Optimizing cold weather concreting practices
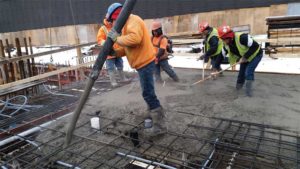
Furthermore, in mass concrete elements, if proper techniques are not used to control the temperature, thermal cracking can occur. This happens when the core temperature of the element is very high due to the mass effect, while the surface temperature is lower because of ambient conditions. In these cases, the temperature differential between the core and the surface is too large, resulting in tensile stress in the concrete. If the tensile stresses outrange the tensile strength of the concrete, cracking will occur.
Cracking reduces concrete’s durability by increasing the permeability of the structure and making it easier for water, air, and chloride to penetrate the material. This can result in rebar corrosion and, in severe cases, reduce the durability and integrity of the entire concrete structure. Therefore, it is essential to monitor concrete mix, ambient temperature, and differential temperature and to adjust curing techniques appropriately to avoid thermal cracking.
Five common mistakes to avoid during cold weather concreting
To ensure proper strength gain and maintain control of the temperature of in-situ elements, it is important to keep these methods in mind when pouring concrete in cold weather. It is also advisable to familiarize oneself with these five common mistakes.
Pouring concrete on frozen ground
If concrete is poured on frozen ground, it increases the risk of cracking. This happens as the fresh concrete closest to the ground continues to cure slower than the surface. Additionally, frozen ground can settle when thawed, causing the concrete to crack.
Allowing concrete to freeze
Concrete should be kept warm, around 10 C (50 F), to cure properly. Fresh concrete can freeze at –4 C (25 F), so it is important to keep it warm until it has reached the specified strength targets.
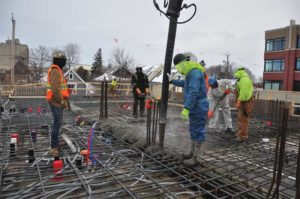
Using cold tools
It is equally important to keep the tools and building materials warm. If forms or tools are too cold, it could alter the concrete coming into contact with them.
Sealing concrete when it is too cold
Concrete sealers make the material more resistant to weather exposure and other outside elements. If concrete is being placed in cold weather, it is advised to get a sealer that works well in extreme weather conditions. Sealing typically should not be done if the temperature is below 10 C.
Misjudging daylight
During colder months, the amount of daylight lessens. It is essential to use time wisely as daylight not only gives more light, making work easier, it also results in warmer temperatures.
Measuring concrete temperature and strength in cold weather
The most common method for monitoring the strength of in-situ concrete is the use of field-cured cylinders. This practice has remained generally unchanged since the early 19th century. The samples are casted and cured according to ASTM C31, Standard Practice for Making and Curing Concrete Test Specimens in the Field, and tested for compressive strength by a third-party lab at various ages. Usually, if the slab has reached 75 per cent of its designed strength, engineers will give the ‘go ahead’ to their team to move on to the next steps in the construction process.
However, when pouring in cold weather, ACI 306 specifically recommends not using this method as field-cured cylinders “can cause confusion and unnecessary delays in construction.” This is largely because it makes it difficult to maintain the cylinders in the same conditions as the in-situ concrete. It is, therefore, recommended that other in-place testing methods, or maturity testing, be used for monitoring concrete strength. When these methods are correlated to standard-cured cylinders, they can be used to determine the concrete strength accurately. Below are some examples of in-place testing methods.
Rebound hammer or Schmidt hammer
This is covered in ASTM C805, Standard Test Method for Rebound Number of Hardened Concrete. A spring release mechanism is used to activate a hammer which impacts a plunger to drive into the surface of the concrete. The rebound distance from the hammer to the surface of the concrete is given a value from 10 to 100. This measurement is then correlated to the concrete’s strength.
Pros
It is relatively easy to use and can be done directly onsite.
Cons
A pre-calibration using cored samples is required for accurate measurements. Test results can be skewed by surface conditions and the presence of large aggregates or rebar below the testing location.