Plaza Deck Restoration: Principles of drainage and waterproofing
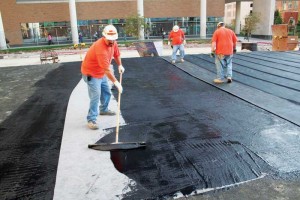
Fluid-applied membranes
Hot-applied rubberized asphalt systems are typically installed at a 5.5-mm (215-mil) thickness, often reinforced with polyester scrim. This installation requires two fluid applications of the membrane, which minimizes pinholing and thin spots in the membrane. Cold-applied liquid membranes are typically installed at a minimum 1.5-mm (60-mil) thickness over a concrete substrate by spray, squeegee, roller, or brush per guidelines by the membrane manufacturer.
ASTM C 836, Standard Specification for High Solids Content, Cold Liquid-applied Elastomeric Waterproofing Membrane for Use with Separate Wearing Course, is a performance specification describing the required properties and test methods for cold-applied, elastomeric-type waterproofing membranes for both one- and two-component systems. Common types of cold fluid membranes include polymer-modified asphalt, asphalt-modified polyether, and single- and two-component polyurethanes.
The advantage of adhered membrane systems is the decreased potential for leaks to migrate under the membrane. The disadvantage is the need for meticulous surface preparation of the substrate, which must be dry, with a lightly broomed texture, and contamination free––including free of the initial waterproofing membrane. Liquid-applied membranes should never be used to fill or level substrate surface irregularities. Moisture is the adversary of these systems. Moisture in the substrate can cause pinholing, blistering, and entrained air bubbles in the membrane. Unsuitable curing agents, form release agents, and other contamination (e.g. dust) can inhibit adhesion. Some manufacturers claim these products are sufficiently elastic to bridge cracks, but typically this requires additional strips of reinforcing material.
The objective with a fluid-applied membrane is to achieve a good bond to the substrate without blistering or pinholes. To that end, a simple patch test (i.e. applying the waterproofing membrane to a small area) may provide the best site-specific results. In the case of hot fluid-applied membranes, this may be the most practical method. However, for chemical and moisture-curing membranes that take longer to set, this may not provide a practical solution for evaluating substrate moisture conditions.
Modified bitumen and bentonite sheets
Another material used for plaza decks is modified bitumen (mod-bit) sheets, often called ‘peel-and-stick’ or ‘rubberized asphalt.’ These are made of asphalt modified with polymers and a high-density polyethylene (HDPE) film backing. The sheets can be applied as a single-ply or multi-ply waterproofing system. When installed as a multi-ply, the overlying membrane course is typically oriented perpendicular to the prior course to maintain seam separation; but no matter the installation, the sheet lap orientation should consider the drainage slope so the membrane laps shed water.
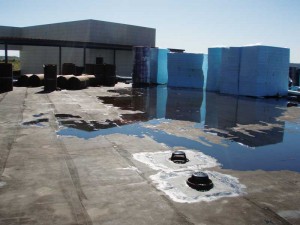
Modified bitumen sheets require a substrate primer and are fully adhered to the concrete substrate. They are sensitive to site conditions, moisture, and deck surface quality, and must be protected from ultraviolet (UV) exposure within a few weeks of installation. These sheets are generally not as preferred for a plaza deck application as fluid-applied or welded-single-ply due to the potential for leaking at membrane overlaps.
There are several sheet membrane composites made of sodium bentonite and a polyethylene liner. The sheet is installed with the bentonite side down directly against the concrete deck with the polyethylene liner facing up and sealed with seam tape. These sheets address the potential for leaking at the membrane overlaps by the bentonite activating and stopping the water ingress. Bentonite composite sheets require full confinement from the wearing course assembly and, therefore, should not be used with paver-on-pedestal systems.
Single-ply thermoplastic systems
Single-ply thermoplastic systems are another good choice for plaza deck waterproofing. General types include polyvinyl chloride (PVC), ethylene propylene diene monomer (EPDM), and butyl rubber membranes. Butyl rubber sheets have an advantage over EPDM sheets because of their lower moisture absorption––a property more important for a waterproofing membrane than EPDM’s greater resistance to UV exposure. PVC sheets are typically reinforced and offer high puncture resistance combined with fused, heat-welded seams. PVC sheets are either loose-laid or fully adhered to the substrate. When loose-laid, they can be compartmentalized by first adhering a grid strip to the concrete substrate and then welding the sheet to the grid. Typical grid size is 3 m (10 ft) square. The advantage of the grid system is it acts like a waterstop that limits water migration under the loose sheet if a leak occurs. The disadvantage is it is expensive and requires additional substrate preparation.
In lieu of a grid, there are PVC membrane composites with a separate polymer layer that also prohibits water migration if the vinyl sheet is damaged. These membranes are installed with the polymer layer directly against the substrate to react and stop water ingress if water circumvents the welded thermoplastic sheet. In this orientation, the polymer layer also functions as a separator sheet with regard to substrate surface contamination (which allows less substrate preparation) and functions as a protective cushion for the thermoplastic sheet against any puncture from an irregular substrate texture.
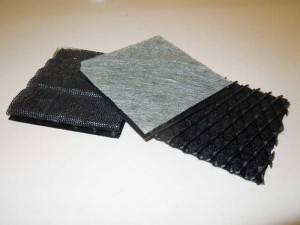
Like a fluid-applied membrane, the installation of a fully adhered thermoplastic membrane requires substantial substrate preparation. Typically, loose-laid single-ply systems are a good choice for areas where there are sensitivities to odours, volatile organic compounds (VOCs), and fumes generated during installation of chemically cured or hot-applied systems. A big advantage of PVC and EPDM single-ply systems is either the membrane or an accessory sheet can be used as an exposed flashing if required in the restoration design.
Multi-membrane system
The ultimate restoration of plaza waterproofing may include more than one membrane system to provide redundancy barrier performance. For example, restoration of the waterproofing may include a loose-laid and seam-welded PVC thermoplastic membrane installed overlaying a fully adhered fluid-applied membrane. Additionally, there are PVC membranes with a hydrophilic polymer layer that provides self-sealing properties for even yet a third functional layer of stopping water ingress. This polymer layer also provides a separation between the PVC and any asphalt materials for material compatibility.
Multi-membrane installations provide performance features and advantages not available in a single system. The designer must verify the materials are compatible with each other and surrounding building components. Finally, if a multi-membrane system is chosen, it is best to have both membranes provided by the same manufacturer for a single-source warranty.
Protection course
A protection course over the plaza deck waterproofing membrane should be installed immediately after the membrane and quality assurance testing (i.e. flood-testing or low-voltage mapping) is completed. If the protection course installation is delayed, damage to the waterproofing membrane can occur during subsequent construction operations.
A membrane is worthless after it is damaged. That is why it is important to inspect the membrane to ensure the protection board is installed immediately after the testing is completed. If the membrane fails the testing, the protection course should not be installed until the membrane is repaired and retested.