Prefabricated composite structures: The best of both worlds
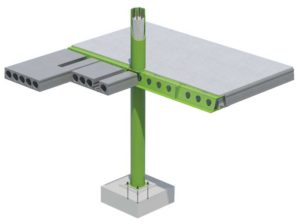
Images courtesy Peikko
Faster access to other construction trades
In addition to a faster erection time with a small crew, the prefabricated structural components offer another major benefit: Minimal shoring. Additionally, the shoring posts can be removed days after they are installed instead of weeks as it is typically seen in poured-in-place concrete construction.
The reason why the shoring is minimal with a prefabricated composite structure, such as the one used in the Luxenbourg projects, is that all the components do not require on-site curing time. The composite columns and the shallow trapezoidal composite beams are structural steel profiles which can carry the weight of the hollow-core slabs. The precast slabs are already cured when they arrive onsite and do not require shoring onsite. Prefabricated structures of this type only require shoring during erection to prevent the rotation of the composite beams when loading all the slabs on the same side of the shallow trapezoidal composite beams. This shoring usually consists of only one 100 kN post at each end of the beam. Once the slabs are loaded on the other side of the trapezoidal beam section, the rotation at the column is annulled. As an additional precaution during erection, the shoring posts are removed a few days after the floor above is grouted instead of several weeks as it is typically seen in cast-in-place structures.
Innovation 2: Eliminating the need for fireproofing
Due to their concrete infill, composite structures can provide a fire resistance of two hours or more. Even if their capacity does reduce in the case of a fire, like any other type of structure, the design safety factor applied for the live load is reduced from a multiplicator of 1.5 to 0.5 in the case of fire. In other words, if the live load used for the design of the structure is 4.8 kPa (100 psf), for ambient temperature this value is multiplied by 1.5 so one would use 7.2 kPa (150 psf) for the design of the structure. When designing a structure in case of fire, the 4.8 kPa value is multiplied by 0.5 so the applied design load on the structure would be 2.4 kPa (50 psf).
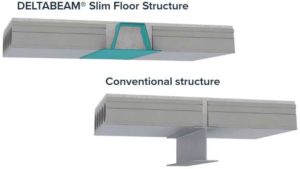
The shallow trapezoidal composite beams have been tested at the Underwriters Laboratories of Canada (ULC) based on CAN/ULC-S101, Standard Methods of Fire Endurance Tests of Buildings, and has obtained a ULC fire rating of four hours. Even with the structural steel remaining exposed, the fire test demonstrated the concrete infill along with the additional reinforcement placed inside the beam at the production facility is sufficient enough to provide the required strength to support a floor during a fire for several hours.
The National Building Code of Canada (NBC) provides guidance on how to design composite columns—a hollow structural section (HSS) with a reinforced concrete core. These provisions were followed when designing the Luxenbourg project.
As a result of the non-resistant attributes of composite structures, the fireproofing trade was eliminated from the project which led to significant cost and time savings.
Innovation 3: Reducing the floor-to-floor height by using flush beam assemblies
The Luxenbourg project, like most new construction in urban areas, was subject to a height restriction imposed by the municipality. To maximize the number of floors in the building, a flush beam combination was selected in lieu of a conventional steel or precast beam system. The shallow trapezoidal composite beams and hollow-core slab assembly allowed spans of approximately 11 x 8 m (36 x 26 ft) with a total depth of only 300 mm (12 in.). If wide flange steel beams would have been used to support the prefabricated concrete slabs, the beam would need to be 400 mm (16 in.) deep for a total floor assembly of 700 mm (28 in.).
Having beams that did not protrude under the slab also gave the design team complete flexibility for the interior layout. After finishing the first phase of the Luxenbourg project, the developer realized the units with smaller total floor area were easier to rent. Therefore, in the second phase of the project they decided to have 11 apartment units per floor instead of 10. Since the structural system requires few interior columns (six in a floor plate of over 1200 m²) the only change to the structure was the addition of one cantilever balcony on a perimeter pre-stressed slab. All the columns remained in their original location which facilitated the co-ordination with the parking on the level below.
Innovation 4: Designing cantilever precast balconies without a thermal bridge
One of the biggest structural challenges in residential construction is designing cantilever balconies without a thermal bridge. Since the slab is partially inside and partially outside, eliminating heat loss through the concrete and reinforcement is challenging.