Providing opportunities with fluid-applied thermal break coatings
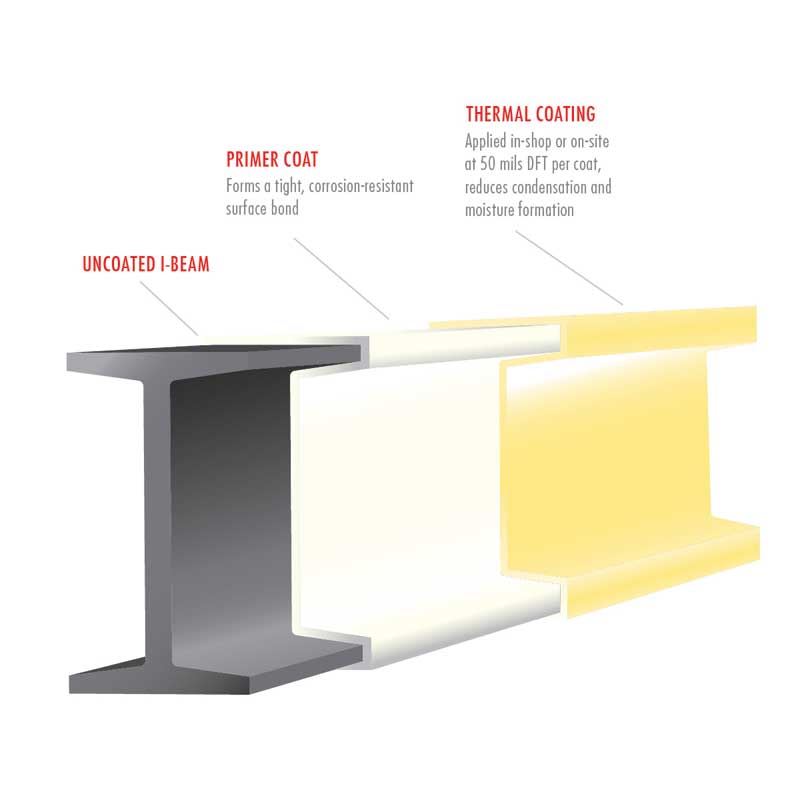
Understanding the architectural applications
Architects designing with cantilevered beams, concrete balconies, roof penetrations, canopies, spandrel glass, and ornamental architectural features must address the cold-to-hot issue. At these moments in the design, moisture formation has to be taken into consideration or problems can occur. Otherwise, the creative approach would have to be scaled back.
For architectural applications, the thermal performance of fluid-applied acrylic insulation coating was recently documented by a Morrison Hershfield report commissioned by a manufacturer. The findings of the engineering firm’s thermal analysis of the products were very promising for a variety of common construction details, including:
- structural steel beams that bypass the thermal insulation;
- structural clips for cladding of exterior insulated assemblies;
- steel stud assemblies; and
- concrete slabs.
The testing by Morrison Hershfield included three coating thicknesses—1.5 mm (60 mil), 3 mm (120 mil), and 13 mm (½ in.)—using a conductivity of 0.0356 W/m·KL (0.0202 BTU/hr·ft·F). The thermal analysis was completed with 3D heat transfer software.
Unlike structural thermal break products, insulated coatings do not require additional engineering to determine whether they will support the load. Insulated coatings can also be more cost-effective by comparison to the steel fabrication and installation of structural thermal breaks and pads, which also require expensive bushings and washers. The aerogel-based coatings can be shop- or field-applied and can be utilized in both new construction or retrofits. However, the benefits of design flexibility with both the steel and the concrete elements can be realized, along with simplified specifications and scheduling.
Thermal coatings work by providing thermal conductivity levels at 35 mW/mk compared to 260 mW/mk for thermal-break pads. The thermal insulating coating prevents the surface temperature from lowering below the dewpoint so moisture does not condense—even without a physical break in the beam.
Overall, design professionals see the potential for cost reductions compared to structural products with aerogel coatings and the prospect of simpler specifications. Manufacturers have drawings and specifications with construction details available for keeping interiors warmer and avoiding condensation and mould formation within the building envelope.
LEED and energy code compliance considerations
The LEED energy efficiency credits referencing ASHRAE 90.1-2010 will gain the most contributions with thermally broken designs. Further, the new design approach indirectly plays a role in assisting with Indoor Environment Quality (EQ) Credit 5, Thermal Comfort.
The overall energy benchmark ASHRAE 90.1-2010 is used by project teams to meet energy codes and voluntary green building programs. Generally, the Canadian and U.S. versions of LEED are harmonious. (There are some options to follow Canadian codes, but they are not required.) A great reference for guidance on building envelope thermal bridging (BETB) was published initially by BC Hydro and recently updated in BETA 1.1 in April 2016. Additional construction details were added and the new version focuses only on thermal performance data; sections related to cost benefit analysis and market transformation were removed in BETA 1.1.
However, some mid-rise multi-family projects at four or more storeys in height could be covered by the LEED for Homes Rating System: Multi-family Mid-rise. In LEED NC, healthcare projects must develop a moisture control plan per EQ Credit 3, Construction Indoor Air Quality Management Plan.
The continuous insulation requirements in energy codes are enhanced by thermal break design details. Often, much attention is paid to upgrading HVAC and lighting systems with increased R-values in the building envelope. Fluid-applied thermal coatings have the potential to create additional energy efficient upgrades to the exterior facing systems.
The latest version of ASHRAE 90.1 and the 2011 National Energy Code for Buildings (NECB) require increased energy performance design details. Building energy performance upgrades, therefore, must include more efficient HVAC, lighting, and insulation systems, but these are not always enough while maintaining the building owner’s desires for unique esthetics and flexible design requirements. ASHRAE 90.1-2010 calls for the additional step of continuous insulation (ci) throughout the entire building envelope. The NECB is based on U-values only, and there is no prescriptive insulation requirements. Once all these requirements have been met, thermal break coatings can further assist project teams with the potential for gaining additional energy performance to comply with the new energy codes.
In the past, it was difficult to comprehensively account for all thermal bridging in U-value calculations—in fact, it was also thought to be a relatively minor impact. Now, there is more of a mainstream awareness the effect is significant; further, there are better tools/data to comprehensively address it. Codes and standards are in the process of evolving to better estimate U-values by more holistically accounting for thermal bridging.
British Columbia, Ontario, Alberta, Manitoba, and Nova Scotia have adopted NECB, but the first two provinces have alternative compliance paths that include compliance paths to ASHRAE 90.1. However, in Ontario, there are supplement requirements outlined by SB-10, Energy Efficiency Supplement, that supersede the ASHRAE U-value requirements with much more stringent values. There is also so-called ‘stretch codes’ in the works that could mean bylaws requiring buildings to exceed both NECB and ASHRAE 90.1.