Pipe rehabilitation for plumbing and bathrooms
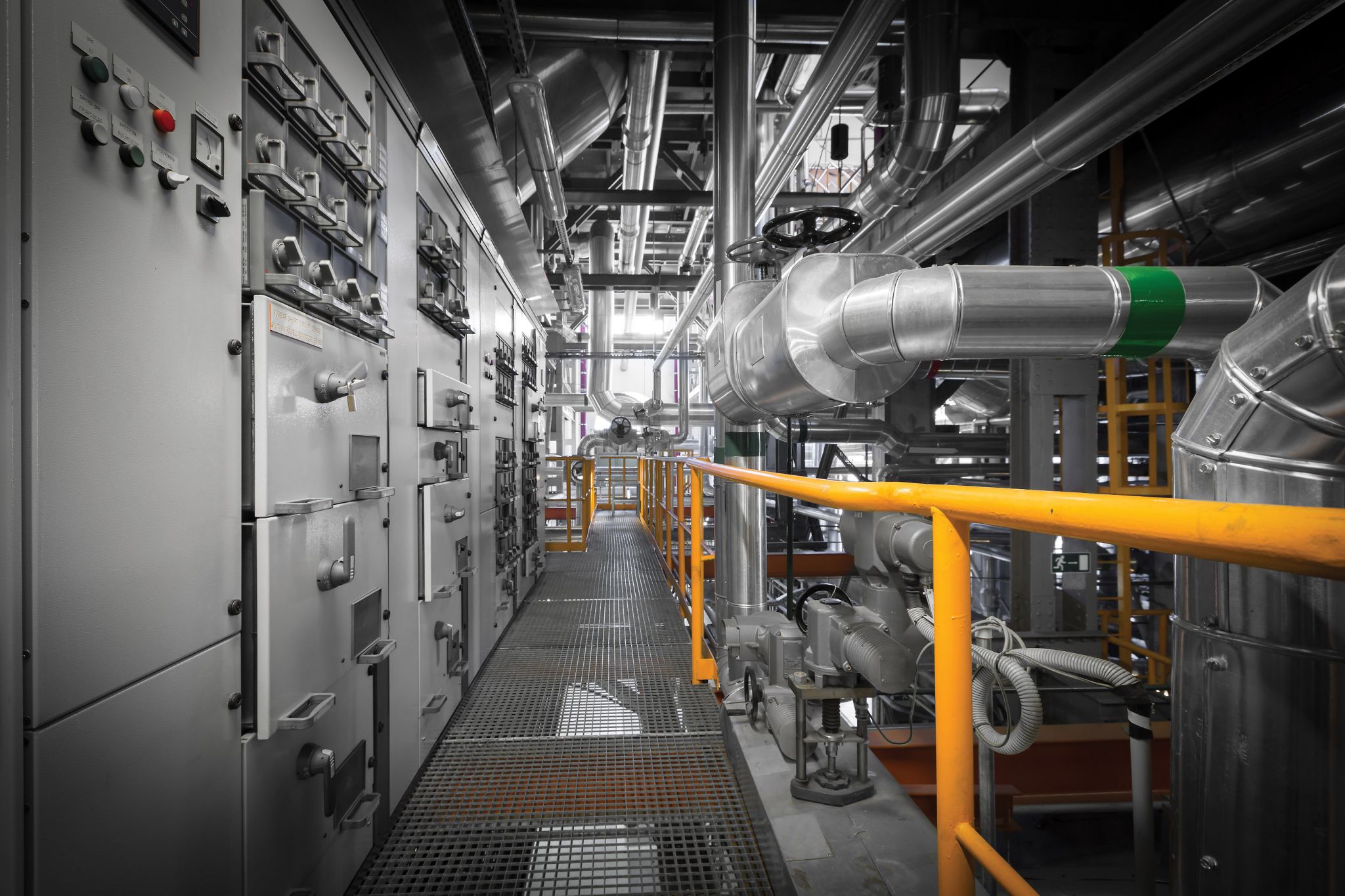
By Alyscia Sutch
Cost-effectiveness, working time, flow efficiency, and sustainability are all important concerns when considering the right fix for damaged piping systems. However, during the planning process, it is best to take an inside look at the system to see the root of the problem, the options available, and how to prevent the likelihood of a reoccurring issue.
When considering water piping in homes, market data surveys by the Canadian Copper & Brass Development Association (CCBDA) and Copper Development Association (CDA) state their namesake material is the predominant one selected for domestic water service and distribution in residential construction. The copper pipes running through homes and buildings are projected to last 20 to 25 years.1 At that point, there can be a high risk of tiny pinhead-sized holes (known as ‘pinhole leaks’) that slowly drip water; these can go undetected for months, causing a lot of damage if the problem is not fixed. Traditional repair options that tear out finished walls and ceilings to remove and replace domestic water systems can be long-term solutions, but also a painful and intrusive experience for homeowners or building management.
Additionally, most homes built before the 1970s have sewer lines composed of cast iron and clay. The most common problem in these lines is cracking at the joints and the bottom of the pipe rusting out—this can ultimately be a failure itself or lead to root intrusion. Root intrusion is one of the most destructive and costly problems property owners can face when maintaining their sewer drainage system. Tree roots can travel a great distance, even around concrete slabs, and penetrate pipes in a bid to access water. This problem is reported to cause half of all sewer blockages. Traditional care for root intrusion involves simply hiring someone to dig up and replace the pipe. Not only is this rarely a long-term fix, but it also requires removal and replacement of finished landscapes and slab to address the problem.
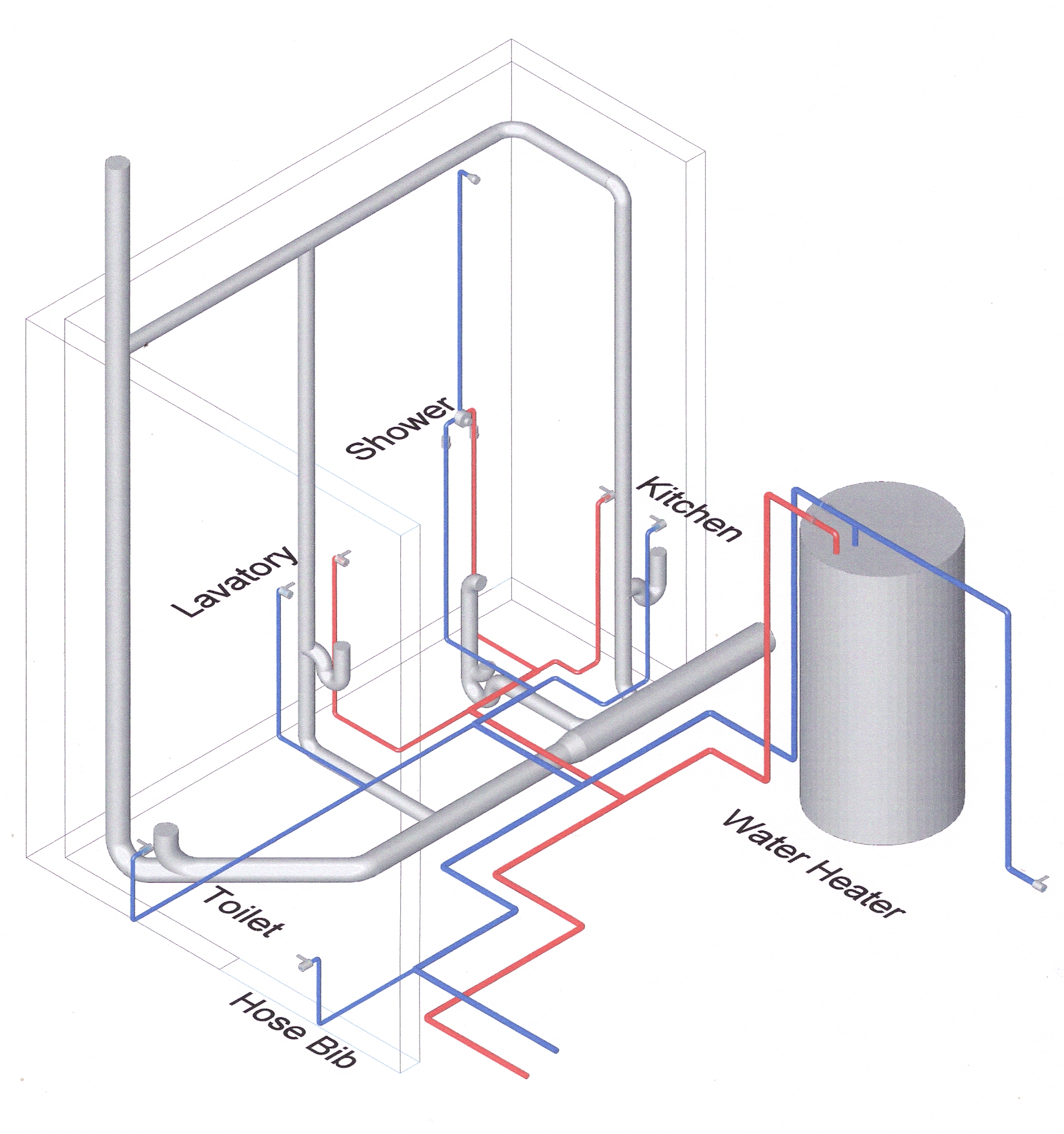
Today, one of the most effective solutions for failing pipe systems both inside and outside of buildings is in-place pipe lining. This includes barrier coatings for pressurized systems and structural liners for non-pressurized systems—both with a life expectancy of greater than 50 years.
An easier way?
A property’s pipe systems are often forgotten about until there is an obvious problem, such as pinholes, corrosion, low flow, or blockages. Like most objects, pipe systems age, and require maintenance to operate efficiently. The traditional process to dig up and replace pipes has more disadvantages than benefits. The disadvantages include:
● system downtime;
● removal of finished landscapes or building interior; and
● displacement of residents while work is performed, removal of fill and existing system and the replacement of fill and finishing.
Additionally, many contractors run into the issue that the new landscape or hardscape is not finished exactly like it was before.
With pipe rehabilitation using structural liners, roots can be removed and a new liner saturated in epoxy can be pulled into place, creating a structurally sound pipe within the existing pipe by using existing access points. Typically, this can be completed in less time, with less cost, and requiring less resources than traditional replacementPulled or pushed into the pipe systems without destruction, the liners can protect the pipes from many types of common failures, including debris buildup, corrosion, leaks, and root intrusion. The liner prevents roots from intruding the pipe because the new liner acts as a seamless, strong, structural pipe. Additionally, there is no longer a worry for corrosion and buildup because the new pipe is now a hardened epoxy.
The liner can decrease the inside-pipe diameter, but the industry uses the Hazen-Williams co-efficient of friction equation—this relates to the flow of a substance in correlation with the surrounding pipe’s physical properties, and the pressure drop or gain caused by the internal surface of the pipes friction (Figure 1).
Structural lining process
The history of structural lining began in Europe during the mid-1970s, reaching the Canadian and U.S. municipal sectors the following decade. By the late 1990s, small-diameter specialists and applications were making it possible to rehabilitate pipe sizes applicable for residential homes (i.e. 50 to 100-mm [2 to 4-in.]).
The project begins with mapping the internal plumbing system and camera inspection of drain and sewer lines. Thanks to recent technology advances, there are techniques and equipment for detecting challenges such as leaks, deterioration, and corrosion without draining and/or taking the system out of service.
A plan is implemented to minimize disruption and afford the most efficient timeline for work completion. Depending on the lining method to be used, pipes may be drained. After testing for leaks, the pipes are prepared for cleaning.
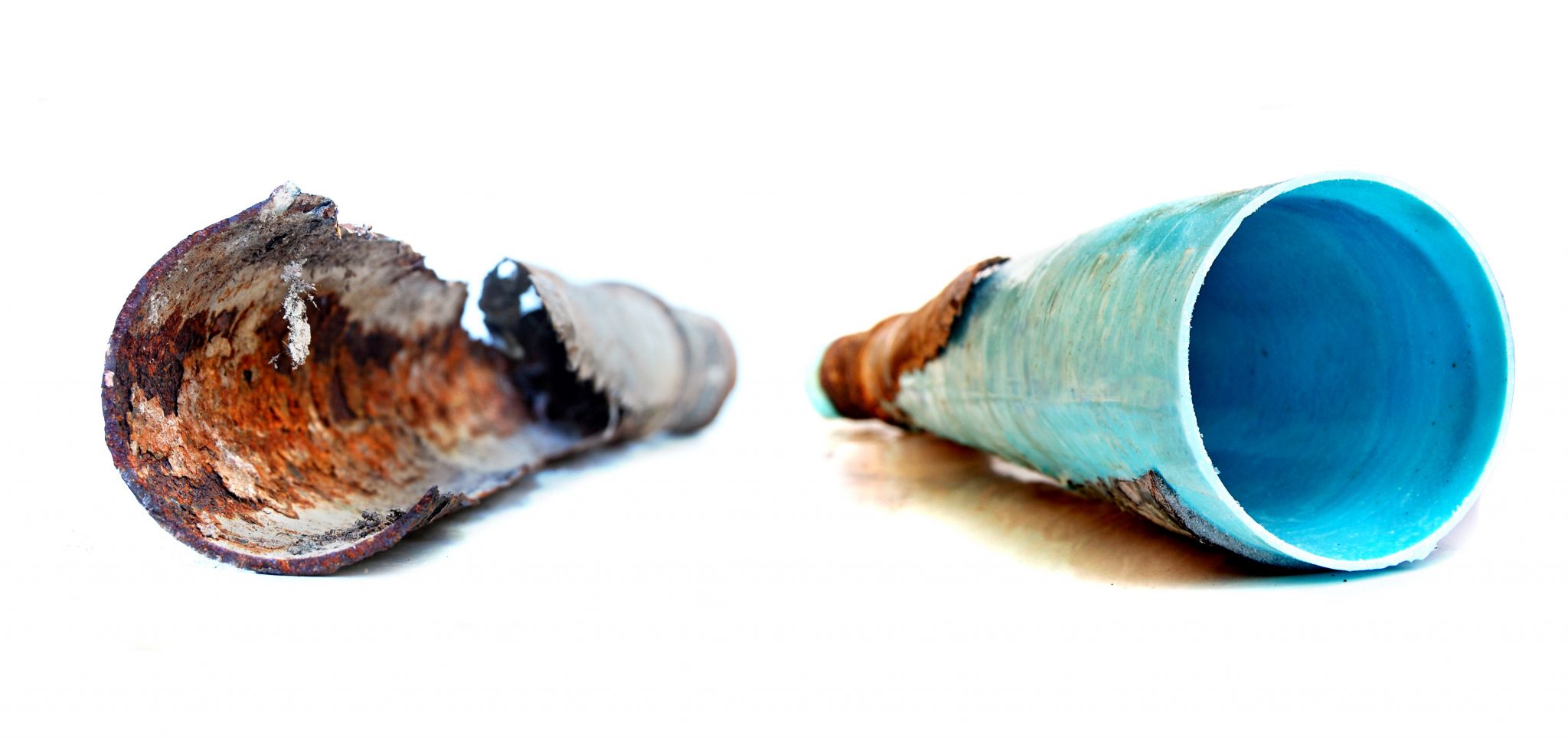
The next step involves the cleaning and reinstitution of the original pipe diameter. This includes removal of calcite, tuberculation (i.e. small mounds of corrosion products), roots, and broken pipe fragments. Such removal methods may include high-pressure water-jetting, or pneumatic or electric specialty tools designed and calibrated to remove the debris and to re-establish the original inside-pipe diameter without damaging the material’s structure or integrity. Cast pipe may require additional preparation when there is significant corrosion or missing sections of pipe. Existing upstream and downstream access points are utilized to pull an epoxy-saturated felt liner or section repair into the host pipe. Full coverage of branches and Ts in the system can also be implemented.
This method provides the ability to line multiple 45- and 90-degree angles, as well as the option of lining specific sections of pipe without involving the entire length. Once completed, a final leak test and camera inspection is performed to ensure the system is now a smooth, joint-less pipe within the existing host.
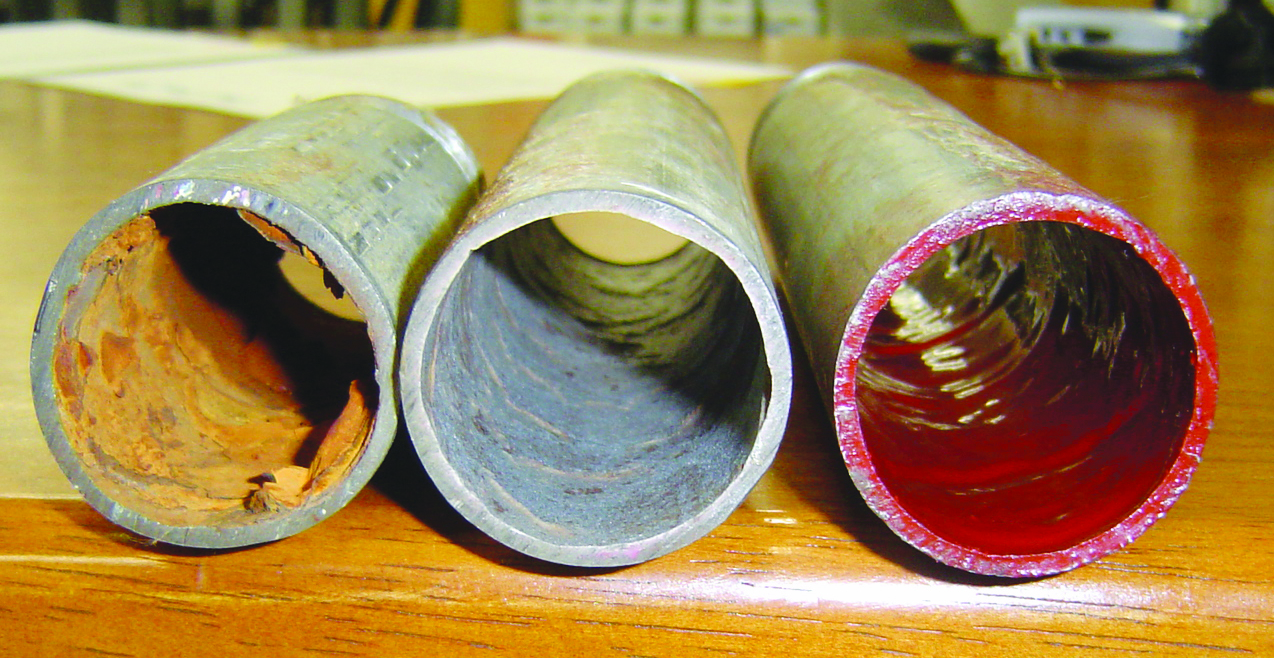
Drain lines and potable water lines are not the only systems being rehabilitated—the technology is also available to retrofit vertical applications, roof drains, and mechanical systems, including fire suppression, air, gas, and HVAC systems. Barrier coating technology with epoxy coatings creates a protective separation between carried contents flowing through and the metals within the pipes themselves—this helps safeguard against decomposition or even copper/lead leaching into drinking water. The epoxy coating used to line potable lines has received many certifications and approvals—the design professional should check to see what is needed for the project.
One of the most important parts of the epoxy-coating process is the preparation where an abrasive material is blown through the system to achieve an anchor-tooth profile allowing the proper cohesion of epoxy barrier coating resin to the host pipe.
When dealing with valves plumbed in the system, they will often be removed before coating so full operation of the mechanical device can still be achieved. While the process is non-invasive, parts of the work may require small conventional repairs or replacement of such mechanical devices (if desired to keep operational).
History of epoxy coatings
Trenchless pipe lining technologies are not new—some of the methodologies have been used for decades, passing the test of time. For example, starting in the late 1980s, all U.S. Navy’s aircraft carriers’ collection, hold, and transfer pipe systems have been lined with blown-in epoxy barrier coating. The coatings were developed to meet the demands of each application that had differing conditions and environments—an epoxy could be applied to the interior of the pipes in-place. This included maintaining pipes at required temperatures for optimal in-place cleaning and coating.
These lining solutions have since grown to include applications in the private and domestic piping markets that faced aging potable water systems and poor water quality in all types of residential, commercial, industrial, federal, and municipal properties. For blown-in epoxy coatings for pressurized systems, the velocity is also calculated with the Hazen-Williams equation. Although the diameter of the pipe may be slightly reduced because of the coating on the pipe walls, the process can in fact provide a better flow rate (Figure 2). Metallic piping systems build layers of tuberculation, scale, lime, and rust buildup over time, diminishing the inside diameter and causing a loss of flow.
Heathgate Condominium
With available alternatives to traditional pipe replacement that are also nondestructive, many homeowners, property managers, engineers, and municipalities are turning to trenchless pipe lining to rehabilitate pipe systems. Several plumbing and mechanical companies are now offering these pipe rehabilitation products across Canada and abroad.
The owner of Toronto’s Heathgate Condominiums was spending up to $60,000 annually in pinhole leak repairs, which prompted the managers to look for an alternative option. Chemicals used to treat drinking water had slowly eroded the pipes, resulting in multiple pinhole leaks. Inevitable leaks formed throughout the system about once per week in the 58-suite condominium property since its creation in 1989.
The management company for Heathgate chose epoxy coatings to line the entire 18-year-old potable piping system, which included mains, vertical risers, and horizontal branches; it also incorporated a hot water recirculation system.
“The owners were very pleased with the process and the professionalism of crews. They especially appreciated not having to endure the breaking of their walls or any significant disturbance to their daily lives while the work was carried out,” explained Robert L. Weinberg, president of property management company, Percel.
Notes
1 For more, see “Causes and Prevention of Pitting Corrosion in Copper Plumbing Systems in the USA,” by W.S. Lyman et al. The paper was presented in the Proceedings of the International Symposium on Corrosion of Copper and Copper Alloys in Buildings, presented in March 1982 in Tokyo. (back to top)
Alyscia Sutch is the marketing co-ordinator for Nu Flow Technologies licensing and manufacturing facility. She has a degree in public relations, and has worked in the construction and rehabilitation industry for seven years. Sutch works closely with construction, plumbing, and mechanical companies who license pipe-lining technologies. She can be contacted via e-mail at asutch@nuflowtech.com.
To read about the pipe rehabilitation process, click here.