Protecting buildings with hydrophobic coatings
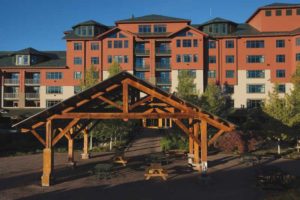
Reclad delivers armour to condominium building
Along the Atlantic Ocean in North Myrtle Beach, the Edgewater Condominiums needed an upgrade to the 10-year-old stucco facade. The board of directors worked with the project team for the 10-storey condo building and made the decision to remove the cladding and install a continuous insulation (ci) wall system, with a super-hydrophobic finish which had self-cleaning properties.
“The hydrophobic finish does a remarkable job at keeping the building looking clean and new,” says Chris Rush, president of the Edgewater Condominium Associations (COA) board of directors. “The buildings completed more than a year ago [with the same finish system] looks just as good as the building that was just completed.”
The system featured a continuous, air and water-resistive barrier (WRB) which helps the building prevent moisture intrusion, but was also vapour permeable to allow quick drying. As added protection, the lack of fasteners in the adhesively applied continuous wall system further minimized potential moisture and air intrusion into the substrate.
Specifying a ci wall system helped to lower the utility bill by 20 per cent and improved comfort levels for residents. The water- and weather-resistant properties of the hydrophobic finish provided additional protection against damage and water intrusion during three hurricanes—Florence, Michael, and Dorian—which brought 120 km/h (75 mph) winds. What protects the building is the entire building enclosure and the finish layer provides the esthetics and protection against rain, but in the case of hurricane, there needs to specifically engineered wall systems that must meet strict criteria.
Makeover to defend resort hotel
The Steamboat Grand Resort in the popular ski area of Steamboat Springs, Colorado, sits at an altitude of 2,103 m (6,900 ft). The area has more than 300 days of sunshine per year and some of the highest snowfall totals in the state, wreaking havoc on traditional facades and water-based coatings. The climate conditions caused extensive damage to the roof, resulting in water intrusion, which led to the original facade being covered with mould and efflorescence. The original building cladding was stucco and exterior insulation and finish system (EIFS). After more than a decade, the exterior facade was worn by time and the weather and was in need of a facelift.
The 328-room resort hotel was the ideal location for a super-hydrophobic coating with self-cleaning properties. The project team could also apply the new coating without disturbing guests and visitors—an added benefit to the hotel’s operations.
Reliable armour
A building’s coating is its first line of defence; it is the initial layer of protection from the elements and human impact. Building owners, developers, and contractors can change the paradigm when it comes to long-term building performance and esthetic appearance by specifying more durable coating solutions, such as hydrophobic coatings.
With the cost of resources continuing to rise, architects and building owners continue to look for ways to improve building performance and extend its esthetic allure. By utilizing exterior finishes or coatings with hydrophobic technology, the cost of maintaining the visual apparency of a building can be greatly reduced.
Hydrophobic exterior finishes and coatings provide exceptional resistance to algae and mildew growth and can reduce maintenance costs by increasing cycle time between recoats. The ability to repel water contributes to increased weather resistance, reduced dirt pick-up, and added protection from wind-driven rain. Hydrophobic finishes or coatings keep the building looking good longer, perform better against outdoor elements, and can lower a building’s carbon footprint.
Verified standard testing has proven super-hydrophobic and hydrophobic products can repel water, increase weather resistance, reduce dirt pick-up, and provide added protection from wind-driven rain. As a result, it can keep buildings clean for longer and reduce the need to recoat.
Advancements in material science mean longer, more reliable coatings, which can resist the forces of nature, but at the same time, are inspired by that very nature.
James Howell is a product manager for Sto Corp. and focuses on on facade claddings. He has a degree in business management and has more than 20 years of experience working with exterior insulation and finish system (EIFS), stucco, air, and moisture barriers in research and development, and marketing departments.