Offsite versus onsite construction
Reduced timeline
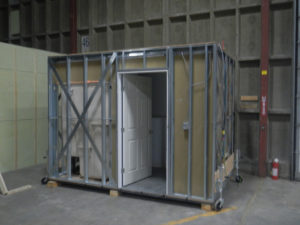
The greatest benefit to a construction site is the project schedule is dramatically reduced using prefabricated methods. Developing a property requires a large sum of money to either be tied up or financed. Reducing the build time not only reduces the overall cost of capital required for a project, but also ensures the building is ready for occupancy sooner, turning typical cost into revenue sooner than traditional construction may be able to deliver.
Since in-situ construction requires the assembly and erection to be completed onsite, the general contractor (GC) must deal with a very congested and inefficient space where trades are trying to share resources, workspace, access, parking, and supervision. This burden takes energy away from the GC and causes distraction and inefficiency. The drastic reduction in people and overlapping trades instantly reduces the cost of supervision, while simultaneously increasing the quality of time a supervisor or foreman spends onsite.
The ability to observe the construction of a wall panel or bathroom modular system in a factory weeks before it is needed onsite provides GCs and building owners schedule certainty. While traditional methods require labour to be present and productive onsite every day, the productivity cannot be measured until the end of the day. This creates a reactionary wave if production is not as fast as planned. With offsite construction, production can be properly forecasted days or weeks in advance, giving project managers time to manage their schedule.
In Canada, the construction, renovation, and demolition sectors account for 27 per cent of the solid waste produced. As the world becomes more educated and concerned with sustainable building practices, efficient buildings, and waste reduction, prefabrication offers a solution to address these trends. In the design phase, prefabricated methods can assist architects and designers to plan waste out of the project. A report published by the Waste Reduction Action Programme (WRAP) suggests offsite manufacturing processes can help the construction industry reduce waste by up to 90 per cent.
There is no question the construction industry is trending toward offsite methods. The key for Canada is to catch up to the rest of the world, particularly China and the United Kingdom, and educate themselves on the risks, downsides, benefits, and limitations of available premanufactured solutions.
Factors affecting cost, risk, and schedule when it comes to prefabricated building methods that must be considered and weighed by all stakeholders include:
- project financing;
- occupancy date;
- onsite waste disposal;
- heating/hoarding;
- safety railings;
- site congestion; and
- use of site resources (e.g. material lift and crane).
For a building to realize all the above considerations, stakeholders must collaborate early enough in the conceptual and design development stages to allow prefabrication to provide its many benefits. Careful planning before a project commences is critical to ensuring the benefits of offsite construction are realized. This requires engaging the owner, contractor(s), design team, and sub-trades earlier than required to collaborate on the front-end of a project to reduce change orders, snags, scope gap, or overlaps in the end.
In most circumstances, the construction procurement methods allowing for prefabricated solutions to be implemented easier are design-builds (DB), integrated project delivery (IPD), private-public partnerships (P3), and construction management (CM). This does not mean other methods are not to be considered, but it becomes much more difficult to implement offsite solutions if the provider is not included at the start of the design phase.
Overall, as previously mentioned, offsite manufacturing products and solutions are becoming more prevalent in the construction industry, and collectively as an industry, it takes an open mind to accept change.
Keith Tilley is the director of business development at Mod Panel Manufacturing. He has been working in the subcontractor field for 10 years. Tilley is an active member of the Edmonton Construction Association (ECA) and YBG in Edmonton. He has an MBA from the University of Alberta. Tilley can be reached at keith.tilley@mod-panel.com.
David Kennedy, MBA, P.L.(Eng.) LEED AP LEED AP, is director of engineering at Mod Panel Manufacturing. He is responsible for overseeing the engineering department for new and conceptual designs including building envelope solutions, modular pods, and volumetric steel/wood boxes. Kennedy has more than eighteen years of experience in the design of building mechanical and control systems. He can be reached at david.kennedy@mod-panel.com.