Options for preventative roof maintenance
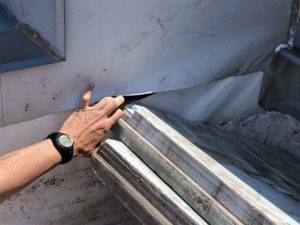
Visual reviews
The simplest and the most effective approach to preventative maintenance is to undertake a visual review of the roof. Using checklists, a professional walks on the roof and visually reviews the various components of the assembly. For example, many of the issues mentioned earlier can be easily identified during a visual review. Walking the roof enables consultants to ‘detect’ soft spots, an indication of deteriorated or moisture-laden components.
Some key items that would be covered in a visual review include:
- interior signs of roof problems, such as leaks, cold spots, stains, etc.;
- drainage restrictions when checking for accumulated dirt and debris at drains and scuppers;
- signs of damage or weathering of the roof membrane;
- gaps and tears of expansion joints;
- vent stacks, skylights, exhaust fans, new equipment additions, etc.;
- rooftop structures such as guardrails, access ladders, hatches, davits, tie backs, and chimneys;
- sealant deterioration; and
- membrane and metal flashings.
Thermographic roof imaging
In the author’s opinion, the most common, non-intrusive investigation is thermal imaging. It can be used to detect both air leakage in the building envelope and thermal anomalies across the wall and roof assemblies. Depending on the location, thermographic roof scanning is conducted between late spring and late fall. A proper scan requires a cloudless day/night with little or no wind, dry surfaces, and daylight heating. Winds beyond 10 km/h (6 mph) will speed up the cooling of the roof and distort the cooling patterns. Standing water also poses another limitation. Additionally, exhaust fans and other equipment incorporating B-vents/chimneys will have to be turned off, as it may provide alternative thermal signatures that are unrelated to moisture.
In fundamental terms, the process involves the natural (sun) heating up of the roof assembly, and as the roof cools, areas of greater thermal mass (i.e. wet insulation) will retain heat longer than dry regions. The infrared (IR) camera measures and records the temperature differences of various objects on the roof by reading the emitted heat energy—hotter areas appear brighter with more vivid colouring than cooler zones.
Thermography works on built-up roof (BUR) systems where the insulation is ‘sandwiched’ between the deck and the roof membrane. It is also suitable for conventional modified-bitumen (mod-bit) membranes and fully adhered single-ply membranes such as ethylene propylene diene monomer (EPDM). Thermographic scanning of polyvinyl chloride (PVC) and thermoplastic olefin (TPO) roofs can be challenging, and require special attention due to the inherent sensitivity of light-coloured membranes.
Thermal imaging does have some limitations, as it cannot be performed on:
- built-up ballasted assemblies where large 25 to 38-mm (1 to 1 ½-in.) stones are used to hold the membrane in place, as the stones may retain the moisture within the aggregate, and may act as a ‘heat sink’ by absorbing the sun’s thermal radiation, thereby distorting the results;
- loose-laid membranes, as the layer of air between the underside of the membrane and insulating layer may distort imaging;
- inverted roofing systems where the membrane is sandwiched between the roof deck and the insulation; and
- metal roofs, primarily due to the reflectivity of the panels.
Thermographic scans can only be performed at night. It should be undertaken by people who are properly trained to use the equipment, interpret the onscreen images, and on safety issues. It is advisable to send two people to the site—one to use the equipment and another to record, mark the roof, and act as a safety spotter. A thermographic roof scan can only identify thermal anomalies. The presence of moisture within the assembly will have to be confirmed with a moisture probe or cut tests.