Myth versus reality: Revealing the curtain wall capabilities of modern steel
Myth 1: Steel frames are likely to corrode
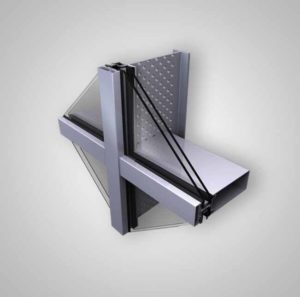
Image courtesy TGP
Among the most common misconceptions about steel is the carbon alloy is unsuitable for use as a primary framing material due to corrosion. Indeed, early steel curtain walls were vulnerable to rust, and the industry turned to more corrosion-resistant materials, such as aluminum, by the mid-1900s. Especially in a country largely subjected to freezing winters with heavy snowfall, those in the design-build sector are rightfully wary of building materials that cannot stand up to moisture and air, two of the main catalysts for corrosion.
The Europeans have led the way in developing systems that eliminate much of the water and steel contact in glazing systems. Water is typically present in the glazing pockets, where the glass is captured along its edges, to hold it onto the framing system. The means of capture employs gaskets, since metal to glass contact would not create the necessary air and water seals required by specification. Pioneering a solution, the Europeans took the gasket at the face of the primary framing member, which forms the interior portion of the glazing pocket, and entirely covered the face of that steel with the gasket, completely removing any possibility of water coming into contact with the steel. Water from other portions of the façade, such as the perimeter interface with surrounding construction or from the surrounding construction itself, is precluded by intelligent detailing and execution of those conditions. The governing principle is water should not come in contact with the steel, and the systems themselves address water isolation from steel internally.
This has allowed steel to become a more suitable material for consideration as a glazing system framing material. Notably, steel frames do not require cladding or reinforcement to support expansive captured and non-captured curtain wall systems. When properly sized, the primary frame members can serve as structural elements, although this would require co-ordination with the general contractor (GC), structural steel fabricator/erectors, and glazing subcontractors. A wide variety of finishes are available, from powder-coating to liquid-applied coatings. However, it is the glazing systems that typically isolate the carbon steel from coming into any contact with water.
Weather seals, moisture protection, and ASTM E331
The gasketing methodology employed by these systems has been the major contributor to steel’s comeback in curtain wall applications. With the addition of a continuous gasket covering the full width of the steel face, steel back members are now isolated from water within the glazing pocket (Figure 2).
Specifically, gaskets are typically ethylene propylene diene monomer (EPDM) rubber or silicone. While manufacturers handle sealing gasket joints at framing members in different ways, many overlap and seal gasket joints at framing member joints at intersections. This further prevents moisture intrusion. Any water collecting in the glazing pocket is redirected to the sill of the opening, or at intermediate locations in tall vertical members (greater than 6000 mm [236 in.]), where the water is then weeped out of the glazing systems. The glazing pocket is also free of metal, supporting condensation resistance.
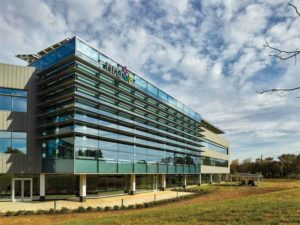
Photo © Jeffrey Totaro
As for whether or not steel-framed curtain wall systems meet third party, independent laboratory testing, it is important to examine steel’s performance as per ASTM E331, Standard Test Method for Water Penetration of Exterior Windows, Skylights, Doors, and Curtain Walls by Uniform Static Air Pressure Difference. With ASTM E331, water is applied to both the outdoor face of the curtain wall and opening perimeter joints to adjacent materials at the same time. The static air pressure is kept uniform, though the air pressure at the outdoor face is higher than the pressure at the indoor face. While all of this is occurring, the curtain wall’s level of resistance is measured. Under these requirements, steel glazing systems have met zero water penetration when tested at 718 to 1436 Pa (15 to 30 psf).
Air protection and ASTM E283
Equally important to corrosion prevention is resistance to air penetration. When oxygen comes into contact with water on a steel surface, the rusting process begins.
Fortunately, the continuous gasketing mentioned above in relation to water penetration also prevents air from entering through the steel curtain wall systems to the occupied, interior, conditioned air spaces. In essence, the gaskets form a tight, protective seal against air penetration. Installers commonly utilize pressure plate systems as a two-line resistance strategy for air and water penetration. Functionally, pressure plates with self-sealing fasteners keep the glass in place. They also help maintain adequate pressure on the glass, gaskets, and framing, creating the seals necessary to meet the air and moisture resistance mentioned above.
Steel can meet ASTM E283, Standard Test Method for Determining Rate of Air Leakage Through Exterior Windows, Curtain Walls, and Doors Under Specified Pressure Differences Across the Specimen, requirements. According to the test method’s scope, “This test method covers a standard laboratory procedure for determining the air leakage rates of exterior windows, curtain walls, and doors under specified differential pressure conditions across the specimen. The test method described is for tests with constant temperature and humidity across the specimen.” When tested with a pressure differential of 299 Pa (6.24 lb/sf), a steel curtain wall’s air leakage has been consistently measured at 0.005 L/s of wall area.
These airtight framing capabilities also debunk another myth that is associated with steel products—poor energy efficiency.