Providing opportunities with fluid-applied thermal break coatings
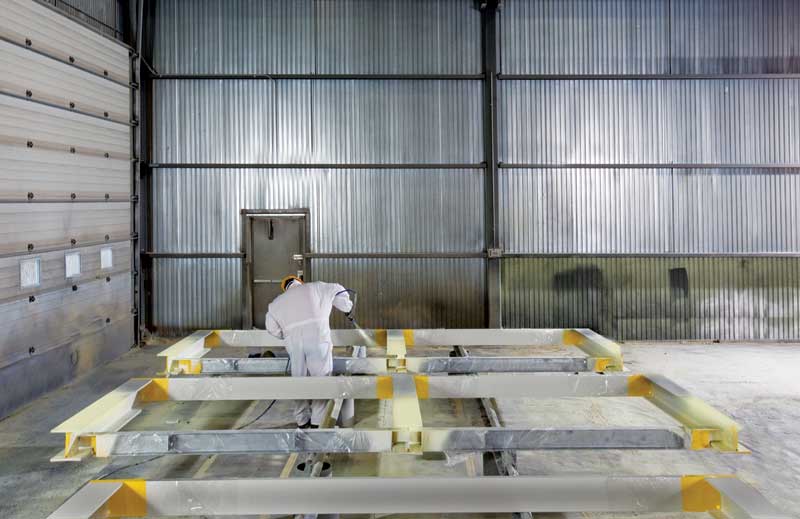
Condensation and IAQ requirements
The health benefits of a building with a reduced potential for mould growth in wall systems are desirable for building owners who want to avoid litigation due to sick building syndrome. The warmer interior temperature of the structural members of the building can be improved by liquid-applied thermal coatings.
The forthcoming LEED for New Construction (NC) v4 will address the thermal comfort of occupants in its Indoor Environment Quality (EQ) Credit 5, Thermal Comfort. The relevant standard is ASHRAE 55-2010, Thermal Comfort Conditions for Human Occupancy, with errata or local equivalent. Without thermal bridging within the building envelope, project teams that design thermally broken balconies can meet the requirement of LEED v4 Credit 5.
This technology is not only driven by performance and need, but has evolved to water-based technology as well as low- or zero-volatile organic compounds (VOCs), meeting LEED requirements for all design parameters.
The compatibility of air and vapour barriers, along with sealants and cementitious and intumescent fireproofing, is key to all designers for building envelope code requirements. In other words, the inadvertent development of an aerogel-filled thermal break coating is a workable solution to a nagging design problem.
Interior and exterior areas where thermal bridging is a concern
For fenestration within interior rooms where the relative humidity (RH) can reach high levels in the cold winter months and thermal bridging has not been mitigated, ice buildup on windows can present moisture issue to the materials and systems surrounding the opening. As the ice melts, the moisture can migrate to the drywall and damage the interior walls, as well as provide moisture for mould growth.
To mitigate the surface temperature of the window frames, an aerogel-insulated coating can be applied; case studies have shown the temperatures from an infrared (IR) camera can be raised significantly to above the dewpoint to greatly reduce and potentially eliminate condensation. For example, an existing aluminum window frame within a high-RH room with an outside temperature of −2 C (28 F) will go from a spot surface temperature reading of 8.4 to 20.3 C (47.1 to 68.5 F) once 2.8 mm (110 mils) of the aerogel coating has been applied.
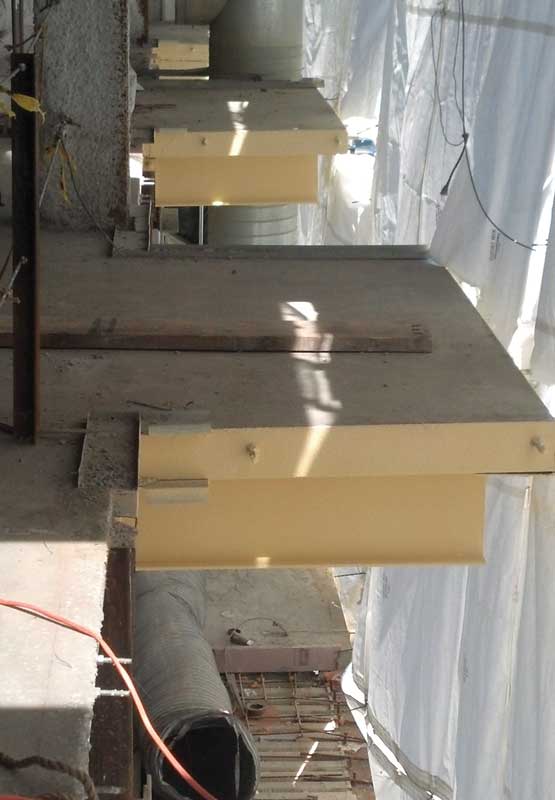
Another common area within the interior of the building affected by condensation is where the walls and ceilings meet at a corner. Often, mould is noticeable on the ceiling in these areas.
At the intersection of the interior and exterior on multi-family construction, balconies are a common source of heat lost and condensation issues. The balcony slab extends to the outside air, exposing the entire slab to exterior temperatures via thermal bridging. The intersection of the low- and high-energy temperatures heating and cooling energy throughout the building is often lost, with any exterior systems in contact or nearby absorbing more moisture from condensation than they can withstand.
Dangers of continuous condensation cycles
Structural steel beams, their hardware, or their welds can weaken when they remain wet from moisture infiltration. This can lead to costly building code violations, mitigation projects, or structural failure (especially when leaking exterior systems exacerbate the issue compounded with heavy snow loads and chlorine rock salt applied for years on roof pavers). (These cases are rare, but have happened. For an example, see the forensic engineering investigation into the Algo Centre Mall Collapse in Elliot Lake, Ont.)
Insulated fluid-applied coatings were first used on boilers and pipelines where preventing steel corrosion under insulation (CUI) was of vital concern. Corrosion can attack the jacketing, insulation hardware, or the underlying steel. The National Board of Boiler and Pressure Vessel Inspectors (NB) is a great resource for further information on steel corrosion under insulation.
These coatings are durable and corrosion-resistant, bonding to the substrate to greatly reduce issues associated with CUI. Once moisture and thermal protection exterior systems have been installed, the property installed insulated coating will provide peace of mind to the project team, building owners, and occupants for decades to come.