Protecting buildings with hydrophobic coatings
One of the most hydrophobic surfaces in everyday use is polytetrafluoroethylene (PTFE). In the kitchen, one can see a droplet of water will roll around a PTFE-coated frying pan. PTFE has a contact angle of around 105 degrees. Surfaces with a contact angle greater than 150 are called super-hydrophobic surfaces.
Understanding super-hydrophobicity
The term “super-hydrophobic” has become the common nomenclature to describe any surface which easily repels liquids. Sometimes it is used accurately, but most times, it is incorrect. A super-hydrophobic coating has a greater contact angle than a hydrophobic coating. A hydrophobic coating only needs to have a 90 degree or greater contact angle; whereas a super-hydrophobic coating typically has a coating contact angle of greater than 150 degrees.
To understand the basic ideas behind many super-hydrophobic surfaces, both in nature and artificial environments, consider a “bed of nails.” If a balloon is pushed against a single nail, the nail penetrates the skin of the balloon, making it pop easily. However, if there is a bed containing many closely spaced nails, the balloon can be pushed quite hard against the nails, and it will not pop. This is because pushing against many points spreads the force and reduces pressure.
Many plants and animals have evolved to have surfaces with much higher contact angles than that of PTFE. In the case of plants, super-hydrophobic surfaces can be created through the deposition of wax towers, such as on cabbage leaves, or via hairs (e.g. on the leaves of Lady’s Mantle). For animals, it can be through the use of super-hydrophobic structures. This could be the “coat” which allows a water boatman to pass through the surface of a pond without getting trapped by surface tension, or the scale structure of a butterfly’s wing that stops them getting waterlogged in rain.
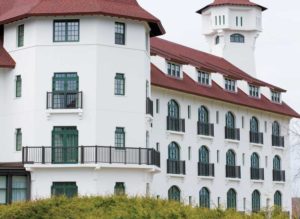
Performance in design
Designing a new building or recoating or recladding an existing facility comes with expectations to deliver a long-lasting structure and comfort for occupants. Five factors which impact the performance of a building and the exterior coating:
- Mechanical action, such as abrasions, hail, swelling, and building movement. Extreme weather, such as hail, can damage the structure or cause abrasions which compromise any coating applied to the exterior cladding.
- Air pollution, including organics such as nitrogen oxides (NO) and mineral materials such as dust. During wildfires, forest fires blow smoke and soot across the environment. In rural areas, fertilizers used on farms release nitrates into the air. In cities, hydrocarbon soot from diesel exhaust and jet exhaust leaves behind a sticky black residue. These pollutants can deteriorate the coatings and appearance of the facade.
- Biological organisms, such as mildew or fungal growth. In temperate rainforest regions, algae is common on the exterior of a building, creating an unappealing green appearance and decreasing the water-shedding effectiveness of the coating. In damp, humid climates, fungal growth can propagate and bond to coatings, making it difficult to remove and leaving a deposit on the surface of the coating.
- Bulk water includes rain, dew, snow, humidity, and other moisture and water vapour. The coating is the first face to the elements and requires effective, reliable water resistance. However, a traditional water-based coating can soften when exposed to bulk water. The softer coatings become tacky and attract dirt which does not wash away easily.
- Temperature and light effects due to climate and ultraviolet (UV) rays. Temperature and light can also degrade coatings on the exterior of buildings, making them fade after years of exposure. Moving North to South, the amount of UV exposure increases significantly.
Architects, designers, and specifiers can select from a wide variety of materials, finishes, and coatings to help protect a building’s exterior wall. The factors listed are important to different customers depending on their performance needs. This could depend on many different conditions such as climate, colour selection, or geographic location. A building owner in the downtown area, with a lot of vehicle traffic and high UV exposure, might prioritize air pollution over bulk water performance.
Acrylic coatings offer a variety of protective characteristics, including durability, fade resistance, and resistance to cracking, peeling, and chipping while bridging hairline cracks. They extend the lifetime of a building’s appearance and protect it from the elements. Applicable in new construction or a recoating situation, such coatings provide a variety of esthetic options and preserve the value of buildings by serving as a breathable, durable, attractive layer of protection.
Hydrophobic coatings are acrylic coatings which repel water. This enables faster drying of the surface, reducing the opportunity for mould, mildew, dirt, and other pollutants to grow or stick to the surface. They may be used for new construction or recoating existing buildings, and help the building maintain its esthetic appeal and perform better against the elements, while lowering maintenance costs and the frequency of recoating.
Having a super-hydrophobic or hydrophobic coating/finish, compared to a traditional one, can reduce building maintenance by as much as half or two-thirds of its original cost by extending recoat frequency and annual cleanings. In addition, by reducing mould, mildew, and algae growth on the surface of the coating/finish, it can also lower the chances of delamination or blistering—requiring less building repairs and possible moisture intrusion related issues.