Producing quality polished concrete floor slabs
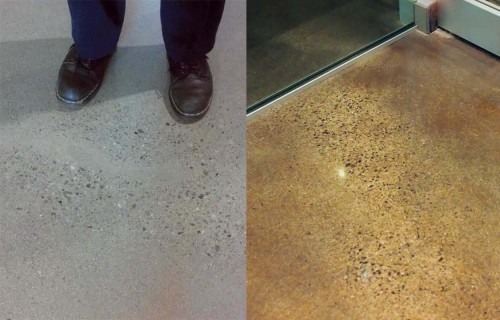
Optimum esthetic quality
There are many factors to be carefully evaluated to lessen or avoid potential problems and achieve adequate results.
Near-surface compressive strength
Achieving adequate compressive strength of test cylinders cast from concrete used for slabs and toppings is rarely a problem. However, achievement of optimal compressive strength of the near-surface concrete is critical for adequate wear-resistance performance of polished concrete—particularly when dyes or stains are included as part of the process, and this is not necessarily guaranteed by high compressive strength results.
Although concrete mix design parameters have a major influence on achievement of optimal near-surface concrete strength, even more important factors include whether ambient conditions are conducive to rapid drying, and how effective protection measures are during placement, finishing, and curing. Under rapid drying conditions, even high-strength concrete may not provide the required wear and abrasion resistance properties without adequate precautions. Therefore, planning for appropriate execution of protection measures can be critical.
Rapid drying conditions
In cases when rapid drying conditions prevail during the placement and finishing operations, and the rate of evaporation becomes faster than the concrete can replenish surface moisture with bleed water, the concrete finishers can face difficulties timing the commencement and duration of the various operations—particularly the floating and trowelling procedures.
Rapid drying of the surface before commencement of curing procedures can then lead to several concerns. For example, after concrete placement desiccation of the near-surface zones could be sufficient to adversely influence the natural cement hydration reactions, leading to lower strength and reduced wear and abrasion resistance. This phenomenon could result in non-uniform wear patterns and varying degrees of finished gloss within the polished concrete finish. Further, difficult finishing conditions can result in non-uniform distribution of fine and coarse aggregates within the upper thickness of plastic concrete—especially if the concrete is over-worked. This could lead to non-uniform exposure of aggregate. Under extreme conditions, rapid drying of the surface can result in plastic shrinkage, cracking, or crazing—especially if protection is not provided during and after the finishing operation, and curing does not commence immediately after. (When drying conditions are severe during placement and finishing operations, CSA A23.1-09 (R2014) requires one or more precautions be taken, including dampening the subgrade prior to placement, covering the concrete surface with polyethylene sheeting between the various finishing operations, and applying fog spray immediately after placement and before finishing, or as a continuous operation. The use of spray-on mono-molecular materials (i.e. evaporation retardants) is also permitted, although certain precautions are advised).
Chemical densification
Contrary to some claims, grinding and honing the surface of concrete does not ‘close up’ or toughen the near surface thickness. In fact, these operations ‘open up’ the surface and increase porosity and the potential for the development of wear-patterns. This is why liquid chemical densifiers after the initial grinding operations are used. If stains or dyes are to be employed, they should be in advance of the chemical densification.
The most commonly applied densifiers are based on potassium, sodium, or lithium silicate. These materials chemically react with calcium hydroxide compounds formed by portland cement concrete’s naturally occurring hydration reactions. In very simple terms, the result of the reactions is the formation of additional calcium silicate hydrate within the cement matrix—a much more inert hydrated compound. These products of the reactions fill the capillary cores of the cement paste matrix, resulting in a denser, tougher near-surface zone.
However, use of SCMs, such as fly ash or ground-granulated blast-surface slag, have similar reactions and can therefore ‘interfere’ with the near-surface zone densification effectiveness by varying degrees. Concrete suppliers will routinely include CSMs within their mix design, and are permitted to do so by CSA A23.1-09 (R2014). However, the type of CSM and the amount used will vary from plant to plant and from region to region, potentially leading to variations in the results of polished concrete applications from project to project.
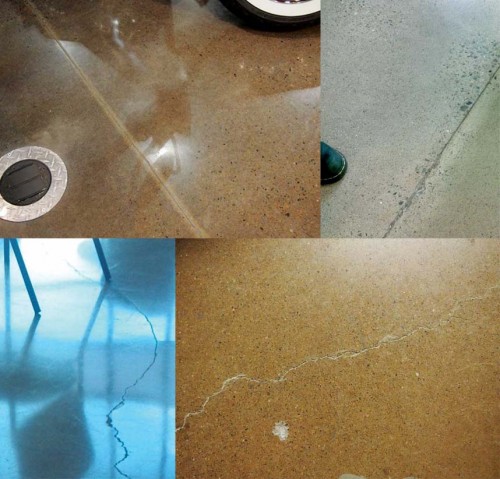
Floor flatness criteria
Uniformity of aggregate exposure is also influenced by the techniques used by the concrete floor contractor to achieve a given floor flatness (FF) and smoothness. (For more, see “Concrete Floors: Flatness vs. Smoothness” by Keith Robinson in the September 2015 issue of Construction Canada). CPAA recommends use of a highway straightedge and the achievement of an overall flatness of floor flatness FF50, with a minimum local value of FF35. However, to achieve this degree of flatness, CSA A23.1-09 (R2014) recommends special narrow-strip placement with mechanical screeds and highway straightedges. These are unlikely to be utilized by the CFC unless required by the specifications. However, this author believes a more realistic tolerance for overall flatness would be a FF25, achieved by a procedure typically including mechanical screeding and use of a highway straightedge before steel trowel finishing. Although they enhance the achievement of optimal flatness, great care must be taken when using a highway straightedge to avoid over-working the surface.
Other criteria
Other conventional practices that can adversely influence the achievement of acceptable esthetic quality include the use of below-slab moisture-vapour retarders (MVRs), construction of toppings, and curing procedures. Under rapid drying conditions, MVRs can provide similar effects to toppings cast over precast suspended slabs. Both can accentuate the problems associated with timing and duration of the various finishing operations, due to the creation of differential moisture conditions between the upper and lower zones of the slab or topping. This phenomenon can increase the potential for problems associated with curling and warping, as well as drying, shrinkage, and cracking. Topping delaminations can also occur under severe rapid drying conditions.
The absence of curing, or poor curing practices, can also result in similar defects. After termination of curing, it is important the surfaces of cured concrete slabs be kept free of any objects until polished concrete operations can begin. (Ideally, storage on a polished concrete floor should be prevented in any event.) This is especially important when dyes, tints, or stains are used. It can also be a particular concern if rapid drying conditions were experienced during concrete placement and finishing, or if curing was delayed. The undesirable result can be the creation of ‘footprints’ of the objects, which may become evident because of their influence on the uniformity of hydration reactions.
CPAA recommends evaporation control and wet curing, rather than topically applied curing compounds. However, for optimal results, this author recommends the concrete surface be well-wetted and covered with polyethylene sheeting immediately after final finishing. The sheeting should be positioned so contraction joints can be cut during the curing process, as soon as the concrete has sufficiently stiffened. The surface should then remain continuously wet for seven days.
Most product manufacturers recommend a minimum delay of 56 days be provided so the effects of drying shrinkage can be mitigated and undesirable stress can be avoided at joints—both of which can be a complication regarding timing for joint-filling. However, this requirement is due to the extended hydration reactions created by use of suppplementary cementing materials, which are not recommended to be used for concrete required to be polished. Therefore, in theory, joints could be filled much earlier.