Overcladding masonry facades: Additional practical insights
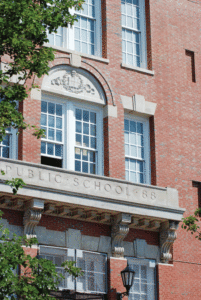
By Albert Aronov, AIA
The March 2023 issue of Construction Canada included an article from the author on the topic of overcladding as a solution for owners of commercial, institutional, and government buildings that are structurally composed of masonry and beginning to show the impacts of age, weather, neglect, and deferred maintenance on the enclosure. This is a follow-up article speaking to additional questions in this system type. The topics to be addressed in this article, with respect to overcladding of masonry facades and foundations, as well as roof assemblies, include the following:
- Placement and attachment of insulation and air barrier within the assembly.
- Considerations for the use of exterior insulation and finish system (EIFS) overclad solutions.
- Structural considerations, including thermal bridging and construction costs.
- The appropriateness of face-sealed systems in certain climate regions.
- Questions regarding air barriers.
The essential role of air barriers in the overcladding assembly
One premise of the original article is that the bearing walls of many government and school buildings across North America, built in the last century with solid masonry, are now experiencing moisture intrusion. These areas of leakage and incursion are leading to severe degradation and damage to brickwork, window openings, and interior assemblies with plaster and other finishes. As an alternative to removing and replacing the original masonry—an approach that can negatively impact structural integrity—project teams and architects are encouraged to design an insulated facade layer with vapour barrier, creating a new enclosure that is watertight and energy efficient, and possibly more attractive. This raises a question about how to ensure the ideal placement and attachment of the insulation, air barrier, and cladding.
The project case studies in the original article were school buildings built in the early part of the 20th century with masonry, and particularly brick and brick veneer. The approach employed for these structures has been intended to accomplish restoration and renovation using a face brick system that would improve the enclosure performance while retaining the original esthetic in some measure. In these cases, the new face brick overcladding was applied directly to the existing load-bearing masonry (after any needed repairs) without adding any layers of insulation between. The technique includes parging the original masonry to create a smooth surface for application of a fluid-applied vapour-permeable barrier, with a mini-cavity and drainage mat for moisture to escape. This approach results in a waterproof, breathable, and attractive facade.
For projects in cold climates using a rainscreen system instead of a face-sealed solution—whether fibre cement, metal panels, terra cotta, or siding—insulation is essential and must be continuous to be most effective. The International Energy Conservation Code (IECC) adopted a requirement of continuous insulation (ci) in the building enclosure in 2012 because of its effectiveness in increasing thermal resistance of a wall. Experts such as John R.S. Edgar, president of the EIFS Council of Canada, emphasized the placement of ci “outbound of the studs,” adding:
Canadian code-writers have taken note—the National Energy Code for Buildings’ (NECB’s) focus has shifted to the building envelope’s passive performance, limiting reliance on powered mechanical systems in the alternative path options.1
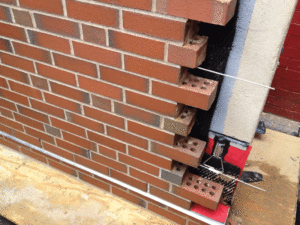
Many dew point calculations in rigorous building science studies have proven that walls with no insulation between studs and using only exterior ci are fully protected from air leakage condensation during cold weather, as long as the ci is installed on exterior side of the vapour barrier. The reverse—heavy interior insulation and little or none outside—lead to condensation occurring on the inside, and the potential for mould and rot with the attendant structural deterioration and occupant health risks. For overcladding scenarios, rainscreen systems provide the best opportunity for including ci.
Important air barrier considerations
The purpose of an air barrier is to stop airflow or resist air pressure within the enclosure (or between conditioned and unconditioned spaces), in order to control the flow of heat and moisture. As such, any air barrier must be continuous and durable, with all transitions and penetrations carefully sealed. Unchecked air movement creates both moisture management problems and thermal performance issues, since air carries moisture and water vapour as well as heat, or lack of it.