Polished concrete’s warring state
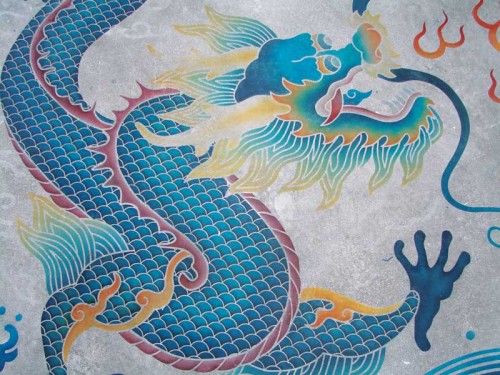
Photo courtesy Colour
The not-so-great wall of grit
Another attempt to communicate design intent and perhaps keep Division 09 products out of Division 03 is to specify by grit. A spec might read something like this:
Use one of these three liquid-applied products a._____, b._____, c._____, and finish to an 800 grit finish.
In order for this to be quantifiable, and for this method to be repeatable from one floor to another and one project to the next, ‘800 grit’ cannot be variable. However, this is not the case. Many manufacturers will suggest a grit range for achieving a specified gloss reading. This is because an individual manufacturer can produce a variety of different abrasive tools within a specific grit category. In other words, a company could offer multiple types of abrasive tools varying in size, shape, and matrix material (all with different scratch patterns), and yet still designate them with an identical grit number. It should be taken into account there are at least 2000 suppliers of abrasive tools and the problem only compounds.
In doing this, a situation is created in which different types of floor finish legally become ‘the same’ in your construction documents. Your bids will reflect this with some contractors bidding fully refined floors and some bidding cheaper sealed or coated floors that wear off in a year. Grit is too variable to define your design intent clearly.
Surface texture grade and roughness average
In modern Chinese, one reads from left to right, but in ancient Chinese the reader had to read from right to left (and from top to bottom). This article will now follow suit, turning the conversation around to look at things from a new point of view. What if we did not specify by the tools doing the work, but rather on what was actually happening to the floor? Do not measure the tool, measure the floor. Specification writers do not really care what shape, size, or grit the tool is as long as the result is the durable, sustainable floor.
It is also important to understand how the ideas of surface texture grade (STG) and roughness average (Ra) relate to measuring the surface of the concrete slab and creating quantifiable language. A few years ago, the Concrete Sawing & Drilling Association (CSDA) published ST 115, Measuring Concrete Micro-surface Texture. Its purpose was to provide a uniform language for measuring concrete surfaces for their surface texture value, and then employing those values to communicate design intent. By using contact instruments and understanding surface texture grades, one can obtain a quantitative measure of the concrete surface profile and understand how texture characteristics of the concrete surface influence floor performance in regards to gloss, friction, and sustainability.
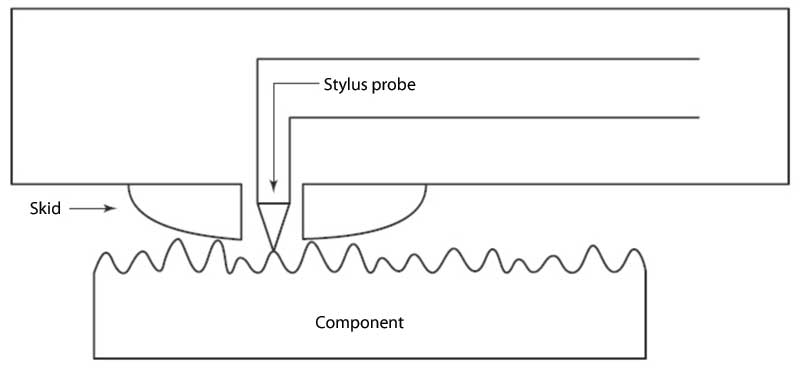
Image courtesy Concrete Sawing & Drilling Association
The roughness average is the parameter used as the basis of CSDA ST 115 and specifications quantifying refinement by STG. The association’s executive director, Patrick O’Brien, points out Ra has been used in the steel industry for decades. Measured in micrometers (μm) in most parts of the world and micro inches (μin) in the United States, it employs a device called a profilometer to use a stylus to trace the profile of the floor to determine the average roughness and STG, identifying the physical level of refinement on the floor’s surface.
When you need the floor to have a matte finish, you can specify the floor be refined to .76 μm. If the client needs more of a semi-gloss refinement, then it can be close to .41 μm; if the project demands a glossy finish, then .15 μm is called out. There is no need for the contractor, project manager, and owner representative to debate whether an object is easily identifiable in a floor or if just the right amount of crispness has finally been realized. In a very simple manner, we can tell to what degree the profile has been mechanically refined as well as keep out the barbarian hordes from Division 09. Robinson said a quantifiable standard like CSDA ST 115 “makes for a really happy specifier.”
Conclusion
Simply specifying by micrometers will not solve all problems. Skilled and certified contractor craftsmen will still be the difference between good and great, and communicating design intent with all relevant parties (e.g. concrete supplier, placement/finishing contractor, general contractor, polishing sub, etc.) is critical. Still, at least there is now a common language with which to build Grand Canals and Great Walls. We have been dealing with “Warring States Language” in our concrete specifications for long enough. It is time to unify and to simplify so everyone can be on the same page of the story—the happy ending is truly sustainable floors and satisfied clients.
Christopher Bennett is a project manager and specification writer at Tao Group, a construction-consulting firm dedicated to achieving quantifiable and repeatable results. He previously worked with specifications and product management at Husqvarna Construction Products. Prior to his career in building, Bennett served as a Mandarin Chinese crypto-linguist on active duty for the United States Navy. He can be reached at christopher.bennett@taogroup.co.