New spray foam regulations: What you should know
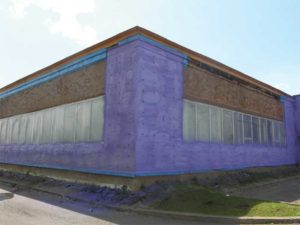
By Gary Chu and Michael Pace, CET, BSS
Spray foam is a frequently specified insulation in Canadian construction. The versatility, reliability, energy-efficiency, and safety profile of spray foam has made it an effective choice for all types of buildings, including residential, commercial, industrial, and institutional.
Spray foam offers several advantages. Its inherent ability to expand and form a monolithic layer of insulation allows it to effectively fill and seal around pipes, studs, and joints. Combined with its ability to eliminate conductive air movement in and out of the building and energy efficiency potential with high R-value, spray foam offers unique benefits. Additionally, its structure and chemistry make it virtually impervious to dust, moisture, fungi, and mould issues. Spray foam’s ability to act as an insulation, air barrier, vapour barrier, water barrier, drainage plane, weather barrier, and radon barrier—in a single product—showcases its functional versatility, achievable only by the nature of its chemistry.
Evolving for ever-improving environmental efficacy
While the benefits of spray foam insulation technology have been well-established in millions of buildings for more than half a century, its chemistry continues to evolve as spray foam raw material suppliers develop chemistries with improved environmental profiles. The focus of this pursuit has primarily been the blowing agent component of spray foam—the gasses that expand the material during installation to create the ‘closed cells’ of the foam. This expansion of approximately 20 to 40 times the liquid volume enables the foam to effectively fill all areas before hardening into its rigid, impermeable final form.
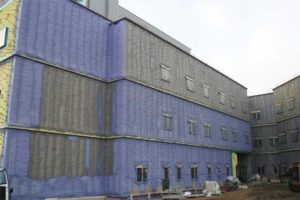
The original blowing agent used in spray foam applications circa the 1960s contained chlorofluorocarbons (CFCs), which were replaced by hydrochlorofluorocarbons (HCFCs) in 1990, and subsequently, replaced by hydrofluorocarbons (HFCs) in 2010.
Now, the development of next-generation blowing agents has elevated spray foam to a new level. On January 1, 2021, the regulatory elimination of HFCs, driven by the Kigali Amendment to the 1987 Montréal Protocol, will come into effect. According to the federal regulation, blowing agents with a global warming potential (GWP) of greater than 150, including HFCs used in foamed plastics (e.g. spray foam, extruded polystyrene [XPS]), will be banned.
The current chemistry found in blowing agents is being replaced by hydrofluoroolefins (HFOs), a substance with near zero contribution to both ozone depletion and greenhouse gas (GHG) emissions. This phase-out of HFCs will result in a significant reduction in environmental impact.
Action 1: Learn about the chemistry
As noted earlier, the blowing agent component of spray foams has evolved over the years to address growing environmental knowledge and stricter regulations. The driver in this regard has been the Montréal Protocol of 1987, a highly successful and far-reaching global treaty working to phase out ozone-depleting substances, or ones degrading the stratospheric ozone layer that helps keep harmful ultraviolet (UV) radiation from reaching the Earth’s surface. CFCs, for example, the blowing agent used in original spray foams in the 1960s, had a high ozone depleting potential (ODP). Their removal and replacement with HCFCs in 1990 effectively reduced the ODP of spray foam by some 90 per cent, and HFCs, coming onboard in 2010, brought the ODP down to near zero. HFOs likewise are considered to have zero ODP.
Spray foam suppliers have been working for the past four or five years to replace HFCs by the January 1, 2021, deadline. HFOs, substances determined to have a negligible contribution to global warming potential (GWP), will become the new blowing agent.
What does this all mean to the specifier? Start specifying only foams using HFO blowing agents immediately. For projects that will be partly or entirely sprayed after January 1, 2021, specifications should include only HFO foams to avoid employing multiple formulations in a single project. With HFO-based chemistry, building professionals will now have all the benefits of spray foam as well as a reduced impact on the environment by 80 per cent less GWP.