Panelized and composite stone masonry
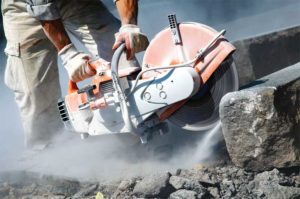
Photo © Shutterstock
Types of masonry products
There are many types of masonry products available in the market.
Stone
Natural stone requires a high level of skilled labour and mortar layers/grout. Building professionals must consider several factors when installing stone such as:
- gypsum layer, batt, and wood frame;
- dry times for mortar scratch coats and inspections;
- weep screens and screeds required for drainage;
- moisture is a consideration requiring engineering behind the wall;
- cold weather mitigation is needed for installation;
- shipping weight and stocking ability; and
- safety precautions at heights.
Stone veneer (with mortar)
Stone veneer also requires skilled labour. When using stone veneer in building projects, design professionals must take into account the following:
- esthetics resemble natural stone;
- easier to mix and achieve custom colours than natural stone;
- more than half the cost of natural stone;
- gypsum layer, batt, and wood frame;
- several mortar layers, metal lath, and two water barriers;
- weep screens and screeds required;
- application of grout, dry time, and excess removal;
- moisture sensitive due to cementitious material; and
- safety precautions needed at heights.
Stone veneer (without mortar)
Stone veneer systems without mortar are primarily installed with a clip system, or with a hanging mechanical fastening method. Other aspects include:
- gypsum layer, batt, and wood frame;
- attachment of wire system and screw to wood frame;
- similar in cost to stone veneer;
- stones/small panels installed individually;
- integrated weep channel between panel and wall;
- stones can vary in size and colour (installer needs to create random pattern);
- look for carcinogenicity warnings (ventilation equipment must be worn when cutting); and
- unlikely to come loose and fall (wire is integrated into the mould woven through middle of stone).
Composite stone
Lighter weight composite stone in cladding panels cover 0.5 m2 (5 sf) per panel, and offer faster wall coverage than other methods. Other features include:
- gypsum layer, batt, and wood-frame—it is recommended to apply a weather-resistive barrier (WRB) and starter strip at bottom of wall;
- offers dry stacked or grouted look;
- uses colourants and grit textures to achieve stone-like look and feel;
- single installation with interlocking panels that are mechanically fastened;
- a fraction of the cost of real stone or stone veneer;
- panels are designed to vary in colour so each will look different;
- no skilled masonry required, and any contractor can install with standard siding tools;
- no mortar, grout, or heavy equipment as well as no dry times or mid-job inspections;
- CCOHS compliant—meets silica dust requirements (no silica); and
- no risk of loose or falling stones.
Cold weather issues
When ambient temperatures drop below 4 C (40 F), cold weather construction methods for masonry must be applied to ensure structural strength and also proper moisture management. The Canadian Standards Association CAN/CSA A371-14, Masonry Construction for Buildings, and American Concrete Institute (ACI) 530.1-08/American Society of Civil Engineers (ASCE) 6-08/the Masonry Society (TMS) 602-08, The Specification for Masonry Structures, outline requirements for masonry construction in winter. During cold weather construction, water requirements in mortar are reduced to reach the desired consistency as too much liquid may freeze and cause a disruptive expansion. Additionally, the initial and final sets of mortar are significantly delayed, and strength rates are reduced.
Masons have developed a variety of strategies to mitigate issues associated with cold weather construction. Masonry materials optimized for cold performance, such as high-strength mortars and those with well-graded sands, are ideal as they require less water. Admixtures like cement accelerators can provide builders with increased rates of early stage strength development. However, such admixtures may only be used if previously specified. Only non-chloride-based accelerators are allowed by ACI 530.1-08/ASCE 6-08/TMS 602-08, as chloride contributes to corrosion of embedded metal structures.
Additionally, masons may protect building materials by wrapping them in canvas or tarps to deter moisture and contaminants. In some instances, a temporary, heated, enclosed work area may be raised at the jobsite to prevent contamination and mitigate severe weather. Moreover, some masonry materials like sand and water can be warmed with heating pads, steam heating systems, or fire. Although a combination of cold weather tactics can be employed, these circuitous methods can prove costly and time consuming.