Canada (CSC), Ordre des architectes du Québec (OAQ), Construction Specifications Institute (CSI), Conseil du bâtiment durable du Canada (CBDCa) Section du Québec, and Conseil de l’enveloppe du bâtiment du Québec (CEBQ). A writer contributing to Montréal’s Armenian press, he can be contacted via e-mail at vrejarmen@hotmail.com.