Noise And New Developments: Sounding off on Ontario’s residential requirements
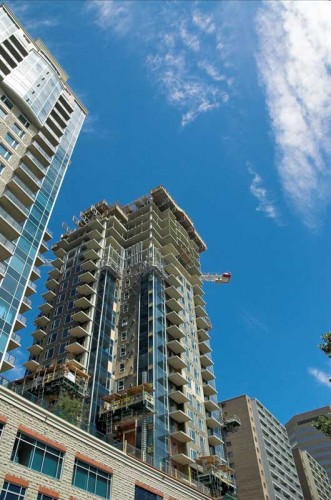
By Ryan Bessey, P.Eng.
Basic acoustic requirements have long been part of the National Building Code of Canada (NBC), which is the model for the provincial codes, including the Ontario Building Code (OBC). The only demand is walls surrounding residential suites must be documented to meet a specific sound isolation performance. The limitation of this requirement is actual field sound isolation performance can vary greatly from the documented value due to various factors.
To address the sound isolation issue (along with other acoustic concerns) for Ontario, the Tarion Warranty Corp., which issues warranties on the province’s residential construction, has stepped in. It now compels developers to prove their new condominiums meet specific acoustic standards before being enrolled under the Ontario New Home Warranty Program. These new requirements are catching many developers off-guard in a booming condominium market.
In its recently revised Builder Bulletin 19R (July 1, 2010), Tarion has added ‘acoustics’ to the list of identified risk areas that must be considered before a condominium development can be enrolled in its new home warranty program. In other words, after the building’s design is complete, but before construction can proceed, a design certificate must be prepared by an acoustical engineer for review.
The simplest and most efficient method for certification is to have the acoustical engineer involved in the design of the project from the beginning. Otherwise, a detailed acoustic review must be conducted at the end of the design phase and if any issues are discovered, aspects of the building may require re-design. This can wreak havoc with schedules and project costs.
In the case of one Toronto condo tower, while the high-value penthouse suite offered a sweeping skyline view, analysis of the plans from an acoustic engineering perspective showed those living on the top floor might also have an unexpected additional feature—noise from the mechanical penthouse located directly overhead.
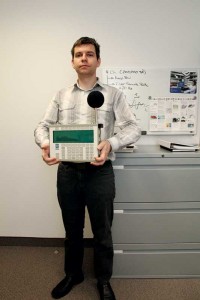
Photo courtesy Golder Associates Ltd.
It was clear to the acoustical engineers brought in to provide advice on this project that, as designed, the floor-ceiling assembly would not be enough to keep sound from the mechanical room above from reaching the unit below. Whether from the continuous noise of the building’s chillers or, even worse, when the diesel generator was operated as part of mandated monthly testing, the sound level would be such that the penthouse suite’s presumably well-heeled owners might make some legal noise of their own. This is one clear example of a design issue a good acoustical engineer could catch, preventing an expensive post-construction headache.
Importance of inspections
Having an acoustically certified design is not enough, as there is no guarantee the final construction will be built or perform exactly as designed. To address this concern, Tarion requires inspections and field testing take place to catch any acoustic deficiencies and verify performance before the building is handed over.
Since inspecting and testing every room of a large condominium is far from practical, acoustical engineers focus on a statistically representative sample of key risk areas. The number of inspections, along with the quantity and type of tests, is subject to Tarion’s approval, but also based on the expertise of the acoustical engineer.
Where the problems lie
In order to accommodate anticipated differences between design data and field performance, the onus is on the design team—which should include the acoustical engineer—to provide plans that hold up well during field testing. This approach may require designing suite walls, mechanical systems, and exterior façades to tighter tolerances than to which some developers are accustomed. As a result, achieving compliance is not always a straightforward matter.
Acoustic problems due to poor construction are increasingly common in condominium towers. Part of this is due to pressures on crews to reduce costs, possibly through cutting corners on materials and labour, or simply not understanding the nuances of acoustic construction techniques. These may show up when the unit’s occupants find they can hear their neighbours’ conversations, or are disturbed by HVAC, garbage chutes, parking garages, or elevator noise. Instead, a good acoustical engineer can identify these issues through site inspections or field testing.
As more urban infill units are built close to busy roadways, there is greater potential for exterior noise to intrude. Combine this with the floor-to-ceiling glazing popular in today’s condo market, and the potential for sound issues further increases. It is important the glazing’s acoustic performance be carefully specified to ensure both unit owners and condo developers will have restful nights.
With the increased prevalence of subwoofers in sound systems, and the growing popularity of wall-mounted wide-screen monitors with built-in rear-firing speakers, entertainment technology is playing a role in generating new types of potential noise complaints. As the guidance documents from Tarion suggest, buildings should be designed with respect to good acoustical engineering practices, addressing these new types of noise issues.
Overall, acoustics have come more to the forefront of Ontario builders’ consciousness with the inclusion of noise-related requirements in the home warranty program. Consequently, there is a lot more noise about noise, when it comes to high-rise condominium developments. How does a builder make it less likely acoustic considerations will force a costly retrofit, turning what could have been a profitable venture into a costly learning experience?