Opening the door to visual communication
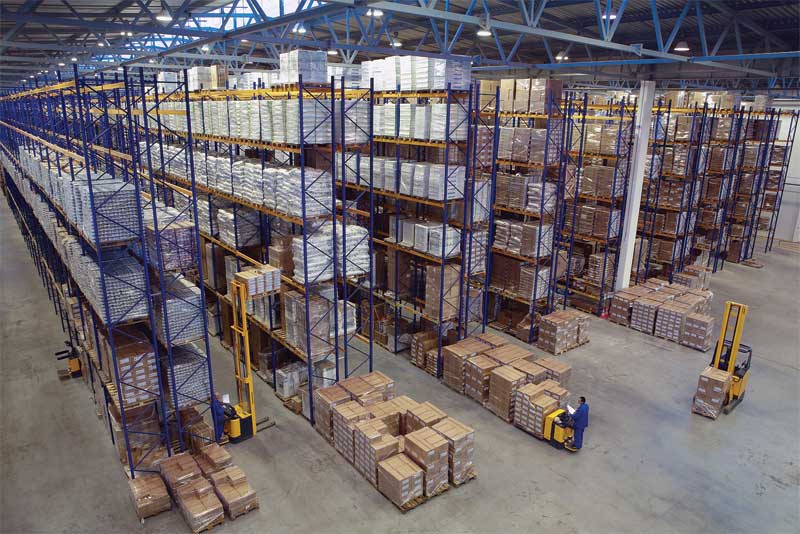
Photo © BigstockPhoto
For forklift operators, there is a balancing act—safety regulations and protocols encourage them to operate with caution, while production goals push them to work as quickly as possible. It is the operator’s responsibility to make the right decisions. This is why operator training is mandatory.
Even the best-trained forklift operators must deal with certain realities. Approaching a closed door is one of them. Other common challenges include:
- unexpected entry—when workers on foot or another forklift might be using the same door;
- open staging areas—when areas in front of doors allow unrestricted movement of forklifts, as well as workers who are on foot;
- difficulty hearing—when wearing hearing protection can impede a worker’s ability to hear audible devices or sense where the sound is coming from;
- stopping requirements—when a forklift moving at 16 km/h (10 mph) may take 12 m (40 ft) to stop (studies have shown that a panic stop takes
0.2 m/km/h [1.3 ft/mph]); and - floor conditions—when slippery or wet floors make it more difficult to stop.
Light communication improves safety
The blind spots created by closed doors represent a danger not too dissimilar from blind spots created at loading docks. Vision can be severely hindered inside a trailer, where forklift drivers are essentially operating inside a tunnel. This creates a dangerous blind spot for the operator until the forklift has fully backed out of the trailer. Likewise, the inability to see a forklift inside a trailer is concerning to other forklift operators. This problem becomes exacerbated when a trailer is approached from the side and a forklift is operating at the front end of the trailer.
Simple light communication technology began appearing in loading docks across North America in response to these dangers. Now, vehicle restraint signaling systems contribute to a safe loading dock environment with an easily understood red light/green light system to indicate when a trailer is secured at the loading dock. The newest communications technologies use advanced systems to further enhance the safety of trailer loading and unloading. For example lights around the corners of the dock doors provide clear communication of the restraint status directly in the forklift driver’s line of sight.
This technology also offers lights at the rear of the leveller to confirm the status of the dock lock to the forklift operator inside of the trailer where there is the most risk. Located within the leveler, these light communication systems effectively mirror the red/green status of the control box, providing forklift drivers and other nearby personnel with another level of protection against catastrophic accidents.
Light-emitting diodes (LEDs) in the upper corners of the interior dock doorframe provide a quick ‘status-at-a-glance’ view for forklift operators so they know if the trailer is locked and safe to enter. It makes them more confident when entering a trailer, while lights on the leveller make them more confident while inside the trailer. In both cases, this makes operators more productive.
Similar types of light communication systems are migrating to the inside of facilities, especially where blind spots like doors exist.
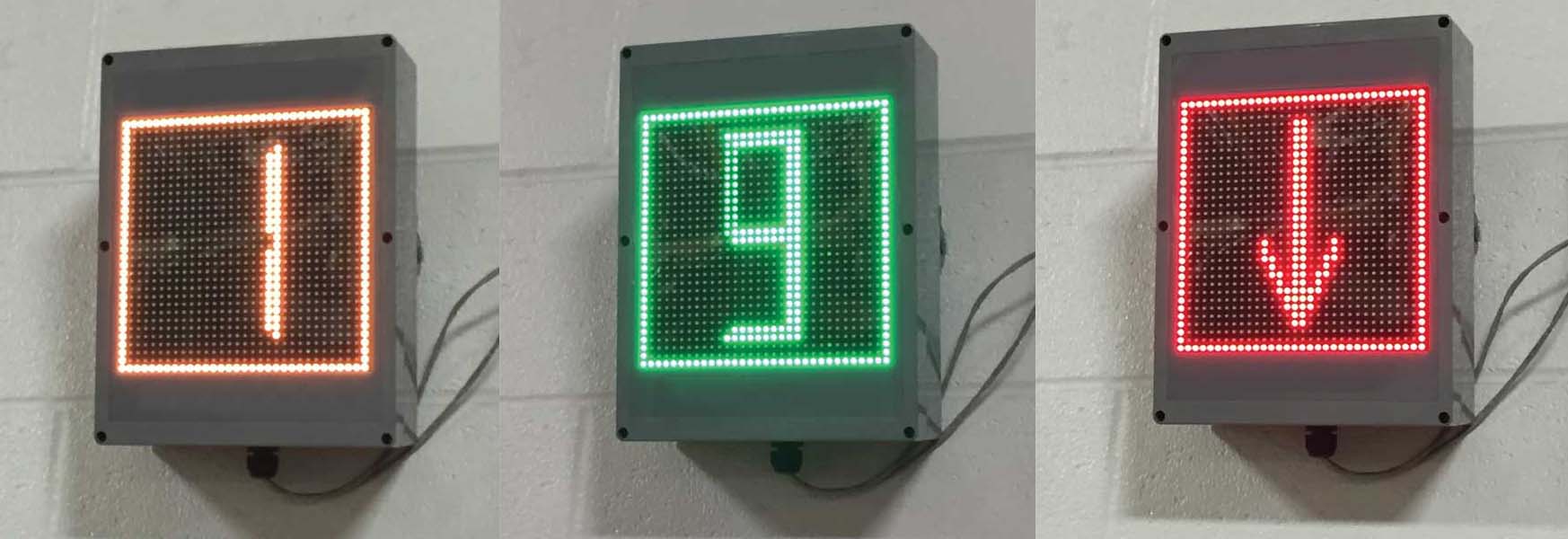