No Shell Game: Ensuring auditorium acoustics
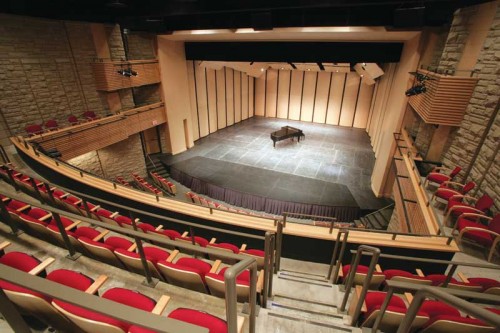
By Mark Ingalls
Attending a musical performance can be captivating. Listening to the beautiful sound and spectacle, the effortlessness of the musicians’ skills, it can be easy to forget the hours, months, and even years of practice that make the memorable performance possible. In a similar way, the factors behind successful auditorium acoustics often go unrecognized, including one of the most visible elements: the acoustical shell.
The most important considerations in a successful installation—acoustics, function, and esthetics—are illustrated in a unique project at the University of Western Ontario (UWO).
Disconnected spaces
To understand the important role played by acoustical shells, it is critical to first consider the architecture of typical auditoriums. The stage and audience area are usually separated by a proscenium opening, which provides a ‘picture frame’ through which the spectators watch the play, opera, or other dramatic production.
This was true of UWO’s Talbot Theatre, which was built in the 1960s on the school’s campus in London, Ont. Like most proscenium auditoriums, the Talbot featured a fly loft and rigging system above the stage, used for supporting lights, curtains, and stage scenery. While this setup is ideal for drama, it poses several acoustical challenges for music performance.
The proscenium opening makes an acoustical separation between the stage area and the seats—effectively creating two different acoustical spaces. Instead of reaching the audience, much of the sound produced onstage ends up lost in the fly loft above the stage or in the offstage wing space. Such conditions make it difficult for musicians to hear themselves and each other; this setup also compromises and diminishes the sound heard by the audience.
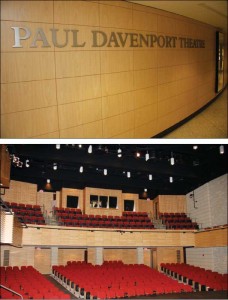
Photos © Paul Mayne, Western News
“Our music faculty overwhelmingly asked for ‘better sound’ when we were planning the Talbot’s renovation,” recalls Louis D’Alton, UWO’s concert manager. “So acoustics were our primary consideration.”
The school’s Don Wright Faculty of Music wanted the proscenium-stage hall to have acoustics more suitable for a range of performances. The existing acoustics were not very favourable for string ensembles and similar groups; D’Alton says the room’s small size meant the sound was often overpowering.
Auditoriums require sufficient volume to create the desired reverberance for pleasurable listening. Inadequate volume also results in excessive sound energy that makes listening difficult—even painful—for musicians and the audience. Acoustical shells cannot remedy a lack of volume.
“The volume of the Talbot Theatre was far too small,” says acoustical consultant John O’Keefe, principal with the Toronto acoustics firm, Aercoustics Engineering Ltd. “It would never be reverberant enough at its existing size.”
After considering several options, including installing an electronic enhancement system, UWO decided to demolish a floor of classrooms above the auditorium, enabling the room’s ceiling height to be raised by approximately 4 m (13 ft). This had the effect of increasing the room’s overall volume by 33 per cent.
Spaces connected
Acoustical shells serve to help connect the stage and audience areas, creating one larger acoustical space. Most acoustical shells consist of two elements:
- sound-reflective side and rear towers placed on the stage floor to surround the performers; and
- ceiling panels suspended from the overhead rigging system.
Together, the shell’s elements effectively seal off the backstage and above-stage areas, minimizing the leakage of sound into these auxiliary spaces and maximizing sound projection across members of the group and out toward the audience.
The benefits start onstage, where the music is created. The convex shape of the towers and ceiling panels helps scatter the sound. Both are constructed of a composite-panel honeycomb-core material that creates an acoustically reflective surface, effective across a broad range of musical frequencies.
This reflected sound enables musicians to hear themselves and each other better. In musical terms, the word ‘ensemble’ means more than just a group performing together; it describes a well-blended sound that unifies the collective.
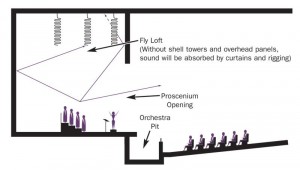
Images courtesy Wenger Corp.
While the full-stage shell creates a ‘blending chamber’ for sound on stage, it also helps reflect that blended sound out toward the audience. The positive impact is measurable. One study of three Canadian multipurpose halls showed acoustical shells increase the strength of sound by more than 3 decibels (dB) at many seat locations, which is about equal to doubling the size of the performing group. The effects onstage are even greater—more than 5 dB—according to findings published in the Journal of the Acoustical Society of America (JASA).
Since the Talbot’s renovation, the acoustical shell has enabled the hall to be used for larger ensembles, including the chamber and symphony orchestras.
“The shell has worked out well; we’ve gotten a good response from our users,” notes D’Alton.
“In our firm’s experience with modest-sized performance halls like the Talbot, the hall itself is like an instrument,” explains architect John Nicholson, principal with local firm, Nicholson Sheffield Architects. “Our design was intended to serve the sound and the varied programming needs of the university’s music department—everything from musical theatre to solo piano to large groups. The ability to use the space in different ways is paramount to maximize space and budget.”
The university has praised the results.
“The transformation is nothing short of amazing,” says Robert W. Wood, PhD, the Don Wright Faculty of Music’s dean. “A 45-year-old acoustic nightmare has been changed into a beautiful and acoustically superior performing space. There has been unanimous and high praise for the hall—we are thrilled with this incredibly successful transformation.”
Stéphan Sylvestre, the school’s assistant professor of piano and keyboard division co-ordinator, agrees.
“As a musician performing in the hall, the most important thing is the supportive environment and the inspiration that comes with the warmth and presence,” he explains. “Everything is more precise and clear since the renovation—no sound is lost.”
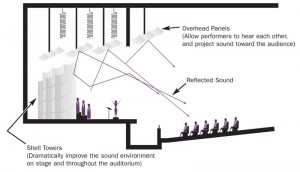
Sylvestre’s wide experience in the Davenport Theatre includes solo piano, a recent CD recording, and performing with other pianists. He has also attended orchestral and chamber music performances there. Sylvestre, whose numerous tours have visited concert halls, universities, and concert organizations through North America and Europe, also believes that the hall is now better in providing ensemble feedback.
“The sound envelops you and enables you to clearly hear every detail of articulation and tone colour,” he says. “As an audience member, there’s definitely much better clarity and sound projection to my ears.”
During various recent recording sessions, Sylvestre spent long days in the hall.
“You can almost tangibly touch the sound, like you’re swimming in it,” he explains. “This enables you to free your imagination more as a musician. Some halls are loud enough without any effort. You let go and the sound produces itself—it’s already there.”
A glove-like fit
While sharing many common characteristics, each full-stage acoustical shell is essentially customized to fit the unique requirements of the space and customer, meeting the goals established by the project team.
The Talbot Theatre’s shallow stage depth squeezed the available space for freestanding acoustical towers, so the three rear acoustical towers were permanently attached to the stage’s back wall, comprising a combined width of 11.2 m (36 ¾ ft). These towers did not require counterweighted bases. This meant only three movable towers were required on each side of the stage, which provided the additional benefit of reducing the space required for storing them. The ceiling panels are also unique—20 individual units, each 2-m (6 ¾-ft) squares, arranged in four rows of five panels, spaced 0.3 m (1 ¼ ft) apart. Each row measures 11.8 m (38 ¾ ft).
O’Keefe says that even with the increased volume in the renovated hall, there was a concern about the stage being too loud.
“We specified individual ceiling panels so the openings between them would allow some sound to escape,” he explains.
Typical ceiling panels are constructed in a continuous row, comprising a large rectangular panel wide enough to be suspended across the stage between the tower sections. Another advantage of individual ceiling panels is the ability to fine-tune the angle of each panel if desired. (Selected ceiling panels feature a hand-winch that allows its precise angle to be adjusted.)
“If you’re a violin player and your sound goes up and hits a flat ceiling, it’s not going to project to the other side of the stage very well,” O’Keefe explains. “Tilting the panels along the perimeter of the shell helps scatter the sound to the other side of the stage.”
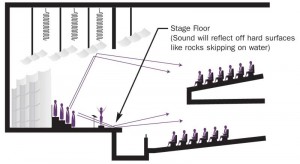
Smooth operation
In multi-use auditoriums like the Talbot, acoustical shells are reconfigured often to suit different performing groups. Therefore, shell features that enable easy operation and handling will speed transitions, facilitating a greater number of events and saving crew time and related labour expense.
The Talbot’s shell is reconfigured regularly in one of two primary setups: the full shell for large ensembles, or what D’Alton calls “music on the half shell”—the six towers arranged in an arc across the proscenium opening. This smaller setup, which uses only half the acoustical clouds, is for smaller concerts or recitals (of the latter, more than 200 are held at UWO every spring).
According to D’Alton, a four- or five-person crew can pull out the shell and reconfigure it in approximately four hours.
“The shell’s done a nice job—we’ve used it almost two years without any problems,” he explains.
Using a patented, electric-powered air caster, one crew member can move each of UWO’s 612-kg (1350-lb) shell towers from storage into performance position, and back again. Each tower incorporates a counter-weighted base for stability, and each base incorporates leveling feet that can be adjusted to accomodate any irregularities in the stage floor.
“The air caster is really remarkable; it’s a key advantage of this shell,” notes theatre consultant David Jolliffe, managing partner with Toronto’s Novita Techne Ltd.
Storage space onstage is always at a premium. When not in use, the seven towers nest compactly in an area stage-left that measures only 2.3 x 3.3 m (7 2⁄3 x 10 2⁄3 ft); floor structuring in this area of the stage was reinforced to support the load. Jolliffe says it is equally important to ensure the ceiling panels can store compactly when tipped and flown up in the rigging—the Talbot’s shallow stage meant rigging space was limited.
Both the towers and ceiling panels feature framework constructed of aluminum extrusions, which are lighter and structurally stronger than steel. As the aluminum extrusion serves as a truss, fewer hanger arms are required to secure the ceiling panels to the rigging. Self-lubricating bearings are used for everything that rotates, such as ceilings, stage doors, and the tower wings.
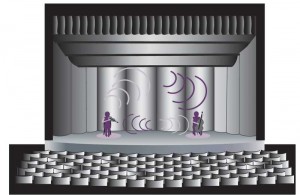
Enhancing esthetics
Acoustical shells are often considered ‘portable architecture’ because of their exquisite level of detail and exacting construction standards. Such shells often serve as visually stunning ‘crown jewels’ of the performance space.
The Talbot Theatre’s shell fits this particular description, visually complementing and reinforcing the auditorium’s overall design by incorporating similar materials, colours, and finishes into the construction.
“We wanted the Talbot’s shell to maintain continuity of esthetics throughout the renovated space while also answering acoustic needs,” says Nicholson, who explains the fan-shaped auditorium previously featured walls and a balcony front finished in walnut panels.
“When reimagining the space, we brought in the walls to square the hall and introduced a harder, more massive, and more textured building material to better meet the acoustical requirements—stone similar to the building exterior,” he continued.
In the renovated interior, birch wood is featured on many profiles and finishes, including the proscenium arch and acoustical shell itself, which is finished in a warm-looking birch veneer. While each acoustical shell is custom, manufacturers can offer a high degree of repetitiveness in the engineering in order to make the process even more cost-effective.
Conclusion
The best acoustical shells balance memorable esthetics and innovative technology to create beautiful results, satisfying to both the eye and the ear. The collaboration involved among members of the project team—owner, architect, acoustical consultant, theatre consultant, and shell manufacturer—is similar to the musical teamwork that takes place onstage.
“It was a very enjoyable project—quality work, working with quality people,” recalls O’Keefe. “Everyone wanted to do things right, everyone was willing to listen and learn, and the final result was wonderful.”
Now known as the Paul Davenport Theatre, the space formerly named the Talbot will continue its role as a cultural cornerstone for both the University of Western Ontario and the city of London.
(See J.S. Bradley’s “Some Effects of Orchestra Shells,” in JASA vol. 100 (2), Pt. 1 [1996]).
Mark Ingalls is a product manager for the performing arts with the Wenger Corporation, a manufacturer of equipment and furniture for music education and the performing arts. During his 23-year career at Wenger, Ingalls has also managed the company’s applications engineering department. Wenger offers a free 34-page planning guide outlining basic acoustical principles impacting many common performance spaces, along with a list of other resources. Ingalls can be reached at mark.ingalls@wengercorp.com.