Optimizing cold weather concreting practices
By Alicia Hearns
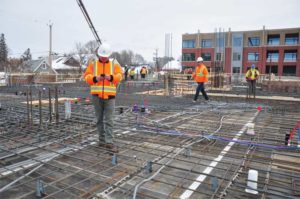
For many construction companies, the time of the year is approaching when dropping temperatures play a massive role in day-to-day site operations, especially where concrete is being employed. Concrete temperature monitoring becomes more critical in cold weather as low temperatures decrease the rate of strength development affecting the durability of the structure. For this reason, accurate and consistent temperature readings of concrete elements are important so that the quality of the structure is optimized.
Understanding heat of hydration
The heat produced by concrete during curing is characterized by an exothermic reaction called heat of hydration. After this initial reaction, the rate of hydration significantly slows down. At this time, fresh concrete is usually transported and placed. The concrete then enters the dormant phase where it has not yet hardened and is workable. Due to this, the length of the dormant period depends on multiple factors, including cement type, additives such as accelerators and retarders, and additions like fly ash and slag. The amount of heat produced during hydration is largely related to the volume, composition, and fineness of the cement.
The end of this phase is characterized by the initial set where strength gain begins. As the concrete hardens, the heat generated during this phase can last for multiple hours. The temperature of the in-situ concrete then begins to stabilize, and the hydration process slows down. It is extremely important to control the temperature of concrete during the dormant and setting phases.
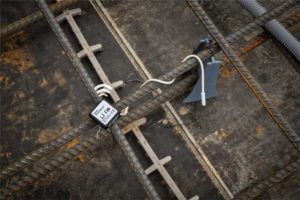
Importance of temperature monitoring in cold weather
The hydration process can be drastically impacted if freshly placed concrete is exposed to temperatures that are too high or too low, compromising strength development. Therefore, the American Concrete Institute (ACI) has provided specific guidelines that outline an allowable temperature range for each pour. This range depends on the element size and ambient conditions (ACI 207, Guide to Mass Concrete, 301, Specifications for Structural Concrete, and 306, Guide to Cold Weather Concreting).
Guidelines for pouring concrete in cold weather can be found in ACI 306. ‘Cold weather’ is defined as three or more consecutive days of low temperatures, specifically ambient temperatures below 4 C (40 F) and air temperatures below 10 C (50 F) for more than any 12-hour period. To ensure proper strength development in these ambient conditions, some placement specifications include:
- concrete temperatures must be maintained higher than 4 C for 48 hours after a pour;
- all concrete surfaces must be protected within the first 24 hours after being placed to prevent freeze damage; and
- concrete temperature cannot reach freezing levels before reaching a specific strength (3.5 MPa [500 psi]) or the overall structure will have a reduced strength.
Controlling concrete curing conditions in cold weather
To ensure concrete elements are curing properly in cold weather, different techniques are used to maintain high temperatures and consistent strength gain. One technique includes the use of insulation blankets. These protective blankets cover the concrete to distribute the heat generated during the hydration process. This helps maintain consistent temperatures throughout the concrete element. The same can also be achieved using external heating systems.
The rate of strength gain can also be increased by using a mix with a lower slump (less water), adding hot water to the mix, and using additives to accelerate curing and lower the concrete’s setting time. Moreover, reducing the time between mixing and placing the concrete can minimize a drop in temperature.
Another approach for controlling heat generation is to select a specific concrete mix design for cold weather conditions. For example, type III cement can generate more heat than types I and II. Further, using finer cement will generate more heat. Similarly, using supplementary cementitious materials (SCMs), such as slag or fly ash, will reduce the amount of reactive materials in the early stages and, therefore, the amount of heat generated.
Why does it matter?
As mentioned earlier, if the ambient temperature is too low, the hydration of the cement will slow down or stop altogether until the temperature increases. As a result, there will be a considerable reduction or an end to the strength development of the concrete element. Hence, it is important to understand these guidelines and how concrete performs during cold weather so temperature and curing conditions can be controlled easily.