Prefabricated composite structures: The best of both worlds
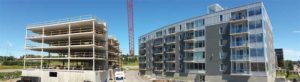
Photos courtesy Dominic Lemieux
In the Luxenbourg projects, the thermal bridge was eliminated by using pre-stressed solid slabs with an integrated 900-mm (35-in.) cantilever. Once the slabs were installed, urethane was sprayed under them and polystyrene foam was used over the slabs, thereby significantly reducing the thermal bridge. The polystyrene was then used to anchor the pipes for the radiant floor system.
Lessons learned
The Luxenbourg project provided experiences that will lead to many new innovations which will be applied again in the future phases of the development.
Lesson learned 1: The more prefabricated elements the better
The Luxenbourg phase II & III building envelopes were almost completely prefabricated. The only part of the exterior envelope that were not prefabricated was the corners of the building and it consisted of a field installed curtain wall. These small sections of the envelope took longer than the rest of the building to install and led to condensation issues for the occupants during winter. The next phase of Luxenbourg will have corner windows like the Luxenbourg phase I. Also, with the current labour shortage situation, having building techniques requiring less manpower onsite is usually simpler to manage.
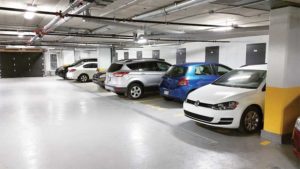
Lesson learned 2: Long spans equal flexibility
The combination of hollow-core slabs and composite beams created a large open space giving full flexibility to the interior design team. Originally, the Luxenbourg phase II and III were supposed to have units of similar areas as phase I. However, after a year of occupancy of the Luxenbourg phase 1, the owner realized the yield was greater with smaller units, so he instructed his design team to try to fit one more unit per level in phase II and III.
Lesson learned 3: Designing precast cantilever balconies without a thermal bridge is possible
The precast cantilever balconies of Luxenbourg phase II and III turned out to be a success over the previous design of an independent structure for the balconies of the Luxenbourg phase I. Although the first phase also eliminated the thermal bridge, having to bring a crane back to the jobsite just to install balconies proved to be costly and time consuming.
Conclusion
As explained above, the Luxenbourg projects have been an accomplishment because of the successful implementation of construction innovations and overall quality of the building. The next four phases will incorporate the best practices from its first three phases but one could simply sum it up as: the more prefabrication the better.
Dominic Lemieux, P.Eng., is a licensed structural engineer in Ontario and Québec and has introduced shallow composite beams to over 150 projects in North America. He studied civil engineering at the Universitat Politècnica de Catalunya in Barcelona, Spain, and graduated in civil engineering at L’École de Téchnologie Supérieure in Montréal. Lemieux is Peikko North-America’s vice-president, Precast Concrete Institute’s (PCI’s) total precast committee chair and, PCI’s precast hollow-core slab committee’s vice-chair. He can be reached at via e-mail at dominic.lemieux@peikko.com.