Optimizing cold weather concreting practices
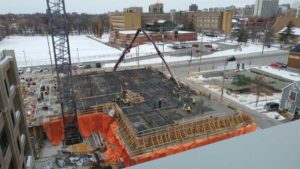
As destructive testing techniques, the drilled core and cast-in-place cylinder methods need third-party labs to perform break tests to get the data. As a result, more time is needed in the project schedule when using either of these methods.
The maturity method
The maturity method, per ASTM C1074, Standard Practice for Estimating Concrete Strength by the Maturity Method, is based on the principle that concrete strength is directly related to its hydration temperature history. Though this methodology has been used since the 1970s, it has only recently gained popularity on jobsites with the use of wireless sensors. The method is defined as “a technique for estimating concrete strength that is based on the assumption that samples of a given concrete mix attain equal strengths if they attain equal values of the maturity index.” In other words, maturity is a value that represents the progression of concrete curing. As a result, a mix calibration is required to implement this technique in the project.
The goal of the calibration is to determine a relationship between maturity and strength for a specific mix. A maturity calibration only needs to be completed once for a specific mix and its properties. This maturity-strength relationship is developed in the lab, using cylinder break tests, and then correlated to the strength of the in-place concrete on the jobsite. Though it may seem daunting, the maturity calibration can be done in the following five easy steps:
- Make a minimum of 17 cylinders—two for temperature monitoring and the rest of the specimens for testing compressive strength breaks. All cylinders must be cured together in a moist environment according to ASTM C511, Standard Specification for Mixing Rooms, Moist Cabinets, Moist Rooms, and Water Storage Tanks Used in the Testing of Hydraulic Cements and Concretes.
- Select a minimum of five break times. For example one, three, seven, 14, and 28 days. For each day, obtain the compressive strength of two cylinders. It is advisable to break a third cylinder if the results vary more than 10 per cent from the average. It is also important to note the time of the breaks.
- At the time of the breaks, it is critical to obtain data from the two cylinders that were used for temperature monitoring and make an average of these values. Input these values into either the Nurse-Saul Equation or the Arrhenius Method according to ASTM C1074 to obtain a maturity value.
- At this point, there will be a set of at least five data points each with a strength associated to a maturity value. Plotting the data points allows one to obtain a curve with a logarithm equation. The formula for calculating the maturity of concrete is: Strength=a+b LOG (maturity).
- It is important to validate the calibration curve by making a couple of additional cylinders on the next pour. Compare the calculated strength obtained from the maturity calculation to the compressive strength that was achieved in the lab. A difference of up to 10 per cent is acceptable.
As a non-destructive testing technique, concrete maturity allows one to estimate the early age and compressive strength of in-place concrete. This is done using a sensor. Wireless sensors are placed within the concrete formwork and secured on the rebar before pouring. The goal of these sensors is to measure the temperature of the slab in real-time and correlate this data to the concrete’s strength based on the mix’s maturity calibration. A physical connection to the sensor is not needed to obtain this information. Instead, data is uploaded to any smart device within an app using a wireless connection where it is updated every 15 minutes.
Data collected by these sensors is considered more accurate and reliable as they are fully embedded in the formwork, meaning they are subject to the same curing conditions as the in-situ concrete element. Equipped with real-time results, contractors can improve the heating process, decrease energy costs, and save time in their project schedule by knowing when to move on to subsequent construction operations, such as formwork removal or post-tensioning.
The main limitation of wireless sensors is the maximum allowable distance between the sensor and the surface of the concrete. Since concrete can block wireless signals, the sensors usually need to be placed within a certain distance from the surface to ensure connectivity.
Selecting the method of strength testing
Monitoring the temperature and strength of the concrete during cold weather becomes much more difficult as a result of ambient conditions and the need for extra equipment onsite to monitor the in-situ elements. The decision in choosing a testing method may simply come down to what the individual knows and is used to. However, the accuracy of these tests, and the time they take to obtain strength data, are significant factors that must be taken into consideration. When pouring concrete in cold weather, the technique chosen not only determines how easy it will be to obtain strength values, but also play a part in whether the project will stay on schedule. This method will also ensure the strength, quality, and durability of the structure is optimized.
Alicia Hearns is a content marketing specialist with Giatec Scientific Inc., a global company providing smart concrete testing technologies and real-time data collection. She can be reached via e-mail at alicia.hearns@giatec.ca.