Protecting a parking deck from water leakage
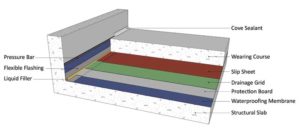
The typical parking deck comprises a waterproofing membrane adhered to the top of the structural slab, drainage grid, and wearing course. (See Figure 1) This assembly works like a rainscreen exterior wall, as most of the water trenches over the wearing surface (usually a concrete topping), while some finds its way onto the membrane and moves towards drains through the drainage grid. Therefore, the topping acts as a membrane protector and water shedding layer—similar to siding on walls. Other layers, such as protection boards, insulation, and slip sheets can also be added to improve the overall performance and durability of a structure. (See Figure 1)
An insulation layer within a deck assembly is crucial when it separates two spaces with a wide difference in temperature, such as a parking floor and an air-conditioned/heated living space. Similarly, in cold climates, the lack of insulation (i.e. thermal barrier) below a plaza deck and above a heated parking space can cause condensation issues on the exposed bottom surface of the concrete deck. In contrast to a deck separating two parking floors, a plaza deck is a supported slab providing green-scape and tree planters, in addition to pedestrian and vehicle loads, over an occupied space. Special considerations should be given to the design and construction of waterproofing systems for plaza decks; such as, selecting the proper protection courses and managing water away from the structure while maintaining the plants’ health.
Unlike fully shielded buildings, parking garages are mainly open to the elements, therefore, their concrete surfaces are more prone to deterioration, such as spalling, scaling, cracking, and delamination. Modern concretes are better designed, with higher strength, and density, with air entrainment. Reinforcement requirements have also changed to reduce corrosion potential, and control cracking. These structures are also subjected to dynamic loading conditions and destructive chemicals from de-icing materials, as well as mechanical abrasions from cleaning and snow removal equipment. In general, a full comprehensive condition review must be conducted by an experienced engineer at least every five years, or when there are signs of structural and performance issues.
Keeping water drained away from the deck will increase its service life; meanwhile, standing water rapidly deteriorates the deck components, such as the waterproofing membrane, the concrete slab, and the rebar. Water within the assembly can also cause extra damage via freezing and thawing cycles in cold climates. Maintaining a minimum slope of two per cent (6.35 mm per m [0.25 in. per ft]) at the topping for surface flow, and at the deck slab for subsurface flow, is essential to direct water towards the highly recommended double-tiered drains. Considerations should be given to the effects of structural deflections and building settlements on the magnitudes of slope to avoid buildup of membrane at drainage flange, resulting in membrane dam around the drain. (See Figure 2)
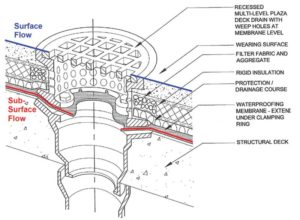
Installation inspection and flood testing
The installation quality of the waterproofing membrane is as important as the selection and design of the waterproofing system, as the integrity and continuity of the membrane are paramount to the performance and durability of the parking deck system. Hiring a third-party reviewer to inspect installation and test the system is beneficial—especially before adding any additional layers and the wearing course. Further, visual reviews should also be conducted frequently as part of the quality control (QC) and testing can be employed as a quality assurance (QA) measure.