Precast concrete solutions for risk management
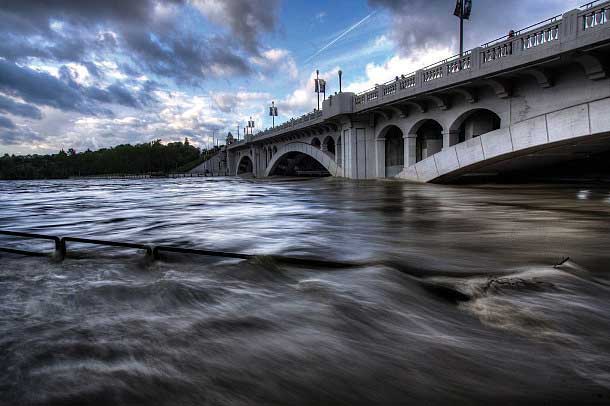
Photo © Ryan Quan
Design for resilience
A town or city featuring stronger, better built buildings, and roads and services to support them is truly resilient. Its leadership recognizes the value of planning for potential disasters and has taken steps to ensure the community has the ability to survive such events with less loss of housing, employment, and critical services. Resilient building materials like concrete and other products can play a vital role in creating stronger and safer communities.
There are various ways to incorporate precast concrete to make projects more durable and disaster-resistant. Precast concrete underground products, wall, floor, and roof systems, along with bridges, offer an unsurpassed combination of structural strength and resistance against wind and blast forces. Builders, architects, and designers have come to recognize more durable underground infrastructure, public buildings, residences, and businesses, often built with precast concrete, resist damage from natural and manmade disasters and can greatly reduce the impact the built environment has on the planet.
These built-to-last communities begin with comprehensive planning, including stricter building codes producing robust structures with long service lives. More durable buildings with high-performance features help promote community continuity, making cities and towns stronger, and better able to successfully weather any challenge.
The residents of more robust cities and towns experience major benefits from the overall improvement of building resilience. These range from fewer burdens on local services and a more stable local economy providing consistent sources of money to run the municipality to a more enduring legacy for future generations.
Conclusion
Climate change is getting attention from decision-makers and citizens around the world. Recent natural disasters and their devastating impacts on communities and the global economy have heightened everyone’s concern. Building resilient and durable structures are becoming more important than ever as we try to adapt to new and extreme changes in weather patterns.
Communities that are being proactive and effectively planning ahead will be in a better position to build stronger, safer buildings and see the long-term benefits. Precast concrete is a reliable building material that can help communities become more resilient to natural and manmade disasters. We need to act now to build a stronger tomorrow.
WHY CERTIFICATION IS IMPORTANT TO RESILIENT CONSTRUCTION |
Infrastructure resilience has become a primary objective for governments and national security organizations over the past decade. Recent initiatives have focused on resilient building design, and one approach under consideration is a voluntary certification program for commercial and residential buildings.
There are three credits in the new Leadership in Energy and Environmental Design (LEED) v4 program centred on resilient design. In a nutshell, these three credits are designed to ensure a design team is aware of vulnerabilities and addresses the most significant risks in the project design, including functionality of the building in the event of long-term interruptions in power or heating after human-caused and natural disasters. The intent of these types of programs is to encourage the adoption of resilient design practices in construction and planning of the buildings. Stringent certification programs like that of the Canadian Precast/Prestressed Concrete Institute (CPCI) can help in ensuring quality assurance of these projects. The CPCI certification program was developed, and is continually updated, by a team representing all industry stakeholders. Further, the program is backed by CPCI’s network of committees, research and development, education, codes and standards initiatives, and integrated programs and relations throughout the industry. The program ensures each plant has developed and documented an in-depth, in-house quality system based on time-tested, national industry standards. To become ‘CPCI Certified,’ plants must demonstrate they have appropriate experience and training in manufacturing precast concrete, have quality systems and procedures in place, and be committed to quality throughout the organization. Each plant is required to develop a site-specific quality systems manual (QSM) that defines in detail how its operations work; this is then reviewed and approved by CPCI. After the QSM is completed, an initial unannounced audit takes place. On passing its first audit, a plant is certified. Twice annually, certified plants undergo a thorough, unannounced two-day audit conducted by third-party engineers who follow criteria specifically targeted to the products being manufactured at that location. Quality assurance ensures certified plants produce materials that are durable and can help ensure a long lifespan of structures and buildings. Additionally, when quality products are used in projects, they are more resilient and have the ability to withstand some of the harsh climate conditions expected in the future. CPCI Certified plants are audited in accordance with standards published in the requirements of CAN/CSA-A23.4-16, Precast Concrete−Materials and Construction, including Annexes A and B, together with:
How to specify CPCI certification
The following language can be helpful in specifying CPCI precast plant certification: Precast concrete manufacturers to be certified to Canadian Precast/Prestressed Concrete Institute (CPCI) Plant Certification Program in [Architectural Precast Concrete Products, A1,] [Subcategory AT], [Precast and Prestressed Bridge Products, B,] [Subcategory] [B1] [BA1] [B2] [BA2] [B3] [BA3] [B4] [BA4] [Commercial Precast and Prestressed Concrete Products (Structural), C,] [Subcategory] [C1] [CA1] [C2] [CA2] [C3] [CA3] [C4] [CA4] [Precast Concrete Drainage Products, D,] [Subcategory] [D1] [Standard Products, S] prior to the time of bid. Only precast elements fabricated under the CPCI plant certification program to be acceptable, and plant certification is to be maintained for the duration of fabrication, [erection,] and until warranty expires. Precast fabrication to meet the requirements of CAN/CSA-A23.4-16, including Annexes A and B, together with PCI MNL-116 and 117 and CPCI certification requirements. |
Brian J. Hall, BBA, MBA, is the managing director of the Canadian Precast/Prestressed Concrete Institute (CPCI), the vice-chair of the Royal Architectural Institute of Canada Foundation, and a board member of the Athena Sustainable Materials Institute. In 1998, Hall joined CPCI as its national marketing director. He is one of the authors of the institute’s sustainability strategy, which includes the development of the CPCI Precast Concrete Life Cycle Assessment, the Sustainable Plant Program, and the CPCI North American Environmental Product Declaration for precast concrete. Hall can be reached via e-mail at brianhall@cpci.ca.