Nailing down a quality hardwood floor with OSB
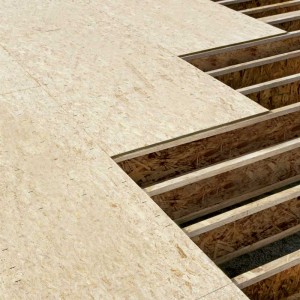
To protect the hardwood flooring from absorbing moisture before installation, it is crucial to keep materials covered before and during delivery, and then wait to deliver the flooring until after the building is enclosed and the temperature and humidity conditions match occupancy levels. It is also important to unwrap the flooring and allow it time to adjust to the interior heated/air-conditioned environment per the manufacturer-recommended acclimation period.
As with testing the OSB subfloor, it is also important to use a good-quality moisture meter to confirm moisture levels in the hardwood flooring before installing it. NWFA recommends sampling the moisture in 40 individual boards for every 93 m2 of flooring.
NWFA also recommends installing hardwoods only when MC is within four per cent of that of the subfloor for solid strip flooring less than 76 mm (3 in.) wide. The recommendation for wide-plank flooring (i.e. wider than 76 mm) is to ensure moisture levels are within two per cent of the substrate’s moisture content before installing the flooring. Recommended moisture differential values for engineered hardwood flooring might vary from these figures, as these types of products incorporate a mix of wood species or components. (The manufacturer should confirm this.)
Subfloor preparation
After the OSB and hardwood flooring are adequately dry, and the hardwood flooring has been acclimated, it is important to evaluate the subfloor’s surface condition before flooring installation begins. Careful inspection can help determine a floor’s short- and long-term performance. Conditions to evaluate include:
- subfloor panels’ proper attachment to the underlying joists—in other words, whether there are any missing or misplaced fasteners (e.g. ‘shiner’ nails or screws);
- panels with edge swell or delamination;
- presence of contaminates or debris that might interfere with flooring adhesives; and
- surface irregularities, such as popped nails.
In addition to visually inspecting the substrate above and below, it is important to walk the floor in all areas and multiple directions. This can help detect loose panels, excessive movement, and squeaks that can be fixed before the floorcovering is installed.
Additional subfloor preparation includes:
- sanding the surface to manufacturers specifications, as needed (some premium OSB floor panels are factory-sanded to help eliminate this requirement);
- removing contaminants, such as excess adhesives, oil, and grease; and
- sweeping, vacuuming, and cleaning.
It is also critical to ready the substrate for the specific flooring selected. For instance, some hardwood flooring products require covering the subfloor with a quality-grade 6.8-kg (15-lb) asphalt felt/building paper lapped 50 to 100 mm (2 to 4 in.) along the edge seams to minimize dust, reduce moisture movement, and prevent squeaks in dry seasons.
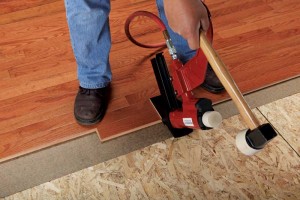
Beyond the subfloor
Oriented strandboard can accommodate glue-down, nail/staple, or floating hardwood installations. This makes it possible to install a wide array of hardwood species and flooring types, solid strip or engineered. Since hardwood flooring performance varies by wood species, flooring type, and manufacturer, it is important to consider several factors when choosing products.
Location
A floor’s location within a building can determine the amount of foot traffic it must withstand. Hardwood floors in a restaurant dining room, for instance, are exposed to frequent movement of waiters, customers, and chairs, as well as dropped dinnerware. In such applications, harder and denser woods are typically preferred given their better wear resistance. Woods that surpass red oak on the Janka Ball Hardness Test (i.e. 8894 kPa [1290 psi])—the industry benchmark for wear resilience—are more durable. Examples of hardwood species that exceed this threshold include ash, sapele, ipe, mahogany, and eucalyptus.
Another option for highly trafficked commercial applications is engineered hardwood flooring. Designed to provide greater stability, particularly where moisture or heat might pose problems, engineered hardwood materials resist cupping, swelling, and splitting.
Although it is reasonable to expect dense or engineered hardwood flooring options to withstand scratches and dents longer than softer hardwoods, it is important to note all hardwoods are susceptible to wear over the long term. Applying a protective wood finish, such as phenolic or polyurethane varnishes, can enhance the
flooring’s durability.
Surface appearance
A hardwood’s visual characteristics—including grain pattern, colour, growth marks, and plank size—help support interior design schemes. Dark tones are a primary choice within contemporary styles, as confirmed by a 2010 USDA Forest Service study, “Enhancing Utilization of Hardwoods in the Eastern U.S.,” which found consumers prefer dark-toned eucalyptus and cherry hardwoods. As esthetic preferences can change over time, it is important to select woods with good sanding and re-staining properties.
Wood species such as eucalyptus and others that can absorb various stains—from oil- to water-based finishes—can be re-stained for a new look or returned to their original colour. While engineered hardwood flooring has less flexibility for refinishing than solid strip flooring, sanding and refinishing engineered products is possible with those that have a wear layer (typically 3.175 mm [1/8 in.] thick).
Maintenance
Periodic cleaning of installed hardwood flooring per manufacturer recommendations is essential to maintaining long-term beauty. Generally, a hardwood’s finish—either surface or penetrating—determines maintenance levels. Hardwood floors with penetrating treatments typically only require a weekly sweeping or dusting, and occasional application of a no-wax floor cleaner. To repair deep scratches or heavy wear, one should refer to the manufacturer’s guidelines or consult with a qualified floor care professional.
It is also important to note hardwoods often contain certain acids in their cellular structure that begin to amber when exposed to sunlight. Known as ‘patina,’ this colour change is not a defect and varies by wood species. The wood will reach its own natural warmth and patina level and stop ambering after a certain period.
Conclusion
The increasing number of buildings that use oriented strandboard panels for an enduring platform evidences its success as a subfloor material. It is strong, consistent, and dependable, and can help enhance subfloor performance and the long-term beauty of an overlying hardwood floor. As with other subfloor materials, appropriate moisture management is essential for a top-notch finish.
Chris Degnan is the oriented strandboard (OSB) product manager for Weyerhaeuser, which supplies structural frame and finish materials, including Edge Gold OSB floor panels and Lyptus eucalyptus solid and engineered hardwoods. He has 25 years of experience in the building products industry. Degnan can be contacted via e-mail at chris.degnan@weyerhaeuser.com.