Passive House goes to work
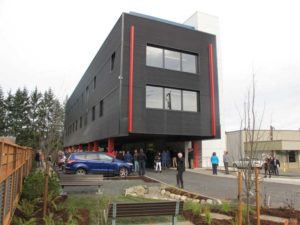
Further, columns could not interrupt the drive aisle, and zoning setback requirements only allowed enough space for a row of columns on the west side, which could not interrupt access to the parking stalls—a structural challenge in a seismically active area. Hence, it was determined to create three masses. A long, skinny block extending the full height of the four-storey building does most of the seismic heavy lifting, relying on thick, tightly spaced shear walls. The electrical and plumbing services fit within this block, as well as washrooms, elevators, and fire exits.
The main office space is a two-storey block spanning over the drive aisle, providing flexible open offices with the option of being subdivided using temporary partitions for privacy. A stairway in the middle of this block acts as a connecting element, enabling casual conversations in mid-transit. It also doubles as bleacher seating for gatherings of 60 to 70 people. The final, smaller mass on the fourth level houses a multipurpose space for training events and holiday parties and an executive hospitality suite.
Thermal boundary
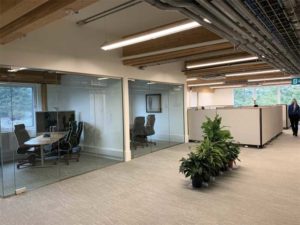
In conjunction with developing the massing, the design team also had to determine another PH criteria—thermal boundary. A decision was made to exclude the ground floor, exit stairs, and elevator from the heated envelope. This improved the form factor and avoided thermal bridging and airtightness challenges, any of which could have resulted in missing the required performance targets.
Structure
The building’s geometry presented challenges for seismic design in a high-risk zone. An asymmetric load path and the narrow width available to transfer shear forces to the foundation led to significant forces acting on certain members and connections. This scenario would normally suggest the use of steel or concrete. However, these materials would have resulted in significant thermal bridging challenges—a key consideration for energy performance and the Passive House standard. This influenced the design decision to use cross-laminated timber (CLT) for shear walls and floor diaphragms as a structural solution that could handle the high loads while minimizing the framing’s impact on thermal bridging because of its significantly lower thermal conductivity compared to concrete or steel.
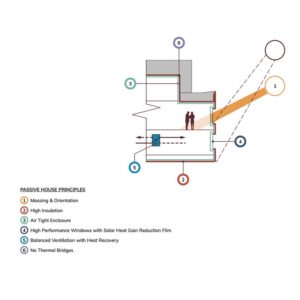
Additionally, glue-laminated (glulam) timber beams were utilized to handle long spans. Glulam columns were used to support larger point loads, and prefabricated light wood framing was employed where forces were less demanding. The result is a unique hybrid structural system. Wood also provides a biophilic element to the interiors, as the structure is left exposed wherever practical.
Nearly a hundred, unique high-force connections required an intensive design process including the creation of a detailed 3D model of the entire building. The detailed digital model was used as part of the computer numerical control (CNC) fabrication process.
Envelope and sequencing
Only a limited number of local trades have Passive House experience or training, and none of them on a building of this type. Since proper execution of the envelope is essential to achieving a high-performance building, care and attention was given to construction sequencing. The project team determined a simplification of sub-trade scopes would allow for co-ordination and sequencing without the need for every trade to be familiar with PH principals. This was achieved by creating a three-layer system for the exterior walls, each associated with work for a particular sub-contractor: structure, thermal and air barrier, and cladding.