Panelized and composite stone masonry
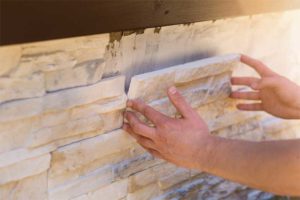
Photo © Shutterstock/Ronstik
Without the need for mortar, composite stone options are cold-weather-ready for installation. Panelized stone veneer (without mortar) also does not require heat for installation for the same reason. Both products do not need a rainscreen unlike stone and stone veneers using mortar, but require a WRB.
Moisture mitigation
For any type of masonry project, the prevention and mitigation of moisture is essential for controlling mould, mildew, and structural damage. Moisture abatement best practices include:
- flashing;
- counter flashing;
- weeps;
- vents;
- sealants;
- water repellents;
- post-applied surface treatments;
- vapour retarders;
- crack control measures; and
- a program of surface protection, internal protection, and drainage and drying.
Additionally, the Building Enclosure Moisture Management Institute (BEMMI) of Winnipeg, Man., recommends any region receiving more than 500 mm (20 in.) of annual rainfall should incorporate enhanced drainage techniques into the wall system, especially if using an absorptive cladding material. Areas receiving 1016 mm (40 in.) or more of rainfall should utilize a weather barrier or rainscreen design, regardless of cladding material. The geographic orientation of the wall, amount of roof overhang, altitude, and even nearby trees can impact the level of water intrusion expected and how likely it is to dry. In many places, new and evolving building codes are driving the need for better moisture management solutions. For example, Canada’s wetter coastal provinces now require, per the National Building Code of Canada (NBC), wall assemblies to be built with capillary breaks between WRB and the exterior veneer.
Mortar formulations for cold weather construction can also be used to manage moisture. Adding water-repellents on the jobsite is generally considered the best method. To help reduce the effects of freeze/thaw conditions, a polymeric admixture can be used to increase adherence.
Drainage is another important consideration in moisture management. Several products now include built-in weep holes or backchannel drainage systems. Manufactured panelized stone veneer systems with built-in clips are designed to create a weep channel behind the stones for drainage. However, they still may be susceptible to efflorescence (a chalky substance created by surfacing salt) and even mould and mildew contained in the rough, porous surface of the stones, which can be difficult to clean.
Composite stone has the advantage of being impervious to moisture and efflorescence, while being highly resistant to mould. In extremely damp conditions, mould will grow on any surface. If this occurs, composite stone can be cleaned off with detergents and a hose. Designed weep holes and drainage channels are included to keep water away from the wall and allow proper ventilation.
Skilled labour issues in Canada
Along with lengthy installation times, the skilled labour shortage continues in the Canadian building industry. Even with ongoing economic growth, there is a huge shortage of skilled labour in the country, notably skilled masons—who are so few and far between in many provinces—that home builders are resorting to exclude masonry or brick in building plans. This illuminates the critical need for alternative, easily obtainable products that can be installed with less skilled labour at a faster pace.
Currently, the Canadian construction industry shows overall contractors simply cannot get the job done without qualified workers.
Even with ebbs and flows in growth, the construction industry needs to recruit, train, and retain an estimated 300,000 new workers over the next decade. According to a BuildForce Canada study, hiring needs will be driven predominantly by the expected retirement of more than 260,000 construction workers, or 22 per cent of the current labour force, forcing many in the industry to take a long look at employee engagement and recruitment.
On a national level, Canada is reaching out to immigrants as a skilled labour solution, with the Canadian Federal Skilled Trades Program (FSTP) offering qualified people the opportunity to become a permanent resident in an attempt to ensure the country attracts and retains a skilled workforce.
When it is impossible to employ natural stone, alternatives may be the solution to achieve the desired esthetics. Current skilled labour shortages underscore the need to find readily available, easily shipped products any contractor can install. The North American building industry is poised to respond with easier panelized and composite systems to solve a host of jobsite, performance, and labour issues.
Ralph Bruno is CEO of Derby Building Products Inc., the Québec City-based manufacturer of exterior cladding products, including shake and composite stone. A veteran of the building materials industry, Bruno was instrumental in leading the conversion from traditional materials to composites. He can be reached at rbruno@derbybp.com.